|
Post by Deleted on Oct 13, 2020 9:41:00 GMT
She's looking great David... I particularly like the cab detail which is nice and crisp...
Pete
|
|
|
Post by David on Oct 13, 2020 20:49:36 GMT
Thanks guys. I'm going to leave the pipes for now. I can always make another later but they look so bad around where they curve up the boiler and connect to the dummy clacks there's not much point quibbling about a bit of a downward slope. I kicked the inlet legs of the dummy clacks out a bit so they could screw down slightly further from my first attempt. That may have been a mistake as the angle the pipe needs to connect to them is very awkward. Fabricated clacks that use copper pipe for the legs would give some flexibility here but the castings don't.
I forgot to mention I had to extend the reversing screw itself by 5 or 6mm. I cut it where the shaft goes through the long bush in the stand then drilled each end 3mm, holding them in the lathe with collets. A 3mm pin was loctited in and it's all hidden in the bush. Even so it just barely clears the dummy backhead.
I think I could paraphrase that famous saying, loco plans only survive until they meet a real boiler! This one is a bit of a horror show - the tubes and flues are banana shaped, the crown is way too high, the firebox too wide by about 6 or 7mm, it's wonky side to side, most of the threads are really loose, it goes too far back in the cab... but unless you're very skilled I can't imagine all that copper bashing and repeated heating will result in anything that looks much like the thing described on paper.
|
|
|
Post by David on Oct 19, 2020 7:30:17 GMT
A burst of effort over the weekend saw the chimney finally bolted on and some spacing washer made to sit under the clacks. Quite some time ago I attempted to mark the bolt positions on the skirt of the chimney with dividers and couldn't figure it out. I decided to print an octagon with lines joining the points and use that to approximate the locations. I nearly stuffed it up by orienting lines fore/aft and left/right but caught it just in time. I think it's a good enough approximation. Drilling the holes was a bit of a drama, I don't have any 10BA sized tapping drills that are sharp. The mostly recently bought box of number drills are all blunt (really blunt) from the factory. I broke one carbide drill off in the hole - using a pistol drill it was expected - but luckily it had just got through so I could punch the stub through with a piece of wire. Anyway, that's a job I've been putting off for years so glad it's done.   I also made some washers to sit between the tops of the clack bushes and the clack valve flange. Other people make it so the flange can screw down onto the boiler bush but I've had the prototypical gusset cast into these so that idea doesn't work. The one on the left needs to be sanded down by 1 turn, about 0.8mm for 32TPI. I'm trying to get them so the clacks are screwed in tight. These washers just look like the boiler bush extends through the cladding on the boiler. 
|
|
|
Post by David on Nov 1, 2020 10:51:32 GMT
Following on from the above post the washer on the left was reduced in height enough to allow another turn of the casting and it scraped the barrel! So I had to make another one and live with the slight visual difference between the two sides. With luck black on black will make it go away. I've been putting the cab roof off forever, because it looks difficult. When I drew the spectacle plate I was being too clever and stuck rigidly to the drawing I was tracing the CAD over, figuring the compound curves were prototypical or something and not thinking ahead to the fact the roof would be rolled so have a constant radius. Luckily there are little plates that go on the front and back of the roof and the front one will hide the gaps which would otherwise be intolerable. Here I am squaring up the roof material. It's quite long to give about 3" either side of the real edge to try and avoid flats after rolling. Given my amazing ability to chew into machine tables, vices, clamps, and anything else that isn't actually the metal I'm trying to remove, this setup was pretty sketchy. I could not find a reasonably flat piece of anything the right size to put under the stock so just clamped it right on the table and had the cutter in the T slot. I got away with it.  Something else I've been putting off, but for the opposite reason, is the dummy air pump. This is all machining, and doesn't have to work! Like the reversing screw it looks like a part that if I get it right it will look excellent, and I thought it would be a nice way to finish the project after all the horrible sheet metal work and detailing was done.  It's a complicated beast and even though thorough drawings have been provided I need to model it in CAD so I can see what it looks like and think about how I might make each bit. This model is fairly complete. There are some sharp corners that will be taken care of by the endmill radius etc so I'm just drawing it well enough to get a feel for the parts. The only thing I'm a bit unsure about is the fins and boss down each side of the bottom cylinder. I think the front of the flange is on the centreline. It might be enough to just make the flanges and use a couple of 1/16 rivet shanks through it into the cylinder to hold it's alignment while it's soldered on. Then the flange and cylinder drilled for the boss to go in, trying not to wreck the flange. But the first problem I'm likely to hit is how to get the dummy flange bolts on each end of the top cylinder in line. It doesn't matter of course, but I'd like them to be. I think the answer is a bar going through the hole at the back that will give me a datum to work from that will be the same whichever way is up.
