|
Post by springcrocus on Nov 6, 2016 22:55:32 GMT
I, too, use very small boring bars when neccessary but the one thing that everyone forgets to mention is their fragility. For a standard sized hole, a slot drill wins most of the time because, like a normal drill, it is self-supporting. The cutting forces either side of the centreline balance out and the tool doesn't break! A boring bar, on the other hand, can be very easily snapped because there is no support to the opposite side and they are particularly vunerable at tne moment that the tool hits the bottom of the hole. They will often take a nose-dive and snap so it is always a good idea to work to a dead-stop on the lathe.
Steve
|
|
|
Post by Roger on Nov 6, 2016 23:04:30 GMT
Hi Joan, I missed the second part of your original question. As Wilf points out, the hole size is approximate. It's quite possible for a 8mm drill, say, to go 0.2mm over size, particularly if it's worn or not sharpened symmetrically. If you use a drill that's say 0.2mm under the finished size you want, you can get much closer to the required size when you follow that up with the size you want. If I need it more accurate than that, I drill 0.2mm under size, then 0.1mm under size and then use a reamer to get it very close. Boring has its limits in that it can't always reach in as far as you need to go. It is the most accurate method of all though when done properly. Again, if you go too quickly to the finished size, you'll end up with a tapered hole or one will a 'bell' shaped entry.
|
|
|
Post by Roger on Nov 6, 2016 23:06:35 GMT
I, too, use very small boring bars when neccessary but the one thing that everyone forgets to mention is their fragility. For a standard sized hole, a slot drill wins most of the time because, like a normal drill, it is self-supporting. The cutting forces either side of the centreline balance out and the tool doesn't break! A boring bar, on the other hand, can be very easily snapped because there is no support to the opposite side and they are particularly vunerable at tne moment that the tool hits the bottom of the hole. They will often take a nose-dive and snap so it is always a good idea to work to a dead-stop on the lathe. Steve This is true, but you only bore the last bit, so that's not really such a big issue. Hitting the bottom of the hole is bad news, and another good reason to fit a digital scale to the carriage.
|
|
|
Post by springcrocus on Nov 6, 2016 23:08:52 GMT
I, too, use very small boring bars when neccessary but the one thing that everyone forgets to mention is their fragility. For a standard sized hole, a slot drill wins most of the time because, like a normal drill, it is self-supporting. The cutting forces either side of the centreline balance out and the tool doesn't break! A boring bar, on the other hand, can be very easily snapped because there is no support to the opposite side and they are particularly vunerable at tne moment that the tool hits the bottom of the hole. They will often take a nose-dive and snap so it is always a good idea to work to a dead-stop on the lathe. Steve This is true, but you only bore the last bit, so that's not really such a big issue. Hitting the bottom of the hole is bad news, and another good reason to fit a digital scale to the carriage. Aachooo. Sod it. Not as good as a dead stop, though. Steve
