|
Post by Deleted on Sept 13, 2009 16:00:31 GMT
Well, following the successful design and construction of my hi-tech brazing hearth, I have now squared off the small end of the 15" long boiler barrel. The other end is to be cut and shaped to fit the throat plate, an exercise that fills me with foreboding! The big end is supported and gripped inside by the chuck jaws. To support the other end I made a 1" thick, slightly tapered hardwood plug, mounted on a long 8mm bolt, centre drilled one end. A long bolt was used so that I had a mandrel on which to make the plug. It was whacked in pretty tight to round up the barrel end to achieve something like a cylindrical form for the cutting process! A knife tool was used instead of a parting tool, in three passes, as I don't like plunge cutting copper that far from the chuck: nice and easy does it and lots of WD40! JB 
|
|
|
Post by Shawki Shlemon on Sept 15, 2009 10:02:13 GMT
Hi JB You are doing a great job and it will looks great when finished however in my humble opinion , one side of the barrel will be in the throat plate silver soldered , not to be seen again and the other side will end up inside the smoke box and will not be seen either so to me for barrel ends close enough is good enough but it is debatable and I fully respect your choice .
|
|
|
Post by Deleted on Sept 15, 2009 11:30:46 GMT
Hi Shawki. I take your point but I guess I just can't help it! JB
|
|
|
Post by Deleted on Sept 21, 2009 17:53:40 GMT
Well, it wasn't easy, and it isn't perfect, but the Firebox Wrapper looks OK and it appears to be the right size! It took me two days and I feel like I've fabricated a Knight's helmet!  For those who may be interested here is the sequence of events: Making the former out of 1/4" steel plate. The linisher makes this easier!  Having beaten out the throatplate from 10 gauge copper, I chose the old fashioned method of creating large holes!  Once again, the APTC drum sander comes in very handy. 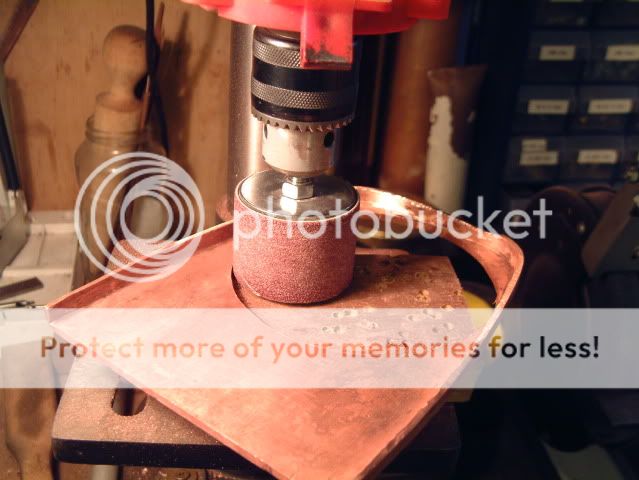 Throatplate and wrapper ready for assembly. The wrapper was bent by hand round the long bar you see later in this post.  Pre-drilled the wrapper. Started with a rivet in the centre of both, and dressed round the job, drilling and riveting one at a time on alternate sides. The long bar is the same radius as that specified for the wrapper corners, so it was relatively easy to maintain the correct form all the way along the wrapper.  All I have to do now is attach the boiler barrel! Wish me luck! JB
|
|
ace
Statesman

Posts: 528
|
Post by ace on Sept 21, 2009 19:36:21 GMT
Excellent work, was it done at 'Knight' Ha Ha Ha ;D
a piece to be proud of and well formed.
And yes best of luck with the rest, hope it comes together.
ace
|
|
|
Post by Deleted on Sept 21, 2009 19:43:44 GMT
Thanks Ace. Don't forget the old adage: 'Once a King, always a King, but once a Knight is enough!' JB
|
|
simonwass
Part of the e-furniture
Cecil Pagets 2-6-2 of 1908. Engine number 2299. Would make a fascinating model....
