|
Post by bobfly on Dec 30, 2006 11:07:36 GMT
A really good book if you can get it is lost-wax casting a MAP publication aboout late 70s mine cost £1 new by G.Leybourn-Needham
|
|
SteveW
Elder Statesman
 
Posts: 1,469
|
Post by SteveW on Dec 30, 2006 14:44:31 GMT
Mesuno,
You ask why go for 'Lost Wax' when simple sand casting is so simple. Well...
If you a student of making sand castles you'll know all about needing a bucket with a good taper on it else the newly molded 'castle' won't come out to play. The same goes for getting your pattern out of the newly rammed up block of sand, if there's no taper (draw) it'll stay there. If you think about it you are now making a mold of the bucket shape. Without enough taper you'll break the sand and the hole in the sand won't be what you wanted.
You also need to make your pattern (bucket) bigger than the required size of metal because on solidifying the metal will shrink big time.
'Lost Wax' allows one to make a hole ready to pour metal into that would be impossible to make any other way. Think about squeezing your hand through a small hole and then making a fist and then while still holding a fist getting your hand out, basically a monkey trap.
There are also the issue of finish. Building up layers of very fine grade material over a shape that basically disappears during the process can get you a very good finish and with no joins.
If you want a rough shape that's going to be machined all over then sand casting is a cheap and simple way forward. You get what you pay for in terms of money and effort.
In terms of recycling old aluminum remember that it may look all the same but it isn't. Try to stick to recycling metal that has already been cast. Extruded aluminums and especially modern car pistons can cause you a lot of problems. Also the stuff will absorb gases during the melt that'll result in a porous result. Additives to de-gas the liquid metal can be a bit nasty.
|
|
|
Post by richcarlstedt on Jan 2, 2007 4:26:23 GMT
Abby beautiful work my friend ! I have been doing lost Wax on and off for a few years. Some work sucessful, and some not. I took a two year course in Jewelry making at night school to learn the basics I have found that lost wax is not a time saver. In fact, it can be a great time consumer, unless,multiple copies of a part are needed. If I need only one or two pieces, I stay with fabrication.
Next I would like to point out a misconception. One that I believed in, until recently ,after going through 18 unsucessful attemps at making a steam distribution manifold and throttle valve for my trunk engine. This was a large cored part and using Kerr Satin cast I made a two part block 4 inches thick by 6 inches wide and 10 inches tall. This being too big for centrifical casting, I decided to put in two sprues at the top and pour into one side and use the hydraulic force of the metal to fill the mold, as the part was only 3 inches from the bottom. I had to do a gravity pour. Our local Adult Evening school had a shop with sand casting facities, and a heat treating oven Of large size
The misconception is that you need 700 degrees (c) for "wax burnout".after the wax is melted at 150 C I was instructed in this at school and every book has the same words ! After making the molds , I set them up on a hot plate for 36 hours at 166 C and the molds since they were split were absolutely clean and they were very dry....(or so I thought) Sealed them in a pail and immediately took them to school and put them in the heat treating furnace for final burnout before pouring. You can imagine my surprise, when the instructor called me and asked about the water coming from the furnace. At 350 (C) the door had water seeping out. we opened the door and saw a spiral cloud of steam coming from the sprues. After a few minites, it stopped. An hour later, at 600 C. we opened the door and I almost fell over. Two hours in the furnace (after 36 hours@ 166!)and you could see vortex's or steam coming out of the sprues. What I saw was not water from the mixing of wet investment, but the result of a high temperature chemical conversion of the investment itself into another form of solid. That explained the 'gas" holes I had in some of my past failures. The investment needs the temperature to convert and it then gives off H2O in the conversation, not the wax burning out. I had pondered this earlier because my employer used waxes for lubrication, and I know when heated to 90 C, all traces disapeared on our product..proven by sulphuric acid wipes..
Sorry for the long story but I wanted to show a real experience as my example and finding. Thanks Rich
|
|
Myford Matt
Statesman