|
|
|
Post by 92220 on Nov 8, 2016 9:31:11 GMT
Roger, I think we should agree to differ. I'm sure we could both go on and on and get nowhere! Getting back to your original post, I have a method that I has stood me in good stead for the last 40 or so years. Drilling a deep, small diameter, hole (or almost any hole size for that matter) and getting it straight, is no real problem.I can drill a hole 2mm diameter, 1.1/4" deep in a brass bar and it will only go offcentre by around 0.0005". You may well think I am telling 'porkies', so I thought I had better do a test drilling and photograph what I had done. Here is a photo of what I did: 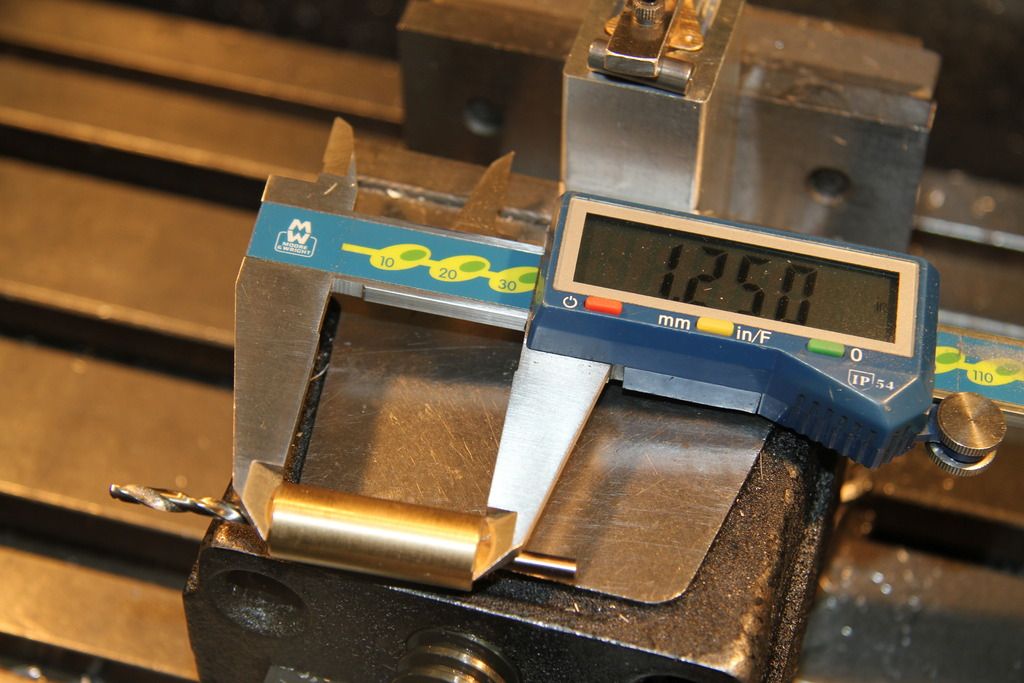 Anyone can do it. I learned this when I was an apprentice draughtsman. During that time, I had to work for 18 months in the development workshop in the company where I was trained, and I learned a number of tricks that have been very useful in my model engineering. This is how I get deep, straight holes - every time: Centre drill, but only drill the pilot diameter of the centre drill. Don't drill so deep you get the 60 degree starting to cut. Next, drill your hole. However, DON'T just push on down! Even a new drill will wander, as we all know. The trick is to drill a few thou and back off. Do this again and again and again. It must be a new drill, and fed a few thou at a time - around 10 / 15 thou at most. Use suds to prevent swarf sticking to the flutes and pushing the drill off-line. The feed-in must be VERY gentle too, so as to keep the drill cutting but not pushed so hard that the drill tries to bow under the load. That 2mm hole I drilled in that brass bar was straight, withing 0.0005". Yes you read it right - an 1.1/4" deep hole only wandered by 1/2 a thou. I set the piece of bar up in the Griptru chuck and made sure it was running true, with no movement at all on the 0.0005" DTI. I drilled the hole then reversed the bar in the Griptru and checked that it was still running absolutely true. I slid the 2mm drill into the hole with the shank sticking out. When I 'clocked' the shank, the DTI needle wandered just under one division - 0.0005". A deep hole can take a few minutes to drill, but the end result makes it worth the extra time taken.
|
|
|
Post by Deleted on Nov 8, 2016 10:09:40 GMT
nice work Bob...I'm not trained but the method you describe is exactly how I do these things...got lucky I guess....  Pete
|
|
|
Post by vulcanbomber on Nov 8, 2016 11:23:12 GMT
At work we get from NTK some solid carbide boring bars, the smallest the supply to us is 2mm diameter... Might be worth a look Roger, couldn't tell you cost however.
