|
Post by Deleted on Feb 22, 2015 11:12:04 GMT
I've looked for data from full size engines as regards cylinder wall temperatures .
Not much to be found but Porta records a cylinder wall temperature of 210 C for an incoming steam temperature of 400 C .
Ewins gives a cylinder temperature of 145 C for an incoming steam temperature of 313 C .
210/400 = 0.53
145/313 = 0.46
Roughly cylinder wall temperature is about half of incoming steam temperature in both cases . This is about right taking everything into account .
In both cases this was for an engine working reasonably efficiently with expansive working .
Cylinder wall temperature for engines working with poor efficiency and non expansively is likely to be a bit higher .
|
|
|
Post by joanlluch on Feb 22, 2015 14:37:42 GMT
Hi Michael, that's intersting. I would have said that cylinder wall temperature would be higher. Even if we consider a temperature after expansion as low as 100 C these figures seem too low. I can think that some temperature loss is due to thermal disipation at the cylinders, so that may explain it.
|
|
|
Post by Deleted on Feb 22, 2015 15:12:45 GMT
(1) Steam cools a further amount as it is being exhausted from cylinder on return stroke of piston . This cooler steam is in contact with cylinder for a relatively long time in the cycle .
(2) There is a boundary layer effect on the cylinder walls which provides useful insulation .
Much more to discuss but I'll leave it at that for now .
|
|
|
Post by suctionhose on Feb 24, 2015 5:00:14 GMT
I keep looking in on this thread in the hope of an outcome. I have 30 years practical experience of vitons - superheated steam - 5" to 7 1/4" size.
To be honest, they have mixed virtues and in the spirit of striving to be better, I'm thinking about what to try next.
There's different types of service: 1. Static Seals. Ie boiler fittings, clack seats, etc. Viton to 170 deg C - no trouble year on year. Orings are 60 - 70 Duro.
2. Non lubricated Rod Seals. Eg Throttle rod into boiler. Leakage cold. Don't like scale on rod. Regular clean and lube of rod helps. Usually seal ok under steam.
3. Piston rod seals. Lubrication essential. Cylinder lubrication alone is insufficient. Sectioning a worn oring shows wear consistent with grabbing and rolling with rod. Wear occurs to the point of leakage under lightly loaded conditions. Still seal under heavy loads.
4. Valve rod seals. Short travels. Low surface speeds. Long life without trouble.
5. Piston seals. Would expect trouble. Cylinders walls are quite dry in terms of lubrication in practice. This observation has lead me to investigate steam cylinder lubrication and oil distribution recently. Not all oil entering steam chest passes through to cylinder... Also, I measured static friction of a pressurised piston oring as being very much higher than a metal to metal seal. Would not use.
Summary : Small viton orings on piston rods have negligible friction affect if copiously lubricated by filling a groove on the non pressure side of seal with oil. (oil cup)
Static seals for fittings are trouble free for the overhaul life of boiler and fittings (100's of hours in steam)
FYI, my "reference" loco is 5"g with cylinders 2 x 3 1/4 (50 x 84mm) WP is 100 psi (700kPa). On loaded passenger train (2000kgs) it operates at 50% cut off with 80 psi steam chest and radiant superheat.
|
|
|
Post by Roger on Feb 24, 2015 8:52:35 GMT
Hi Ross, That's really useful information, thanks for sharing it.
Do you have any sketches or drawings of how best to fit a Viton 'O' ring to a clack seat? I imagine you just make a pocket that's the right size. Is there a particular ratio of size that works best, ie the section and diameter compared to the ball diameter? I know some people don't like this idea, but it seems like a great way to avoid weeping.
I hear what you're saying about lubrication, I'm going to have to do something about that for SPEEDY's piston valve.
It sounds like the use of Viton for a piston rod seal is right on the limit of what the material can stand. Have you considered making a seal from PTFE, using either an 'O' ring or steam pressure to provide the closing force against the rod? I'm tempted to try this myself.
In your piston seal experiment, was that just a plain Viton 'O' ring in a groove? I'm tempted to try the same design of concentric PTFE pegged rings I've used on the piston valve bobbin for the main piston too. All flexible solutions, whether they are 'O' rings or split rings, are going to require more static force than metal rings though. I was surprised at the amount of force it took to move the piston valve seals in a static test.
|
|
|
Post by ejparrott on Feb 24, 2015 9:53:05 GMT
Very interesting Ross. Could you elaborate on this a little? It's particuarly relevant to me as I'm currently designing in this area Summary : Small viton orings on piston rods have negligible friction affect if copiously lubricated by filling a groove on the non pressure side of seal with oil. (oil cup) Are you suggesting that the O ring be clamped in place in a groove with allowance for a certain amount of roll - just reffering to the ME's Handbook .141" for a 3/32 section O ring - and then the traditional and visible gland be arranged with an oil cup to feed oil to the non-pressure side of the O ring? Or does the oil need to be fed into the O ring groove?