There are two ways to run a railway, the Great Western way, and the wrong way.
Posts: 621
|
Post by Myford Matt on Jan 3, 2007 10:06:18 GMT
Hi bobfly - could you confirm the exact and complete title as 'Lost wax casting' (ie no hyphen?). Any chance of the ISBN? Should be on the first printed page.
Cheers
MM
|
|
|
Post by bobfly on Jan 3, 2007 11:03:16 GMT
Hi Myfordmatt. There is no ISBN number on this book it was a MAP craft publication Lost~wax casting,the guy who wrote the book on the introduction page was G.Leybourn-Needham,Altrincham,Cheshire January 1977 it was GEMCRAFT booklet published by Model and Allied Publications 13-35 Bridge Street ,Hemel hempstead ,sorry that is all the information i have. Regards
|
|
Myford Matt
Statesman

There are two ways to run a railway, the Great Western way, and the wrong way.
Posts: 621
|
Post by Myford Matt on Jan 3, 2007 13:19:18 GMT
Many thanks bobfly - I'll keep an eye open for it.
Cheers
MM
|
|
abby
Statesman

Posts: 928
|
Post by abby on Jan 3, 2007 17:21:56 GMT
Hi Rich - interesting observations and worthy of debate . As to whether or not one offs are viable, from a "time consumed" perspective will depend upon the personal circumstance of the individual and the type of product required. Obviously if the part required could be simply fabricated from the final material then that would be the way to go , however the beauty in lost wax casting is the stunning detail that can be reproduced, and the fact that the pattern materials can be worked so much easier than the final metal. The techniques probably border on arts rather than engineering and reflect the ingenuity of the modeler. The use of a fine tip soldering iron to join pre-formed wax shapes can perfectly reproduce full scale steel welding patterns for example . A warmed punch gently pressed into the surface of the wax can produce all manner of detail that would be difficult to add onto a fabrication. I normally produce a mould in silicone rubber from my patterns which means that almost anything can be used for the pattern making , if I want a cloth texture I use cloth , a baulk of timber ,then I use a nicely grained piece of wood. Many of my projects need scale lettering or logos which I produce by photo etching onto sheet brass. I often have as much enjoyment making the pattern and subsequent rubber mould as from the finished item , particularly as the pattern making can often be done in the comfort of the kitchen. On the subject of mould firing , my own moulds are 6 inches dia and 12 inches deep, and are contained within a stainless steel ( nimonic is best) flask. This requires 14 pounds of dry investment mixed with 5.3 pounds of water , every drop of this water and every trace of combustible matter must be removed before molten metal can be poured in. Wax can and will remain trapped in moulds after "dewaxing" and the firing cycle ensures that it is removed. Firing on the size of mould that I use lasts 5 hours at 720 deg C , firing at temperatures greater than this will indeed cause chemical breakdown of the plaster and is undesirable. The temperature cycle for drying , dewaxing , burnout and cooling lasts 24 hours and is essential if faulty moulds are to be avoided , a programmable controller is a must ! As all plaster based investment cements are similar in make-up ie. a refractory held together by plaster I can see no reason for a chemical reaction during "burnout" .The refractory is totally stable at much higher temperatures and plaster will not have a reaction at the firing temperature. My own moulds have finished "steaming" by 450 deg C but still show stains around holes showing that wax residue is present even at this temperature . At the end of the cycle they are usually bone white or occasionally very slightly pink.Sometimes after pouring the metal, which is usually silicon brass , you can notice a whiff of sulphur dioxide from plaster breakdown caused by the high temperature of the metal which is at 1150 deg C. I would suggest that the plumes of steam that you saw were simply the water being driven from the mould - incidentally the oven used for de-waxing/firing should have good air circulation , to allow steam to escape and to provide oxygen for the burn. Moulds may appear to be bone dry but will retain moisture even at temperatures well above boiling point ! As you said centrifugal casting is unsuitable for large items and I use vacuum assisted casting for all my work. the flask , which is perforated , is placed into a chamber with a rubber seal around its top, the chamber is evacuated to 27 or 28 ins HG .As the investment is micro porous any air trapped behind the metal is sucked through the mould and the metal is drawn into the finest detail and deepest dead ends. This method makes complex venting and sprue-ing un-necessary. I have witnessed whole and perfect castings formed from patterns which have broken from their sprues and floated free in the investment until coming to rest against another pattern. they have been fed totally through the contact area ! Just to finish , although I have wax injection facilities I mostly pour my molten wax into the rubber moulds and often use a wax temperature of 150 deg C , in fact I have found that an old deep fat fryer makes an ideal wax pot . The pattern waxes are not of a natural or petroleum nature but more like plastic , they are very fluid when melted and quite hard when set , but they do not evaporate , even at high temperature. Lastly air voids in your castings are most likely caused by incorrect sprue-ing and / or venting ,as moisture would most usually cause metal to be ejected with some force back through the sprue hole.Another possibility is porosity due to shrinkage and inadequate feeding. When a casting solidifies it is a gradual process with the coldest parts going first , this means that the shrinkage is not a uniform process , but is concentrated in the last part to solidify , to counter this, feeders are placed on the thicker sections and also "chills" ie. pieces of metal that will promote more rapid cooling . This is no so easily accomplished in investment casting as it is with sand moulding , but some control can be exercised by pouring metal at different mould temperatures . I normally cast at a mould temperature of 200 deg C for sections of around 3 - 10 mm , I will drop the temperature 50 deg or so for thicker sections and raise it for thinner , but its trial and error . The poking of the sprue with a piece of wire rod or the gentle tapping of the flask helps to keep the feeders fluid for longer which can help to lower shrinkage problems. Hope this is useful - Abby.
|
|
Myford Matt
Statesman

