chiptim
Part of the e-furniture
Posts: 270
|
Post by chiptim on Jul 16, 2009 20:38:26 GMT
Can anyone advise me what to do here please? I've E-Mailed my boiler inspector but think he's away at the moment and I'm keen to get on. The throat plate as specified doesn't have a flange for the barrel. This causes the gap due to the radius of the side flanges for the wrapper. I think it's too big to fill with solder. Should I: 1). file the end of the barrel to this profile 2). bend the ends of the throat plate up a bit and file square or 3). fill with some copper trimmings prior to soldering? 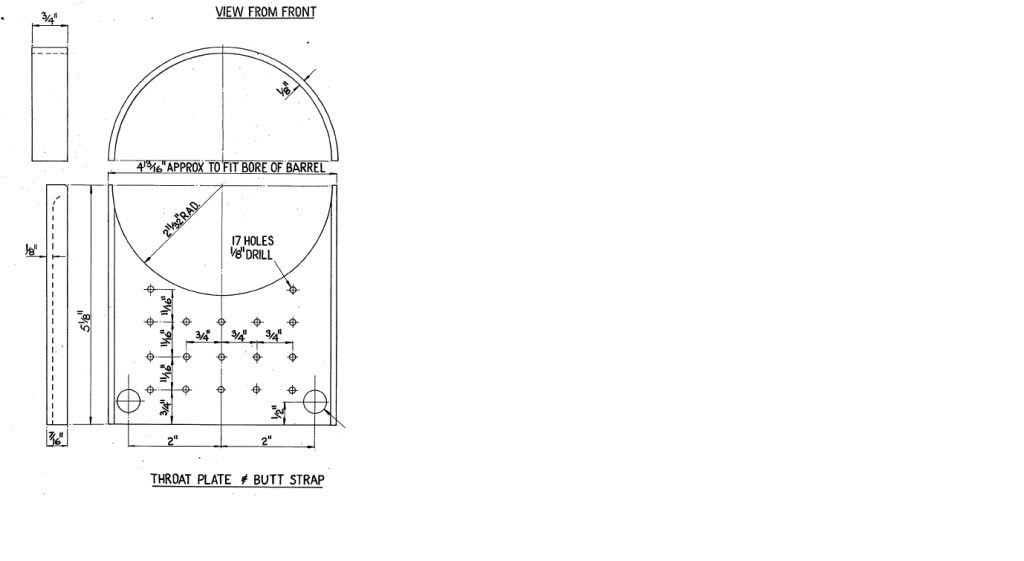 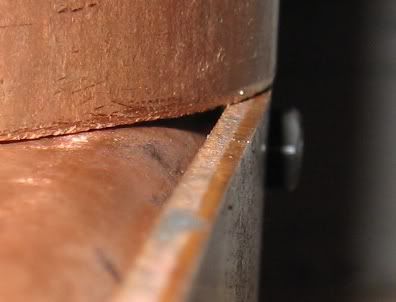 Regards Tim
|
|
|
Post by mutley on Jul 16, 2009 21:09:14 GMT
Hi Tim, Are you using a seperate outer wrapper for the firebox or is it an extension of the barrell? You could use a seperate formed plate on the inside of the barrell similar to if your flanged throat plate had been designed to attach to the barrel.
Andy
|
|
|
Post by Shawki Shlemon on Jul 17, 2009 9:20:00 GMT
The way I understand it, this is a round top boiler and the wrapper is part of the barrel . I have made a few of these in the past but I always form a forward flange to meet the barrel and sometimes is necessary to add a small inside strip as mutely mentioned above . If the gap is large as it seems , silver solder will not fill the gap.Generally if there is no flange brazing is the answer as you can fill gap with it better than silver solder .Whatever you decide to do , I think the best is to consult ( wait for him ) with your boiler inspector before going ahead to avoid any disappointment .
|
|
chiptim
Part of the e-furniture
Posts: 270
|
Post by chiptim on Jul 17, 2009 11:37:17 GMT
Thanks for your replies. Yes there's a seperate outer wrapper that joins to the barrel with the butt strap shown in the diagram. This will overlap both barrel and wrapper by 3/8" so it seems a bit strange that the barrel/throat plate join will only have the thickness of the barrel to form a joint which is 13 or 14 SWG so well less than 1/8". So aside from the gap that I will wait for the boiler inspector to address, it seems strange that all major seems other than this one have a flanged face to form a reasonable depth of joint. In the diagram, do you think the dotted line at the top of the vertical side view is supposed to indicate a bit of an inward flange? I did consider this but if it were so it would require the top of the barrel (join to outer wrapper) to be shorter than the bottom (that would need to reach into the flange) and the drawings don't seem to show this. Tim
|
|
simonwass
Part of the e-furniture
Cecil Pagets 2-6-2 of 1908. Engine number 2299. Would make a fascinating model....