|
|
|
Post by Roger on Feb 24, 2015 10:04:06 GMT
Very interesting Ross. Could you elaborate on this a little? It's particuarly relevant to me as I'm currently designing in this area Summary : Small viton orings on piston rods have negligible friction affect if copiously lubricated by filling a groove on the non pressure side of seal with oil. (oil cup) Are you suggesting that the O ring be clamped in place in a groove with allowance for a certain amount of roll - just reffering to the ME's Handbook .141" for a 3/32 section O ring - and then the traditional and visible gland be arranged with an oil cup to feed oil to the non-pressure side of the O ring? Or does the oil need to be fed into the O ring groove? I was looking for information about 'O' rings rolling and one of the claims for X-rings (Quad rings) here link is that they're better at resisting roll, for obvious reasons. The trouble with X-rings seems to be that of availability, I had to have a batch of them made to get the size I wanted, I'm yet to find anywhere that holds any stock.
|
|
|
Post by Deleted on Feb 24, 2015 13:31:23 GMT
(1) Tables at the heading of this thread refer to liquid absorbtion tolerance which is not quite the same thing as wear resistance or simple heat tolerance . (2) Piston rods on some full size engines have metallic glands . Several different configurations but essentially a stack of cup and cone rings made from (usually) whitemetal . Sometimes solid rings and sometimes with slits . Either way finished close size for rod and compacted endwise . (3) This is an interesting read : www.jameswalker.biz/products/197-Chevron-reg-for-rods-glands-pistons(4) Friction caused by a seal is determined in part by the materials and working conditions and partly by seal mechanical design . I would not say that a metallic ring is always better/worse than an O ring or PTFE seal in this respect - each case has to be looked at individually .
|
|
|
Post by Roger on Feb 24, 2015 14:44:43 GMT
That's an interesting link Michael. It looks like the pressure of the fluid is used to expand the 'V' shape to make the seal, is that how they work? Presumably there's enough natural spring in the materials to make a seal to begin with. I don't see why something similar couldn't be made from solid PTFE with a little thought. Has anyone tried making their own PTFE rod seals, it doesn't sound that difficult to me?
|
|
|
Post by Deleted on Feb 24, 2015 16:18:31 GMT
(2) Piston rods on some full size engines have metallic glands . Several different configurations but essentially a stack of cup and cone rings made from (usually) whitemetal . Sometimes solid rings and sometimes with slits . Either way finished close size for rod and compacted endwise . The BR Standards I have come across and the Bulleid Pacifics have a chilled cast iron segmented piston gland arrangement. Basically a chilled cast iron flat bottomed cup inside of which is a segmented 3 part interlocking chilled cast iron piece held together by 2 springs stretched around the circumference, it is also flat bottomed and ground so that the top rim of the cup is exactly the same as the 3 part piece. there is then an exact same arrangement on top of that which is ground to the first and a third on top of that, no cones at all, all ground flat segmented chilled cast iron. I am currently trawling Google for a pic, I know there is one out there somewhere! Ben
|
|
|
Post by Deleted on Feb 24, 2015 16:27:34 GMT
Thanks Ben - there are certainly multiple variations on metallic packing but I hadn't come across the version you describe .
Be interesting to see a picture if you can find one .
I've only recently started trying to find out how the different types work .
MichaelW
|
|
|
Post by Roger on Feb 24, 2015 17:26:50 GMT
I'd be really interested to see what these different types look like. Am I right in thinking that the segments have their join lines covered by the other halves of the seal? I'm finding it hard to picture how they seal round the outside too.
|
|
|
Post by suctionhose on Feb 24, 2015 20:32:38 GMT
Standby Ed & Roger. A picture is worth one kilo-word...
|
|
|
Post by Deleted on Feb 24, 2015 22:33:45 GMT
Not the pic I was after and not a Std or Bulleid setup but it's the same design. I'll keep searching for the real one. Yes Roger, they overlap/interlock.  There is slightly more to them than this, I hope all becomes slightly clearer! Cheers Ben
|
|
|
Post by Roger on Feb 24, 2015 23:18:59 GMT
Hmmmmm..... slightly.... Each segment looks like it's in two pieces but it's hard to see how it closes down onto the piston rod. Does the flange stand clear of the pocket when it's tightened up?
|
|
|
Post by suctionhose on Feb 25, 2015 0:53:58 GMT
Metallic packing in steam terms amounts to a bunch of washers with small clearance on the rod interspaced with a bunch of washers clamped in the stuffing box. The over lapping faces accommodate misalignment. Compared to hydraulics, it is no seal at all. That said, a combined oring and floating element arrangement can be made in 5" although the complication is not really warranted given the misalignment in models falls within the working range of an oring.