There are two ways to run a railway, the Great Western way, and the wrong way.
Posts: 621
|
Post by Myford Matt on Jan 3, 2007 18:15:39 GMT
Abby - you really need to put your knowledge down on 'paper'!
Just reading your recent commets has got me hooked - where do I start?
Matt
|
|
abby
Statesman

Posts: 928
|
Post by abby on Jan 3, 2007 21:25:36 GMT
The subject of casting seems to be of great interest, and this doesn't suprise me as I have been hooked since I was eight years old and attempted to make my own lead soldiers. Using plaster of paris moulds and the living room open fire as my foundry, I managed to destroy my mothers hearth rug with molten lead, which sticks like the proverbial to a blanket. Over the intervening fifty years I have persued the interest with almost religious zeal and have cast in metals , plastics and concrete , have constructed metal melting furnaces fired by coke , parafin , diesel and gas. As the subject of foundry practice is already well covered I will stay purely with lost wax , unless specific information is requested and I will presume that interested parties have a basic knowledge of metalurgy , the melting of metals and health and safety. Although dating back to the bronze age , lost wax casting was really rediscovered during the second world war and the technological strides have been enormous since, putting the techniques easily within the grasp of model engineers. I will say at this point that my own foundry , although based at home is a commercial enterprise and a hobby that became a living. That said every piece of equipment has been designed and made by myself and improved by much usage. WARNING as a hobby foundry work can take over being the means to an end , and become the end if you are not careful. Well to start you will need some specialised bits of equipment which can be readily purchased for a few thousand quid , or you can make your own. Perhaps the most essential thing you will need is a burn-out oven , this must be capable of heating your moulds to the required 720 deg C , and it will need controling. An oven can be constructed using the heating elements from electric cookers , loads of these in scrap yards and not expensive to buy new. A healthy five kilowatts will make a great oven capable of reaching and holding the temperature with ease , just make sure that the elements are for the voltage of your supply LOL! My first oven used elements from a heater , the type that heat up loads of bricks and then release the heat , can't think of the damn name. REMEMBER. with sheathed heaters the first four inches at either end should be outside the heated area. It is also possible to buy varying lengths of sheathed heater - stainless steel sheath is good enough - which the supplier will bend/form into any shape you require. It is better to make up the five kilowatts in smaller amounts than one big one , then if one element burns out you are still in business. I recommend eight elements , thats four each side wired in parallel. more to follow Abby.
|
|
SteveW
Elder Statesman
 