Posts: 472
|
Post by simonwass on Jul 17, 2009 12:10:18 GMT
I'd just use an 1/8" square infil piece to go in the corner of the throatplate and the barrel, this creates a stronger join as there is more surface area for the silversolder to stick to. Use some snippets of copper to go into the gap to stop the silversolder running through. A proper flanged join is better but at least you have the throatplate on the end of the barrel so it is always under internal pressure.
|
|
|
Post by mutley on Jul 17, 2009 12:14:06 GMT
Hi Tim, As your outer wrapper is seperate and you are using an internal strap to join the two you have an easy option. Make the internal strap a ring and dress the bottom portion down to form a flange that the throat plate can attach to. If you then solder from the inside out you can ensure full penetration of the joint by checking it has appeard at the butt joint externally. I've got some pictures at home of my Simplex boiler that I did this way. I will try and find and post them later. regards
Andy
|
|
chiptim
Part of the e-furniture
Posts: 270
|
Post by chiptim on Jul 20, 2009 11:06:17 GMT
Simon, Andy,
thanks for your replies. More options than I originally though of and I'll let the boiler inspector advise me...but he's still not back!
Never mind, there are other parts I con work on in the meantime.
Tim
|
|
chiptim
Part of the e-furniture
Posts: 270
|
Post by chiptim on Aug 11, 2009 18:01:17 GMT
Problem solved - my boiler inspectors' advice was to profile the barrel to fill this gap which I have now done but the photo didn't come out well! So instead here's a photo showing how it's coming on. It's all held together with Pb screws at present. 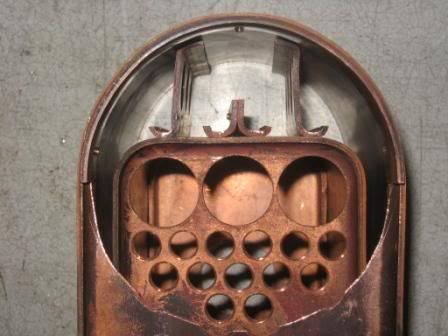 Regards Tim
|
|
redmog
Part of the e-furniture
Not Morgan weather
Posts: 461
|
Post by redmog on Aug 11, 2009 20:14:54 GMT
Whos Idea's That?
Interesting how these girder stays meet the firebox crown! Now whos idea's that? I can see the thinking behind it.
|
|
chiptim
Part of the e-furniture
Posts: 270
|
Post by chiptim on Aug 11, 2009 21:19:37 GMT
It's a "Jesse" boiler by Ken Swan. Is that unusual then? Bear in mind it's my first loco and boiler and I'm working largely in isolation so I've nothing to compare with. I'm building it to the drawings. Regards Tim.
|
|
redmog
Part of the e-furniture
Not Morgan weather
Posts: 461
|
Post by redmog on Aug 11, 2009 21:32:08 GMT
New to Me. It's a "Jesse" boiler by Ken Swan. Is that unusual then? Bear in mind it's my first loco and boiler and I'm working largely in isolation so I've nothing to compare with. I'm building it to the drawings. Regards Tim. Sorry Tim - I didn't mean to cause any concern. I'm not familiar with the boiler and had not seen the practice of the girder crown stays having a curved surface where they meet the firebox crown. Goes to show - What do I know. Chris
|
|
chiptim
Part of the e-furniture
Posts: 270
|
Post by chiptim on Aug 12, 2009 7:37:37 GMT
They weren't the easiest items to form but I had previously asked to replace them with a sieries of long copper rivets on the same spacing as the flate sides and the response was negative hence why I stuck to the drawings. I believe they're one of the more challenging joints to solder but no doubt I'll find that out for myself soon !
Regards Tim
|
|
|
Post by havoc on Aug 12, 2009 10:22:14 GMT
Was any reason given?
|
|
chiptim
Part of the e-furniture
Posts: 270
|
Post by chiptim on Aug 12, 2009 10:52:21 GMT
As stated the response was negative and I didn't question this decision but from memory I think he stated that this would have constituted a change to the original design and therefore required calculations to verify it as suitable - but it is commonly seen so presumably accepted by some boiler inspectors which was why I suggested it in the first place! Regards Tim
|
|
simonwass
Part of the e-furniture
Cecil Pagets 2-6-2 of 1908. Engine number 2299. Would make a fascinating model....