Posts: 472
|
Post by simonwass on Sept 21, 2009 22:30:50 GMT
This isn't a criticism as your making a fine job of the boiler. Why so many rivets, 5 is plenty to hold it together and square, any more is just extra bits that need silversoldering and chances for leaks. My dad never uses any rivets, just tacks, checks its still square, then fills in between tacks. I do like a few rivets to make sure ;D
|
|
|
Post by Deleted on Sept 22, 2009 7:25:35 GMT
Why so many rivets, 5 is plenty to hold it together and square, any more is just extra bits that need silversoldering and chances for leaks. I'm a little concerned about the potential for leaks as well, but I'm using those rivets because the words and music tells me to, and as this is my first loco I don't know any better. Perhaps when I'm older and wiser I'll do something differenter! JB
|
|
|
Post by Shawki Shlemon on Sept 22, 2009 10:38:26 GMT
Everything looks fine to me , congratulation . I have one question and that is how are you going to join the throat plate to the tube by brazing or silver soldering ? Here if we do it the way you have we must braze the joint or to silver solder we must form a flange ( minimum 3t ) .
|
|
|
Post by Deleted on Sept 22, 2009 10:56:38 GMT
Hi Shawki. The design calls for a silver soldered butt joint. I had a word with our boiler inspector and he's quite OK about it. I'll use a wide range solder which will form good fillets. Might have something to do with the fact that he drives an LBSC Brit of his own! I'm more concerned about the close joint that I've made. I can't guarantee penetration to the inside, so I might just remove those rivets and put some 4 thou solder foil in and rivet up again.
JB
|
|
simonwass
Part of the e-furniture
Cecil Pagets 2-6-2 of 1908. Engine number 2299. Would make a fascinating model....
Posts: 472
|
Post by simonwass on Sept 22, 2009 11:37:03 GMT
Don't bother trying to dismantle, if you are concerned the assembly is too tight you could try a little easing of the join with a bit of persuasion with wood chisels etc to make a bit (only a few thous) of a gap. You will be able to check for penetration as its a sub assembly, do it with silverflo24 (or equivalent) and if necessary put some in from other side, problem with sub assemblies leaking is that you will be trying to seal leaks from the other side to which you 1st made the joint, its always easier to make leaks good if there is a full bead of solder (with a tiny bad bit!) than making a full bead where there wasn't one due to bad penetration. Given enough fluxing and perfect cleanliness silversolder is amazing stuff at getting through tiny gaps. The weird thing with riveting boilers for silversoldering is that technically you should 'lightly' make the rivet to allow for penetration, the assembly is then only lightly held together and sort of defeats the riveting in the first place!
|
|
|
Post by welshy on Sept 22, 2009 18:09:09 GMT
Looking very good JB. The rivets will ensure that the 2 adjoining surfaces are a nice snug fit eliminating larger gaps which are harder to fill with the capillary action of the flowing silver solder. Traction engine boiler have a large number of rivets on the back head/wrapper. It is personal choice i suppose as to how many rivets, but yours look good to me. Keep up the good work, the Brit boiler isn't the easiest to start on either so a brilliant first attempt. Mike
|
|
|
Post by Deleted on Sept 22, 2009 22:50:39 GMT
Forgive my French, but this job was a proper little b*gger! Words and music says 'fit the barrel to the throat plate'. What an understatement! Keeping the correct axial orientation was a nightmare, and I think it droops just a little too much even now. I might just fettle it a bit more tomorrow before I silver solder it. BTW I received ten excellent vermiculite bricks today, £20 including postage! 
|
|
redmog
Part of the e-furniture
Not Morgan weather
Posts: 461
|
Post by redmog on Sept 23, 2009 6:37:12 GMT
Looking Excellent.