|
|
mbrown
Elder Statesman
 
Posts: 1,790
|
Post by mbrown on Nov 1, 2020 11:56:04 GMT
If you are not relishing the challenge of making the air pump (and if you are feeling fairly rich....) Knupfer do a very nice lost wax dummy air pump casting - assuming it is the kind fitted to your mogul. linkI have to say that my own preference would be to make it myself, but it can help to know there are shortcuts out there. Best wishes Malcolm
|
|
|
Post by David on Nov 1, 2020 21:54:12 GMT
Thanks Malcolm,
I'm keen to have a go at making it. I like machining well enough if it's not too difficult - it's everything else I hate! Not a single critical dimension here and it doesn't have to work, so it's a good project for me :) It will be mostly manually machined and only those flanges look a bit tricky to place. The whole thing can be held together with soft solder and screws.
I may do the very top of the bottom cylinder on the CNC, but it could easily be done with a rotary table. It has a couple of bits that stick out each side, inline with the flanges below it.
We can buy a resin casting of one here, but I knew from the start I was going to try and make this myself.
|
|
|
Post by Jim on Nov 2, 2020 4:38:00 GMT
It's good to have a go at making your own David. That way you build up your own skill base and strange to say often end up with an item that is better than the commercial version simply because you take time to a) get it to look right and b) because you often add little details that the prototype had on the loco you're following but which aren't on the commercial version because it must appeal to a wider audience.
Your loco is looking great and you should be very proud of what you've achieved I certainly would be.
Jim.
|
|
|
Post by David on Nov 2, 2020 21:30:14 GMT
Thanks Jim. I've edited this to say I had no good photos of a real one on a B class, but then remembered I took photos of one on a different loco when I was at the Powerhouse Museum a few years ago "just in case" and it seems to be the same type so I do have some good photos after all. What the drawings show are very close to my photos with the only obvious difference being the area around the flanges at the bottom of the bottom cylinder. I can imagine this difference is there because to make it completely prototypical would add a huge amount of work to making the model. You couldn't just turn most of the cylinder, it would have to be made in 4 parts, 3 of them like the top bit requiring a rotary table and a lot of care to get them right.   It was interesting to look at the one linked above. It has fins on the lower cylinder, an oil pot is on the other side, and the flanges are less pronounced, being mostly hidden by the fins. It's clearly a single cylinder version of an air pump and has many of the same doodads on it, but also clearly not quite the same so there must have been many variations on this theme. By the time it's finished there will be enough pipes around it that it becomes a busy lump on the side of the smokebox and I think as long as the major features are good then most people will think 'there's the air pump, it looks good',
|
|
|
Post by Oily Rag on Nov 3, 2020 20:40:23 GMT
I find it surprising for that WHB pump not to have cooling fins on the lower air cylinder.
|
|
|
Post by mugbuilder on Nov 5, 2020 0:50:31 GMT
|
|
|
Post by mugbuilder on Nov 5, 2020 2:19:00 GMT
That engine is one of the many different engines stored for over 30 years at Dorigo NSW. It, like the others, is in surprisingly good order considering that it is a 100-inch rainfall area. The built-up crud is a result of regular dosing of sump oil and dust. It is one of the ex Bunnerong powerhouse engines and that is why it has had the original sandboxes removed and that little box one added. The pump is the smallest one fitted to NSW engines and is even smaller than the one fitted to the 12 class 4-4-0's which is the plastic one that is available, and which was taken as a rubber mould from the pump that I made for David May's 12 class.
|
|
|
Post by David on Nov 6, 2020 4:06:16 GMT
Thanks Barry, one of those photos shows some detail I didn't get on mine from the Powerhouse. There's some other good non-pump detail there I'm glad to be able to see too.
Are the dimensions including or excluding crud? :)
I've been making parts for it over the last couple of days but nothing much to show yet. I may be wasting my time trying to model the lower cylinder top/bottom bits in a bit more detail - what's coming off the CNC machine isn't really showing much promise.
This might be a candidate for casting in 3 sections - top cylinder, bottom cylinder, air filter - leaving the C shaped spacer to be made separately. I can make a much better 3D model than what I'm going to end up with in the metal!