Posts: 472
|
Post by simonwass on Aug 12, 2009 14:47:27 GMT
Although there will be many Jessie / Bridget boilers out there, the join of the crown stay to crown is a poor one. You are not getting much contact between the two parts and will use lots of silver solder to fill the radius. They would be better if the outer radius is folded flat, the join would be 2 - 3 times stronger using less silver solder. Any boiler inspector who views this negatively shouldnt be in his position. Also the negative comment regarding rod stays is strange as it is now accepted if not prefferred to flat sheet stays. The problem with proving suitability with regard to strength is never going to go away though, copying a similar modern boiler design should be fine, the GWR Collett 0-6-0 uses rod stays, diameter, spacing & plate thickness given same boiler pressure is confirmation of suitability.
|
|
|
Post by havoc on Aug 12, 2009 17:22:43 GMT
I'm glad at least 2 feel the same as I do about girder stays.
|
|
chiptim
Part of the e-furniture
Posts: 270
|
Post by chiptim on Aug 13, 2009 7:31:28 GMT
I agree that rod stays or long copper rivets looked an easy modification to me however maybe there's a valid reason for this decision which was simply that because we have never met and he knowns this is my first boiler, there exists an element of doubt that I would get the modification correct (i.e. fitting rod stays) hence easier to just follow the drawings and reduce the scope for getting it wrong? There's some arguement in the fact that there are other tricky soldering steps that I will have to get right other than the crown stays. I'm not about to list any names and in the situation that I am in will trust the advice I have received that he is a reputable boiler inspector with lots of experience. So moving on there is still something to discuss because I don't fully understand the previous comment... Can you explain the bit about flattening the crown stays? As I see it the tops of the crown stays are curved with the inside radius of the outer wrapper so this offers a large contact area. If the gap were uniform at 6thou (which of course it won't be but they're not bad) then it wouldn't require huge amounts of silver solder to form this joint. Am I missunderstanding something here? Regards Tim.
|
|
redmog
Part of the e-furniture
Not Morgan weather
Posts: 461
|
Post by redmog on Aug 13, 2009 10:01:03 GMT
Slight Misunderstanding! Hello Tim. I think there might be a misunderstanding. When I made comment about the girder stays being unusual I was referring to the area I have circled in red on the drawing below. I am only familiar with the bottom of the girder stays being almost flat and meeting the firebox on a flat..ish or slightly curved surface. Chris 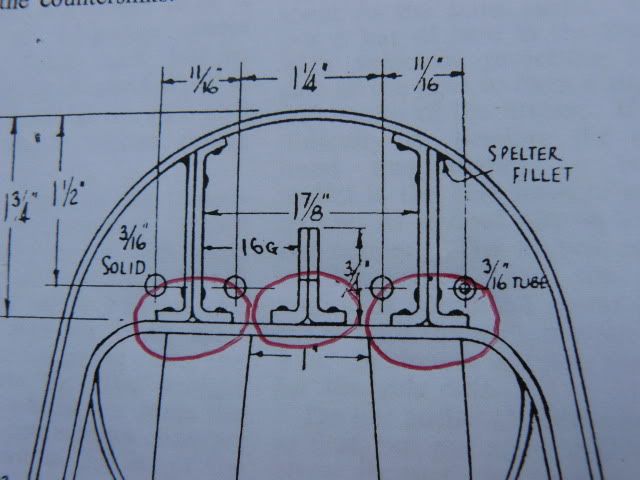
|
|
|
Post by Shawki Shlemon on Aug 13, 2009 10:14:31 GMT
Crown girder stays are permitted in the OZ code with certain restriction such as for small boilers with 3.75" barrels or less Z type are permitted and boilers of larger sizes must have double plate construction plus there are rules for distances and water circulating holes. I can't place the page here for obvious reasons but if you want a copy of the page send me your email by PM and I will email it to you .
|
|
chiptim
Part of the e-furniture
Posts: 270
|
Post by chiptim on Aug 13, 2009 19:46:38 GMT
Silly me! Yes that's clear now. The photo is taken at a slight angle and doesn't show that there is a slight flat section on the bottom but the copper was so thick this was hard to achieve. The drawing shows 7/16" width at the bottom with a considerable flat section. In reality there's just under 1/4" flat section but hopefully the solder will form a muliscous either side down the length effectively widening this contact area. Thanks for all your replies. I've been lent the Alec Farmer book. He advocates fabricating crown stays from scrap flat sheet using high temperature silver solder. So the bottom would be perfectly flat using this method. I'm off on holiday on Saturday, hopefully some practice soldering the week after I return! Regards Tim.
|
|