|
|
|
Post by Deleted on Feb 25, 2015 7:39:58 GMT
Metallic packing in steam terms amounts to a bunch of washers with small clearance on the rod interspaced with a bunch of washers clamped in the stuffing box. The over lapping faces accommodate misalignment. Compared to hydraulics, it is no seal at all. That said, a combined oring and floating element arrangement can be made in 5" although the complication is not really warranted given the misalignment in models falls within the working range of an oring. Its slightly more in depth than that mate! For a start there is no clearance on the rod, they are intially machined to be near enough size for size fit with enough leeway for lubrication. "Washers" is not a great descriptiion either really, it conjours up images of a very agricultural disc of metal with a hole in it, this is a very long way from the truth indeed, as mentioned all the pieces get ground to a high finish in one way or another. The overlapping faces are more for sealing and the ablility for the segments to self adjust when wear occurs (helped by the circumferential spring(s) ) Roger I have found a better pic but still not the one I'm after, it just about shows one half of the interlocking segment of one of the 3 pieces (bottom right of pic) 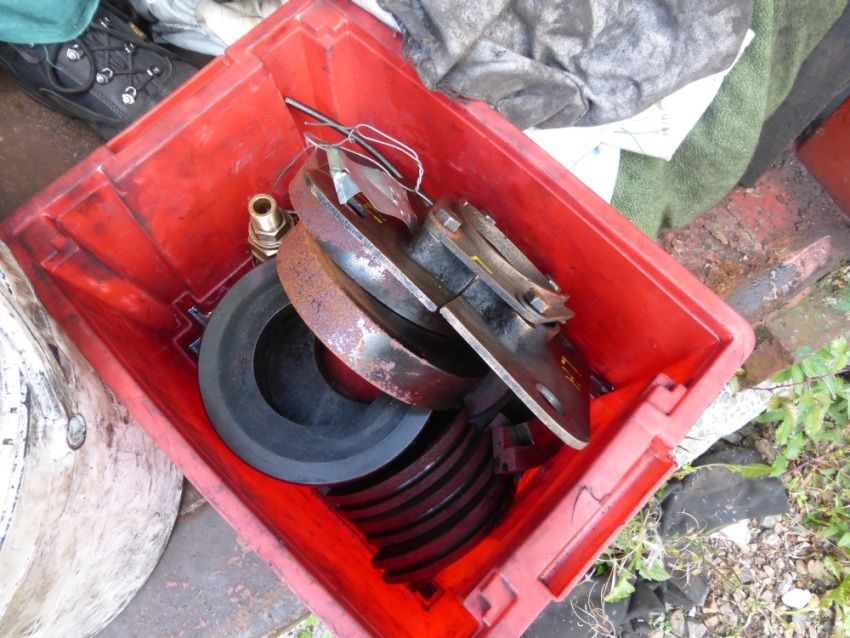 I'll carry on searching!! Cheers Ben
|
|
|
Post by suctionhose on Feb 25, 2015 8:23:59 GMT
I stand to learn something. But I'm not learning yet. Yes please,keep searching!!!
|
|
|
Post by suctionhose on Feb 25, 2015 8:55:09 GMT
Viton Orings as Clack Seats. The proportions shown are 5/16 ball on ¼ ID x 1/16 section oring. Alter larger or smaller to suit requirements. Under pressure, the 304 Stainless or Bronze ball, compresses the oring until ball contacts the metal lip. Thus the tendency of the ball to become stuck in the oring is controlled. You can machine the oring groove down the bottom of a hole with a long skinny boring bar or make the seat portion from hex and screw it up from under into the body. The latter is easier. I run with injectors only. Clacks of this type are indispensable to injector reliability because they seal perfectly without sticking. They are deployed inline, out of sight so the visible clackbox can be made to scale although it performs no function other than a connection for the feed water pipe on the boiler. (second picture) Progress being as it is people have moved on to viton or nitrile balls instead these days. (Ex Automatic Transmissions). Too undignified for me! (BTW this is not suitable for pumps as the intermittent flow may dislodge the oring)  
|
|
|
Post by suctionhose on Feb 25, 2015 9:03:46 GMT
Piston Rod Orings These are fitted according to hydraulic cylinder principles with the housing and rod dimensions being nominal inch sizes. BS orings are oversize in section somas to provide the required nip inside and out the establish the seal. Metric different The groove is always wider than the nominal ring section and is formed in this case by pulling the gland up to a shoulder. It looks like a normal gland but it cannot be taken up. It doesn’t need to be. The pressure deforms the oring to one side of the groove. Hydraulic people would use a hard plastic back up ring to provide a concave seat for the oring so it retains its shape better under the very high pressures. What is not commonly appreciated is that in terms of metal to metal contact, pistons, piston rods & crossheads are the bearings with the highest surface speeds on the engine. I would say the limitation of Viton in pistons & rods is likely the surface speed and the surface finish encountered by the ring while deformed under pressure. On one engine I have used hardchrome rod for piston rods instead of stainless. Still lubricated. I often think a bush of PTFE would do the job without oil. You could hardchrome the bores of a bronze cylinder too!!! I haven’t used PTFE for rings although many people do. The inherent characteristic of PTFE that is both its downfall and its success, is being soft with a high coefficient of expansion. Great for piston valve rings where they can squelch in and out of ports. The wall tension comes from expansion with heat. I think the gentleman from Switzerland (Pondok?) talked about his experience before.  
|
|