|
Post by Deleted on Dec 3, 2009 17:56:22 GMT
Just to let you know that I haven't been idle between boilers. I started working on the brakes, as cutting metal is something I can do OK! As I haven't posted pics for a bit, here is the story so far. The brake cylinder is made from a spare piece of manganese bronze; the actuating arms are stainless (yes, I know, I'm a masochist!). Today's job was the hangers, brake beams and connecting forks. All pretty straightforward stuff, but I would have really liked a 1/4" Sq collet for the machining of the forks!  When I have a few similar items to make, I tend to make one completely, just to see what problems may occur, and also to spot ways of making subsequent items a little quicker. These hangers were drilled in the vice, located against a thin piece of steel. One end was drilled, and the piece then turned end for end and drilled again, then the next piece, and so on. The centre hole was done in another sequence. These were all drilled with a No. 30 drill without centre potting/ spotting or centre drilling. If the surface is smooth, perpendicular to the drill, and the drill is ground correctly, a drill of this size should spot itself quite satisfactorily. As you can see, they all fit together nicely.  We then get to the inevitable hand stuff (what am I saying!). Buttons are dead handy: I've given up trying to machine round this sort of thing. Only five more to make! BTW, it is a good idea to get rid of the steel jaws and make some ally ones.  Looks like I will get the boiler quicker than I thought: look out Chris! JB
|
|
kwil
Part of the e-furniture
Posts: 383
|
Post by kwil on Dec 3, 2009 18:59:31 GMT
Cannot be much demand for their boilers, is this good or bad I ask? Looking forward to hearing of your experiences in this matter.
|
|
|
Post by Deleted on Dec 3, 2009 19:02:56 GMT
Cannot be much demand for their boilers, is this good or bad I ask? Looking forward to hearing of your experiences in this matter. They are quite busy Kwil. Marco is doing me a big favour on both price and delivery, and I will, of course, be posting my progress with this TIG welded boiler. JB
|
|
|
Post by Deleted on Dec 4, 2009 21:28:50 GMT
This afternoon's job was to finish the brake hangers. I found a nice little side and face cutter of the right diameter to take away most of the filing: belay what I said yesterday about filing buttons! If you look closely you'll see where I used yesterday's master to draw the outline on the stack. The dowel pins ensure that the stack sits level.  Roughly filed to shape whilst still on the stack. Buttons aren't needed because it is wide enough to support a smooth 12" file. It's a good plan to use the largest file that you can fit to the job.  Six nice little hangers, individually finished on the Proxxon BF40. I do enjoy this sort of stuff, it's much easier than boilermaking......! JB 
|
|
|
Post by drumkilbo on Dec 4, 2009 21:42:38 GMT
Simply beautiful JB.
|
|
|
Post by bigt1677 on Dec 5, 2009 22:01:40 GMT
Very useful, lovely uniform finish.