Posts: 1,469
|
Post by SteveW on Jan 3, 2007 22:18:25 GMT
Abby,
You need to bottle this stuff and send it in to either ME or EiM. Taking the Camden book catalog as a guide there ain't much out there written down.
Simply re-structuring what's here would be a good start.
|
|
|
Post by spurley on Jan 4, 2007 0:12:55 GMT
Hi Abby Take a leaf from Chris Vine's (excuse the pun!) book and write this down please! The knowledge and experience you show is too valuable to lose or to keep to yourself, if you understand my viewpoint. Chris has recently published a very fine book on painitng model locomotives, which seems to be doing very well. Maybe Chris could tell us how many copies have been sold? He would, I imagine, be able/prepared to assist you with advice on the process of writing and publishing on a subject which doesn't seem to have too much written down about. Go for it  Cheers Brian
|
|
abby
Statesman

Posts: 928
|
Post by abby on Jan 4, 2007 0:45:04 GMT
OK guys i will start to put some thing together , but we haven't touched centrifugal white metal casting or photo etching yet LOL ! thanks for the encouragement Abby.
|
|
Myford Matt
Statesman

There are two ways to run a railway, the Great Western way, and the wrong way.
Posts: 621
|
Post by Myford Matt on Jan 4, 2007 10:17:44 GMT
One step at a time ;-)
MM
|
|
abby
Statesman

Posts: 928
|
Post by abby on Jan 5, 2007 16:07:33 GMT
OK. Just remembered - storage heater - having constructed , or acquired by what ever means , an oven with suitable internal size for your needs ,you will need a controller . DIVERSION I have said this before but visit your local scrap yard - not breakers yard - on a regular basis , make friends with someone who works there , preferably the boss but the foreman is good . Spend a few quid now and again and before too long you will find almost everything you could need at a fraction of the real value , remember to take some gloves though and wear safety boots , keep well away from working machinery . I had the misfortune of buying a Centec 2A milling machine in good working order for £10 . It took me two hours to strip it down to bits that I could put into the boot of my Cortina. Why misfortune ? because the other 20 had just been smashed into foundry sized lumps ! The heating cycle is fairly complex and requires the ramping and holding of different temperatures , When I made my first oven ,a suitable controller was several hundred pounds and a penny , as I was several hundred pounds short of the price I made my own. Thanks to Sir Clive I had a 48K spectrum , and with a simple I/O interface , solid state relays and some basic programming a working controller was born , and died after two runs , a friend came to the rescue with an Apple II and this was in almost daily use for over 10 years . During a recent overhaul of all my equipment I invested in a programmable controller by VERTEX . its made in China , but aint everything now. Very reasonably priced at £120 including solid state relay and heatsink , and easy to program if you can read chinese ! No , the manual has been translated and eventually makes sense. A K-type thermocouple completes the oven requirements , except for a pan of some description that will fit in the bottom and catch the wax during the de-waxing period. Here's some pictures of my oven , it was a pottery kiln which was thrown out when a local school was demolished , I changed the elements from the coiled spring type and added the controller and thermocouple , the flask is just to give an idea of size. 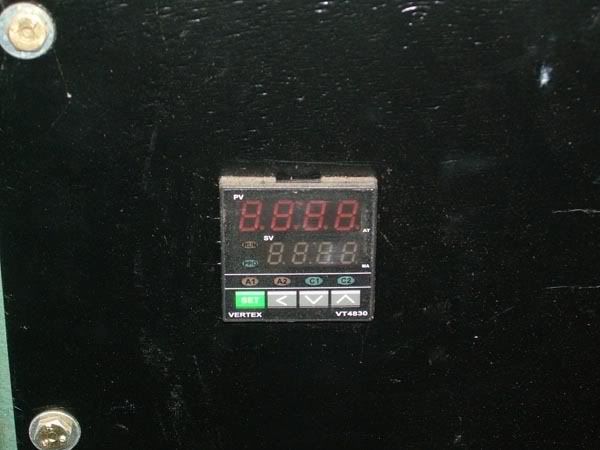  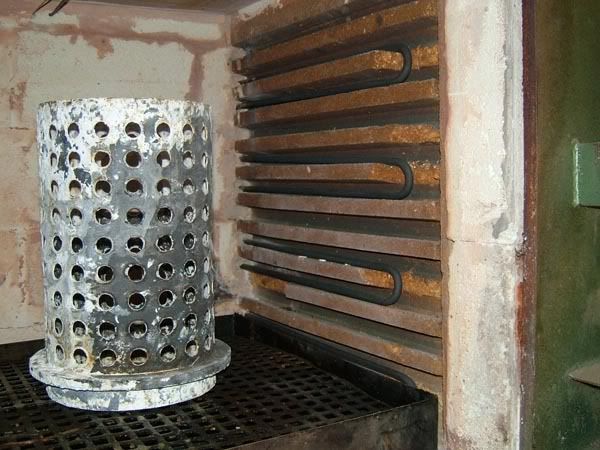 
|
|
Noddy
Statesman