|
|
|
Post by Roger on Nov 8, 2016 11:47:42 GMT
Roger, I think we should agree to differ. I'm sure we could both go on and on and get nowhere! Getting back to your original post, I have a method that I has stood me in good stead for the last 40 or so years. Drilling a deep, small diameter, hole (or almost any hole size for that matter) and getting it straight, is no real problem.I can drill a hole 2mm diameter, 1.1/4" deep in a brass bar and it will only go offcentre by around 0.0005". You may well think I am telling 'porkies', so I thought I had better do a test drilling and photograph what I had done. Here is a photo of what I did: 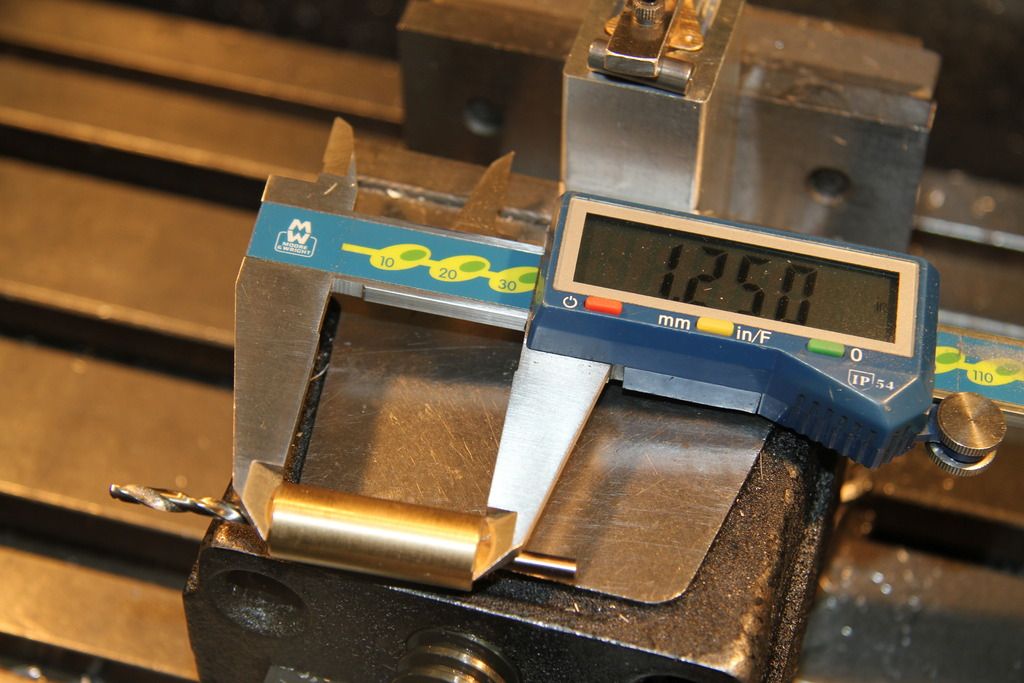 Anyone can do it. I learned this when I was an apprentice draughtsman. During that time, I had to work for 18 months in the development workshop in the company where I was trained, and I learned a number of tricks that have been very useful in my model engineering. This is how I get deep, straight holes - every time: Centre drill, but only drill the pilot diameter of the centre drill. Don't drill so deep you get the 60 degree starting to cut. Next, drill your hole. However, DON'T just push on down! Even a new drill will wander, as we all know. The trick is to drill a few thou and back off. Do this again and again and again. It must be a new drill, and fed a few thou at a time - around 10 / 15 thou at most. Use suds to prevent swarf sticking to the flutes and pushing the drill off-line. The feed-in must be VERY gentle too, so as to keep the drill cutting but not pushed so hard that the drill tries to bow under the load. That 2mm hole I drilled in that brass bar was straight, withing 0.0005". Yes you read it right - an 1.1/4" deep hole only wandered by 1/2 a thou. I set the piece of bar up in the Griptru chuck and made sure it was running true, with no movement at all on the 0.0005" DTI. I drilled the hole then reversed the bar in the Griptru and checked that it was still running absolutely true. I slid the 2mm drill into the hole with the shank sticking out. When I 'clocked' the shank, the DTI needle wandered just under one division - 0.0005". A deep hole can take a few minutes to drill, but the end result makes it worth the extra time taken. The method you describe certainly gets the best out of a correctly sharpened drill. I think It works because you're actually almost boring the hole with one flute being allowed to take more of s cut than the other. It's a kind of self centering boring bar. I use this technique too, but it does rely on excellent geometry of the drill and the tailstock being pretty true to get the hole to the right size. For small holes, carbide PCB drills work really well like this because they are so notch more rigid than HSS ones.