Autodesk have finally let the other shoe drop on the hobby license for F360. It will no longer generate gcode with tool changes or rapid moves. That means generating a different gcode file for each tool and manually editing it to try and restore the rapid moves. They've also removed support for the 4th axis, so goodbye to that, and I'm guessing editing the gcode for Rapidturn lathe work to restore the rapid moves won't be as simple as it is for trivial milling files. It's no surprise, but it is annoying. They don't have anything cheaper than $600 or $700 AU *per year*. That's not happening. I'd pay $500 once-off for unbroken hobby use, but I'm not subscribing at that price.
|
|
|
Post by David on Nov 6, 2020 10:17:12 GMT
The bits so far. The cylinder was turned and milled manually. The two plates were done on the CNC mill. Neither was very successful and the thicker one was done twice after I tried double sided tape again, and it failed again. At least I didn't mill into the clamps or the table this time! I'm making the thicker plates out of 28x3mm brass strip and there's a fair amount of waste by the time you get the clamps out of the way, and you have to get 0.5mm off the back of them when they're finished. I did that on the lathe using a live centre to press the part against a piece of rod. It was sketchy and the superglue gave out but I got away with it. It still left a cusp I had to remove with a little sanding drum. I was going to do them 'part on a stick' but the metal shop didn't have any 38mm dia brass rod and it starts getting really expensive as it goes up in dia. As it is I bought only 500mm of the strip. The holes for the posts were 0.4mm under size off the mill, not sure why. I had to open them out with a drill then a tapered reamer. Given the amount of manual finishing these parts need it's lucky I'm not making spaceship parts.  
|
|
|
Post by Jim on Nov 6, 2020 17:18:00 GMT
Looking very good indeed David.
Jim
|
|
|
Post by coniston on Nov 6, 2020 20:00:26 GMT
I'm sure it will be worth the effort in the end, surprising how these things come together and with a bit of paint really look the part. well done.
Chris D
|
|
jasonb
Elder Statesman
 
Posts: 1,239
|
Post by jasonb on Nov 6, 2020 20:05:21 GMT
david could you not take the 0.5mm off the tops as the first op? As for holding if you are not going to be silver soldering than you could just soft solder onto a scrap block of brass and melt them off afterwards. A couple of tabs would be the other way to keep them in place and just file off at the end. I've not used double sided myself but did do some engraving the other day using the two layers of masking tape and superglue method which worked well.
As I said on ME once you get your educational licence sorted you will get your rapids etc or just run at a good feed rate then the lack of rapids is not such an issue. Not having any means of quick change let along an auto changer I have always broken the code down into what can be done with each tool does not take long to close and load a new code.
|
|
|
Post by David on Nov 6, 2020 22:55:04 GMT
I took the 0.5mm off the top of the stock as a first op on the first attempt, but then I'm cutting all the way through the part and it starts to flex and come up as the cut reaches full depth. Tabs leave too much cleanup and I hate the sound the cutter makes when it goes down the other side of them! I have no more luck with masking tape and superglue than I do with double sided tape. I don't have any good answers for thin stock, after 3 years of experiments.
Soft soldering sounds like a good idea for small parts like these. I'll try that. Perhaps if a non-functional part like these was left slightly over thickness the soft solder could be sanded off sufficiently for some silver solder to take effect.
I'm not holding my breath on the F360 educational license. I'm considering trying the EAA membership route to get SolidWorks.
The tool changes aren't annoying me as much as I expected, for this job at least. An unexpected side-effect is that before each step I can put the tool in the spindle and use the technique you and Wilf use of rolling a pin under the cutter and setting the Z height. That means I'm confident of the tool height before pressing go. The height gauge Tormach supply is pretty cheap and I reckon there might be 0.1mm variability in my tool offsets relative to each other due to that on any given job.
The loss of rapids is a real pain though. I think Autodesk could have achieved their aim of stopping people using the hobby license for production work by disabling multi-tool programs only. I guess they'd say it's too easy to stitch them together and finding rapids buried in g-code is more of a nuisance.
|
|
|
Post by David on Nov 7, 2020 6:30:13 GMT
I took the top 0.5mm off first on the next part, it went ok. The cutter isn't doing a great job but it's a cheap HSS 4 flute in gummy brass.  Like the bottom part of the cylinder, it locates on the rods that will become the ribs at the sides.  Here's the spacer, 19mm dia, 1.25mm wall thickness. The slot ends 2.5mm from one end and 1.6mm from the other. I was uneasy about this setup from the start but didn't figure out why until the end. The thin 1.6mm bit is completely unsupported so I was expecting it to push out or snap or something. In the end I was taking 0.1mm passes. I got away with it, but you wonder how I didn't see the problem before starting. By the time I got there I didn't want to lose my depth after moving the part.  By this point the cheap cutter was completely done. It was rubbing more than cutting for the last couple of passes, but again, I got away with it this time. I usually don't! This was a bugger to clean up because the cutter had done such a bad job.  [/url] I can't get this brass out of the flutes.  All the bits so far.  
|
|
|
Post by Jim on Nov 7, 2020 6:58:31 GMT
That's looking really good David. Well done!