Great progress JB. It's not the droop of the boiler I'm looking at. It's the droop of the angle brackets carrying all that non-ferrous in the background. Amassing what load a couple of screws can carry. Simon and Baggo - thanks for the knowledge.
Chris
|
|
|
Post by Deleted on Sept 23, 2009 8:19:09 GMT
Talking of droop! Before I go any further, and ignoring the words and music just this once, I'm going to knock up and attach the backhead temporarily, to get the exact 1/8" rearwards slope in relation to the boiler barrel. This just to make sure that the only excessive droop I get is the one associated with my age group! JB
|
|
|
Post by Deleted on Sept 24, 2009 17:18:02 GMT
Disaster!The barrel moved a little on the throatplate while being soldered. I had relied on gravity to keep it place: I won't do that again! My high precision fit (which took me all morning to do) turned into a 1mm gap on the lower left side!There was solder running everywhere but into a fillet. Do I hacksaw it off flush and refit, or try and melt it off? I suspect the former will be the case, and I'll land up making a longer smokebox! JB BTW, no trouble getting the assembly hot enough with my new cheapo bricks.  !
|
|
|
Post by chris vine on Sept 24, 2009 18:01:01 GMT
Hi JB,
Looks pretty good to me. Not quite sure what your problem is. Did the solder fill the gap in the end? are you worried about the bit of solder on the face of the throatplate or has it ended up a bit crooked in the firebox?
if you have managed to fill the gap and make it tight, and it is a little crooked I am sure you can gently coax it into shape. You might make a block of wood which fits in the firebox and something similar in the barrel and then persuade it to the shape you want. Of course you know already that the copper will be like butter at the moment.
As long as the gap has filled, I think the very last thing I would do is to try to melt it out or cut it off.
Only my thoughts!!!
Chris.
|
|
|
Post by Deleted on Sept 24, 2009 18:32:37 GMT
Hi Chris. I'm afraid daylight can be seen through the two little slots! Also the barrel is supposed to be flush with the top of the firebox wrapper, and it has slipped 3mm downwards. That's why it is a disaster! JB
|
|
simonwass
Part of the e-furniture
Cecil Pagets 2-6-2 of 1908. Engine number 2299. Would make a fascinating model....
Posts: 472
|
Post by simonwass on Sept 24, 2009 23:02:47 GMT
Did the barrel not fit through a hole in the throaplate, I don't understand why it has moved down by 3mm? Should the barrel rest on the throatplate? Any gaps can be filled with slivers of copper and silversoldered over. Save any sharp slivers when you nibble plate with tinsnips, or make longer flat bits by hammering slivers to fit. You could also persuade the plates to fit closer, a few taps with a small riveting hammer does wonders. You can melt the barrel off but you'll need to get it hotter than the temp you needed to make the join, I had to do this once and hope never to do so again. Some help with easing the barrel off whilst you heat will be necessary. Does the barrel fit into the smokebox or up against it with a sealing strip? If it fits inside the 1/16" you'll loose sawing it off is nothing.
|
|
|
Post by baggo on Sept 24, 2009 23:53:19 GMT
Ouch JB  Just studied the drawings in the articles and realised that the barrel just rests on the throatplate without a joining ring or similar. It is a pure butt joint and I am surprised your boiler inspector ok'd it  I wouldn't be happy with such a joint in such a crucial area. What to do? I would very carefully saw off the barrel from the throatplate, clean everything up, and fit a joint ring inside the barrel that fits into the hole in the throatplate. That will give a much stronger joint and locate the barrel positively. At the worst, you are only going to lose the width of a sawcut of the barrel length. However, there does seem to be a bit of an anomaly on the drawings in that the diameter of the hole in the throatplate is equal to the inside diameter of the boiler barrel ,which would suggest that the top of the barrel is actually flush with the top of the throatplate rather than the top of the firebox wrapper? You might have to make a stepped joint ring if you do want the barrel to be flush with the top of the firebox wrapper. Just my thoughts, John
|
|