|
Post by Deleted on Jan 1, 2009 16:35:42 GMT
Alan, can I stamp my foot just this once and shout:
YOU DON'T NEED CARBIDE TOOLING UNLESS THE NEED IS EXCEPTIONAL![/color]
Thanks, I needed that! JB
|
|
|
Post by maninshed on Jan 1, 2009 17:28:56 GMT
I have never had much joy with carbide tools, apart from working on cast iron. For running cabide tools generally you need speed, gee gee's (horse power) and a ridgid machine. Most general ME lathes up to 5" just arn't ridid enough, so i agree with 'Simplyloco'. Going back to Dr john's photo on page one that's the sort of finnish I get, not so good on one cut but then not to bad on the next, usually being the finnishing cut that is poor. I usually grind my lathe tools on a cutter grinder so the angles and finnish is usually good, I then give them a light stoning.
|
|
|
Post by havoc on Jan 1, 2009 18:36:42 GMT
JB, shouldn't people use what they feel good and confident with? You can shout all you want I don't go back to HSS tooling unless I want a formed tool. I couldn't sharpen a bit if my life depended on it. So instead of using blunt HSS I use a TC and trow away when needed. And I don't see the speed issue. Using any tool below its designed speed results in less than optimal finish. This is how an HSS tool looks like when I have used it: 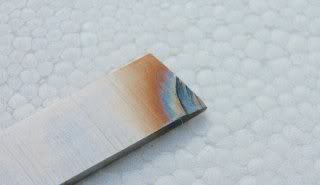 Need I to say more?
|
|
|
Post by jonkett on Jan 2, 2009 0:05:47 GMT
Jonkett, I assume that Dm is in mm in your formula, otherwise I arrive at rather funny speeds (1270000 rpm for a 50mm diameter). With the diameter in mm I arrive at 1200 rpm which is more sensible. I turned my last batch of 25mm wheels at 1000 rpm. The chips that come off then are a nice deep purple and very hot. More rpm I didn't dared to use. Yes, quite correct the formula is in metric and the figures used are basicaly for low carbon steels. The surface speed for Cast Iron is in the order of 100 - 180 m/min
|
|
|
Post by jonkett on Jan 2, 2009 0:19:58 GMT
If you are not achieving the results you think that you should with carbide tooling the chances are that apart from speeds and feeds your selection of carbide grades and chipbreaker is probably where you problem lies.
I go to shows and look at the stands especially the ones selling carbide and what i see are packets of inserts that can't be sold to an industrial user, or have been bought in surplus auctions. A good proportion of which is no use to a model engineer, or when asked if a 50MM face mill comes with a set of TPKN or TPUN inserts get a completely blank expression.
Use a good grade of carbide in the correct application you won't go far wrong, in fact in one of the latest magazines there is an illustration of a brazed carbide tool for steel being used on cast iron.
Ok, it will still work but not as effectively as the cast iron grades, steel grades are basically P30 or tough grades, when a K10/K20 hard grade is what is required. Brazed carbide was really a product for machines that were slow speed and perhaps not as rigid a setup as the modern kit.
|
|
|
Post by drjohn on Jan 2, 2009 12:42:23 GMT
Alan, can I stamp my foot just this once and shout: YOU DON'T NEED CARBIDE TOOLING UNLESS THE NEED IS EXCEPTIONAL![/color] Thanks, I needed that! JB[/quote] JB, Beware the fallacy of dogmatic finality! Without being acerbic, I and my needs are exceptional as you put it. What works for you and western industry, doesn't necessarily hold for the constraints of working in the deprived tropics. I will use carbide of whatever grade as and when I want. DJ
|
|
|
Post by petercolman on Jan 5, 2009 20:52:32 GMT
We seem to be running te risk of confusing modern industrial practise with home workshop machining. I think that the vast majority of us are working with machines that will not perform to the optimum with modern carbide tools, we juwst dont have the speed or power they need. So to get back to the problem that we all face, namely how to get good finish at home, I still think the well stoned HSS tool will give the best finish, however that is not working so what else? 1 make sure the tool angles are correct 2 remove the backlash from the top and cross slides, this is always a difficult one but a temporary measure is to put the cut on and tighten the jib strip for an experimental cut 3 get the coolant going this must be there to stop the swarf welding to the top of the tool and ragging the finish 5 use fre machining metal ( this is obvious but you will be surprised what a diffenence irt makes (one check is to machine a bit of brass0 Peter
|
|