Jim
|
|
jasonb
Elder Statesman
 
Posts: 1,239
|
Post by jasonb on Nov 7, 2020 7:53:13 GMT
My thoughts are that cleaning up a couple of tabs is a lot less work than having a part move and need to be remade or having to mount in the lathe to do additional machining. That cutter looks to have been past it's sell by date in the first picture let alone later on. For the spacer holding if below the vice jaws will stop the end flexing outwards but is risky so just put a piece of sacrificial material (aluminium) between part and jaw so you cut into that if something goes wrong with your code. This was 22g (0.7mm) soft bending brass, done in three passes of 0.3mm deep to just break through, 3mm HSS 3-flute cutter (ctr cutting), 5000rpm 300mm/min feed, lack of any significant burrs is a good sign the cutter is sharp and feed/chip load not causing rubbing. Work was screwed to a piece of MDF with washers and screws, did the hol efirst and added an additional screw then cut the profile. youtu.be/GwlnREMKA0s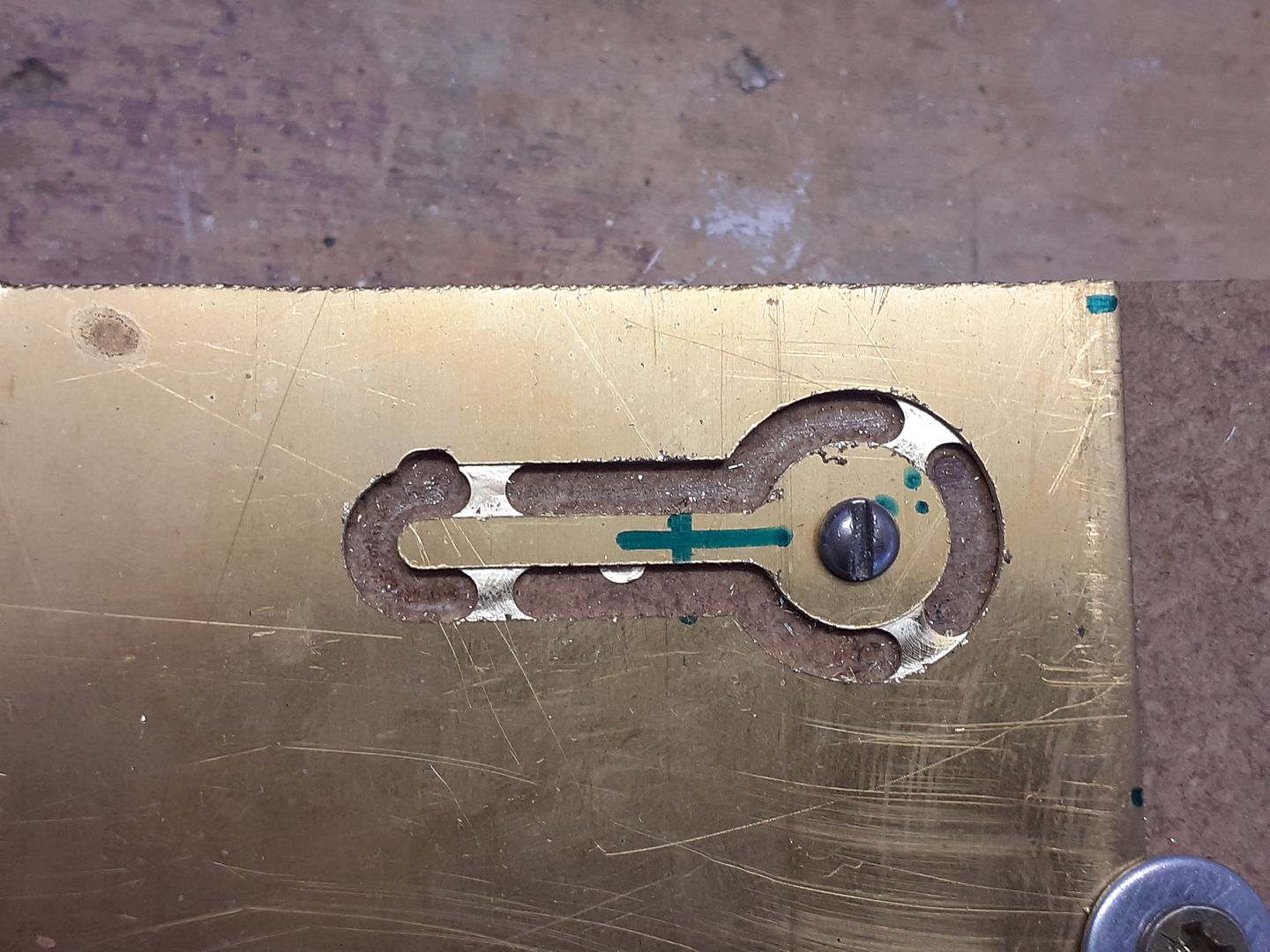
|
|