|
|
|
Post by Deleted on Nov 8, 2016 12:05:47 GMT
Some years back I drilled the bore for a long gun barrel...it was for a 1/16 scale model tank with fully working gun using a black powder charge including projectiles. The barrel was 13 inches long (this included breach and muzzle brake)and I had to drill/bore a 5mm hole down it's length, it wasn't as accurate as Bob has shown but it was good enough for the job in hand. Gun worked great, could shoot a round straight through timber of some considerable thickness. Did the same thing with model Cruiser guns...1/96th scale of 6" guns...with the rest of the ship of course. no projectiles with this, though, after all it would have been bad form to blow the head off an innocent duck as it paddled across the boating lake now, wouldn't it?
|
|
|
Post by 92220 on Nov 8, 2016 12:32:37 GMT
As I said earlier, I've not used carbide tools until I got hold of those screw shank carbide endmills. I will get some of the PCB drills and give them a try. You are right about the need for excellent geometry. No drill is going to give a decent hole if it is badly ground. That's why, if I have any holes that HAVE to be right, I always use a new drill as the starter drill because if the cutting edges are not evenly ground, there will be uneven cutting loads on the end of the drill and it will wander in deep drilling, no matter what you do. As you say though, boring is often the best way of getting a true hole, and certainly the best if you want a flat bottomed hole. Once I have an accurate hole, any subsequent drills, to open out, will, pretty closely, follow the path of the original drill, provided the corners are sharp and not micro-chipped. You mention about the tailstock having to be true. Agreed. One point that is not always realised is that a No 1 centre drill, being the smallest, will actually find the centre of a rotating bar because the actual dead centre is 'stationary'. i.e. it doesn't rotate in a circle, like points that are out from the centre. It remains in exactly the same place. A bit of a difficult concept to describe. That is why it is called 'Dead' centre. Once I have a centre, I put a small diameter drill in the tailstock and bring it up to just touch the centre hole. Careful watching of the tip as it touches, will indicate if the tailstock is out of line because the drill will move sideways. It's amazing just how small a movement you can see. Getting the tailstock true is relaively easy if you have a test bar to run between centres. As long as the tailstock guide face that runs on the inside face of the bed is hard up against it, and the test bar is then used to set the tailsock over until the bar runs true, it's only a case of always pull or push (whichever)the tailstock against the datum bedway to get a true centre. If the tailstock is not the original, then that is a different matter, because, Myford, at least, always matched the tailstock to the headstock on new machines, so one tailstock may well be slightly higher or lower than another. A No1 centre drill, though, will always find the 'dead' centre of a rotating bar, so that is a good start.
|
|
|
Post by Roger on Nov 8, 2016 12:47:06 GMT
Sometimes I have to drill out broken or damaged threads that are not only stuck in a hole, but someone has helpfully tried to drill them out off centre. Using this gentle touch down method with a carbide drill, I find them rigid enough to act as a slot drill if taken slowly enough, with repeated backing off, until it clears the off centre hole. You'll find the Carbide used in PCB drills to be of the highest quality. They have to be because they go down to 0.1mm diameter. If you look at those under the microscope, you'll see how good they are. Most of these are made in China. There certainly are poor quality carbide tools made there, but not all of them.
|
|
|
Post by 92220 on Nov 8, 2016 13:35:30 GMT
I will definitely give them a try. Thanks Roger.
|
|
robmort
Hi-poster

3.5" Duchess, finishing 2.5" gauge A3 and building 3.5" King
Posts: 174
|
Post by robmort on Nov 11, 2016 20:47:07 GMT
I agree with the general idea that Roger describes and I use a similar technique but with spare or broken HSS mills or even drill bits. The main problem with them especially in small diameters is rigidity and strength due to the presence of the flutes, compared with solid boring bars. So they need finer and more cuts. But at least any breakages are easy on the pocket.
Rob
|
|
|
Post by Roger on Nov 11, 2016 21:45:19 GMT
I agree with the general idea that Roger describes and I use a similar technique but with spare or broken HSS mills or even drill bits. The main problem with them especially in small diameters is rigidity and strength due to the presence of the flutes, compared with solid boring bars. So they need finer and more cuts. But at least any breakages are easy on the pocket. Rob Hi Rob, You'll find the rigidity issues are far less of a problem if you use any form of Carbide, whether that be drills or slot drills. It's probably worth seeking out a machine shop where they will probably give you as many worn carbide cutters as you can carry.
|
|