|
|
|
Post by Deleted on Dec 13, 2009 18:13:11 GMT
Last component: the brake shoesI managed to crack a few of the original shoes that were supplied in stick form: I'm not used to dealing with small castings. I couldn't locate a cast ring of the correct size at sensible money, but as the Brit shoes don't actually do anything I found this nice lump of high grade alloy to carve up! Those who are old enough will be reminded of the Popeye cartoon where a huge vertical borer is producing cufflinks from foot square billets! I chose this approach because it permits ALL of the machining operations to be carried out at one setting: matching of the wheel radius; slimming the shoe to put on the shoulder which was absent from the castings supplied, slotting for the hangers, and parting off to width. Voila! Initial boring and facing.  Slotted for the hangers using a 3/32 parting blade; they fit!  Prototype filed up and fitted. I hope you'll agree that it looks a little better than the scabby casting shown in the picture! Or am I supposed to achieve the same thing with it somehow? I'll make another four tomorrow. The more observant will spot my deliberate mistake: the hanger pins are 1/8" too short, yet another senior moment..... This scale thing is very interesting, but may lead to my downfall! JB 
|
|
|
Post by mutley on Dec 13, 2009 20:24:14 GMT
looking good!! 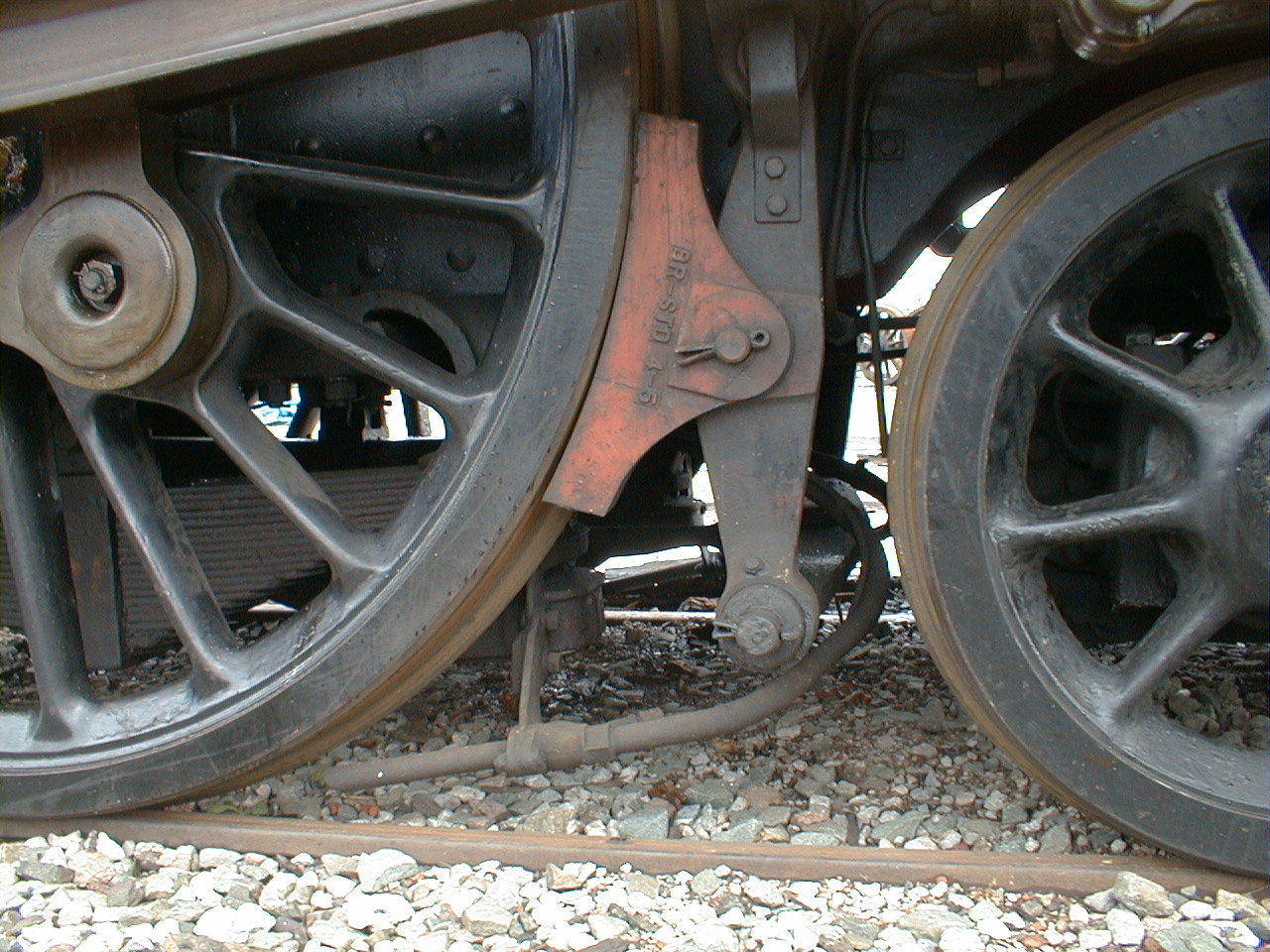
|
|
|
Post by welshy on Dec 14, 2009 21:39:13 GMT
Yes nice work there JB. Looking better by the day. Mike
|
|
|
Post by arch1947 on Dec 15, 2009 20:18:09 GMT
G'Day JB, Nice work, I certainly learn a lot from this forum and the photos are excellant. I have a question about how you made the brake beams?? that connect to the bottom of the hangers. It looks like you have cut them from flat and then turned the "pin" before maching the taper on the sides. Is this correct? I am in the process of building the tender for Virginia and brakes are part of that exercise hence my question. Keep up the good work, Arch
|
|
|
Post by Deleted on Dec 15, 2009 21:22:15 GMT
Hi Arch! Yes, the brake beams were made from 1/2" X 1/8" MS plate, hacksawn to rough length, and accurately sized in the 4 jaw against a stop in the headstock spindle. The end of one piece was was marked out and centre popped, centred in the the 4 jaw against the spindle stop, and machined and threaded. Turn it round and repeat, etc.etc. The tapered sides were then filed, and finished on the linisher.