Posts: 672
|
Post by Noddy on Jan 12, 2007 15:23:10 GMT
Can I suggest a source for the steam? If you are using plaster of paris as binder, it sets by hydrating to Gypsum CaSO4.H2O note the water of crystalization. half of this boils off at just over 100c taking you back to plaster of paris (CaSO4)2:H20.
Getting rid of that last remaining water requires greater heat. The end result is anhydrite (CaSO4) which is hard dense and very slow to re hydrate to gypsum, although it will do it; as one driller found out when he left 100m of rods down a borehole through Hartlepool Anhydrite mine. They are still there.
If it was plaster of Paris, I'm mildly surprised that the mould did not crumble
|
|
abby
Statesman

Posts: 928
|
Post by abby on Jan 12, 2007 16:32:08 GMT
yes indeed there is chemically combined water which will be driven of gradually but by the time firing is complete this has completely disappeared , the moulds after casting are solid yet able to be easily broken , you can dig the investment out with a screwdriver , which is desirable for recovering the castings , If you wait until the metal has solidified and plunge the moulds into water the steam generated is enough to turn the moulds to mush and the castings are almost clean of cement , this causes problems for me when disposing of the sludge so I prefer to leave the mould to cool and dig the investment out , it is suprisingly easy and a few clouts on the sprue with a hammer shakes it loose. Abby.
|
|
John Lee
Part of the e-furniture
Posts: 375
|
Post by John Lee on Jan 12, 2007 18:31:20 GMT
Hi folks, I'm new here but about to go on a model engineering adult education course with my dad. Crazy christmas present idea. Anyway, I don't know much about model engineering however I've spent a large part of today reading about casting using sand moulds, and recycled aluminium. Is there any reason why you would prefer lost wax over sand? There seem to be fewer stages involved, you keep the original and can do it all at home. I can see that it may take a little more cleaning up than lost wax would as the surface may be less clean. www.abymc.com/forum/These guys do a lot of their own casting and use essentially free scrap metal (aluminium cans etc..) and charcoal as fuel for melting it down. Not so crazy Christmas present idea. Welcome to a world that will fascinate you for the rest of your life if you want it to. Good on your dad!! There are lots of reasons to prefer lost wax over sand. Sand produces crude parts without detail, lost wax produces almost finished parts. It's like chalk and cheese. Read on... Welcome to the new hobby; I hope you stay. Regards, John
|
|
|
Post by AndrewP on Jan 24, 2007 23:26:22 GMT
For a good treatise on metal casting, albeit slanted towards jewellery and small sculpture try Practical Casting by Tim McCreight ISBN 0-9615984-5-X. Eminently readable, covers low tech methods like steam and sling casting (for the brave only the last one) and he actually does it. To start with I used an old enamelling kiln, manually controlled with a hand held thermometer and type K thermocouple, torch melted my metal and vacuum invested and cast with a fridge compressor. There are some pics on my website - www.agatehouse.co.ukbut it badly needs updating.
|
|