I should have photographed that sequence, as I use the 4 jaw a great deal and perhaps a few others could have been interested in that bit. Apologies!
BTW the brake shoes were done in the 4 jaw, more to see if it could be done that way, rather than it being the optimum method! JB
|
|
|
Post by Deleted on Dec 18, 2009 20:01:58 GMT
looking good!! 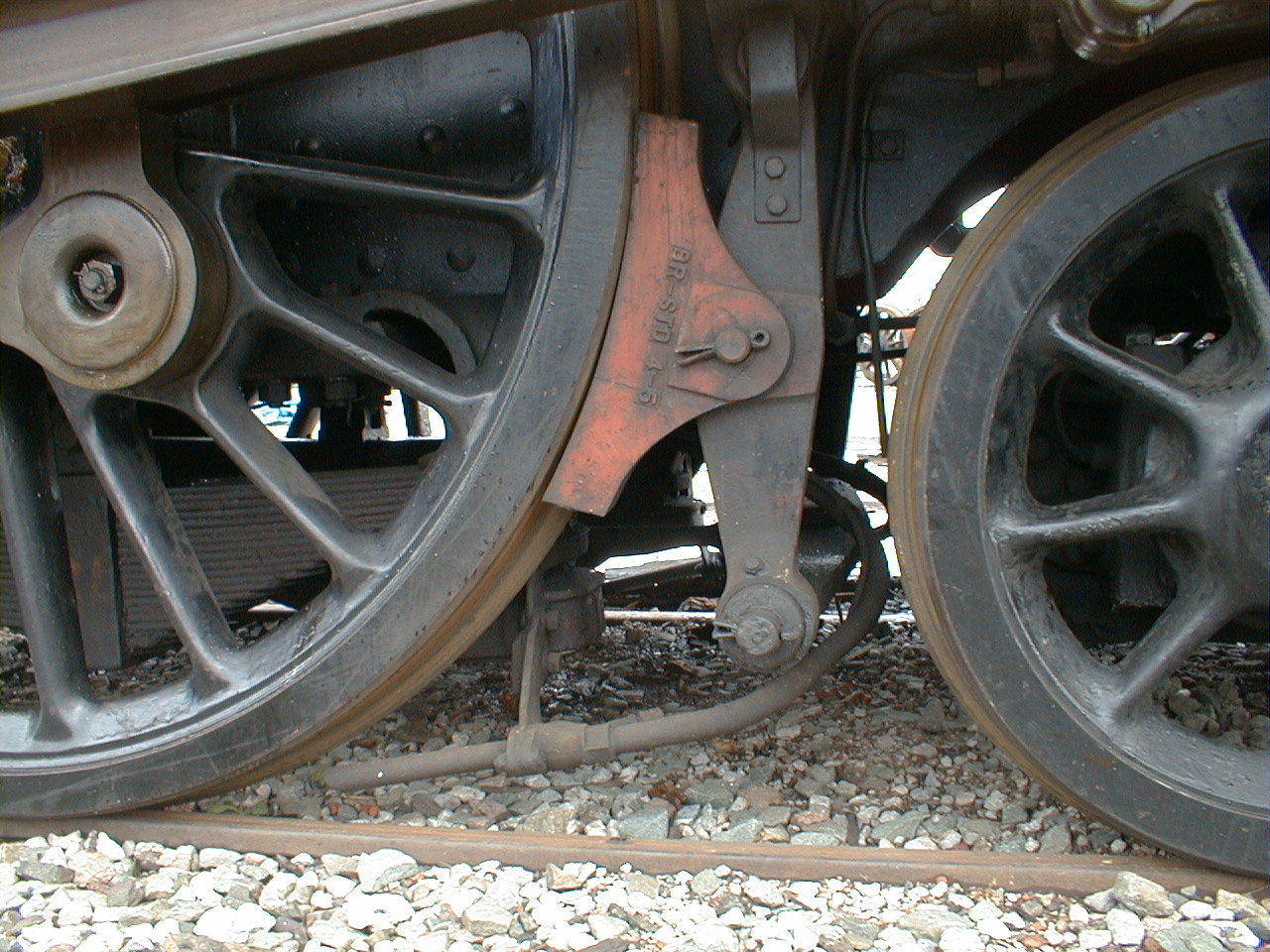 OK, on the subject of scale, and to try and emulate the above, I'll do a Jeremy Clarkson impersonation: "Who thinks that JB's home made split pin looks better than Curly's nuts..........?" ! JB  
|
|
davidm
Seasoned Member
Posts: 109
|
Post by davidm on Dec 18, 2009 23:03:09 GMT
Those split pins DO look good. What size are they & where do you get them from, please.
David
|
|
|
Post by Deleted on Dec 19, 2009 9:28:52 GMT
|
|
isc
Statesman

Posts: 708
|
Post by isc on Dec 19, 2009 10:09:08 GMT
You can make your own half round wire,take a bit of wire and clamp in a fretsaw ,then use a suitable size file and file a flat.isc
|
|
|
Post by Deleted on Dec 19, 2009 10:39:50 GMT
You can make your own half round wire,take a bit of wire and clamp in a fretsaw ,then use a suitable size file and file a flat.isc That's a novel idea if you can't get any, and I shall remember it: however, I got 50 for 99p...... JB
|
|
kwil
Part of the e-furniture
Posts: 383
|
Post by kwil on Dec 19, 2009 10:59:34 GMT
Why have you got chatter marks on your flanges? Seems out of character 
|
|
|
Post by Deleted on Dec 19, 2009 11:10:10 GMT
Why have you got chatter marks on your flanges? Seems out of character  That's because I didn't make the wheels. I bought the frame with the wheels from a famous member of this forum (who didn't make the wheels either): everything else is all my own work!I shall get rid of those before final assembly! JB PS: On the subject of split pin sources, by son-in-law just called in to look at the Brit. As he's a yacht rigger I suddenly have a source of miniature stainless steel pins!
|
|
|
Post by Deleted on Oct 29, 2010 15:16:39 GMT
I thought that I'd better finish the brakes before the frame comes back from the painters, so here is the full set, trial assembled ready for final fit and paint. I've adopted full size practice as far as possible instead of LBSC's large nuts, in that there are split pins holding the shoes and the bottom beams, and the hangers are held at the (new, thinner) hanger pins with button head screws All the pivot/hanger pins are stainless, and the shoes are alloy. Sorry about the pic: my camera hasn't come back yet! JB DJ, this isn't a cock up...... 
|
|
Smifffy
Statesman

Rock'n'Roll!
Posts: 943
|
Post by Smifffy on Oct 30, 2010 9:28:24 GMT
Works of art!
Keep the piccies coming please.
Smifffy
|
|