|
Post by Deleted on Oct 17, 2009 18:32:45 GMT
JB, there was a Britannia boiler in the same stage of yours but soldered at the Midlands show plus the rolling chassis again in the same advanced build as yours I had to do a double take on the builder to see if it was you, I took some pictures with my phone I'll see if I can get them on here. Hi Spamcanman! Thanks for the thought, it will be interesting for us all to make a comparison. I'll be there myself on Monday with my camera and I'll look out for it! JB BTW I just remade the two outer crown stays, they were in an awful mess! It fits together properly now.......
|
|
|
Post by welshy on Oct 17, 2009 18:46:20 GMT
Yes i saw the Brit boiler as well, I noticed it that it had a butt joint with a lap strip which was soldered onto outside of the barrel. There were a few more 3/1/2 and 5" Brits some finished and some at the chassis stage so a lot for you to compare John. Mike
|
|
|
Post by spamcanman on Oct 17, 2009 22:50:03 GMT
you could always pop over to Western Steam and have a chat with Hellen Verrall she has some of her work (boilers) on display she will be very helpful with advice.
|
|
|
Post by Deleted on Oct 19, 2009 20:12:43 GMT
I'm posting this negative set of pictures in the spirit of this forum: the first 'I told you so' comment will get an appropriate response! I've had some success using EasyFlo 2 in the kiln for small stuff, so in went the firebox prepped up with some Cupalloys 440: 650-710 C melting range. That's 12 quids worth of solder!  I took it up to 720 - to be sure- to be sure- and when I opened the lid it looked as if nothing had moved: no real melting, and certainly no penetration into the rivet heads etc. In fact, some of the silver solder pieces looked like they had been entirely unaffected by the heat. I took it up to 740, thinking that there was something wrong with the kiln controller (it's normally spot on for pottery glazes), but when I opened the lid, it was the same! By this time I was seriously disappointed with the results. I put it in the pickle and this is what I found. This shows the outer tubes have fillets, but the inner ones are seriously 'unmelted'. There is no penetration.  The solder rings placed inside the chamber haven't even slid down to touch the outer wall.  The solder placed on the firebox ring just gave up! 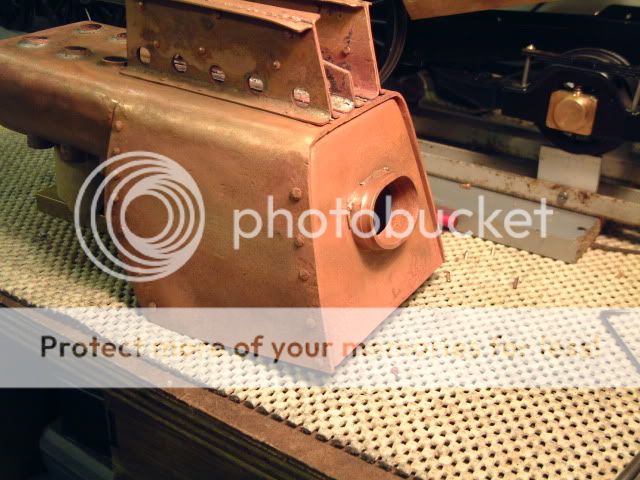 I spoke with the Cupalloys man at the show today. He said that I had 'got away' with the kiln method using EasyFlo 2 as the melting range is only ten degrees, and the constituent parts don't have a chance to separate during the heating period of some 45 minutes. 'However' the 440 has a range of 60 degrees, and he maintained that the lower melting point constituents had melted out, leaving high melting point components in their original positions. Trouble is, I can't find any 'low melting point' residues. He told me I would have to melt out the residues and start again using the traditional method...... Oh well, it was worth a try! JB
|
|
|
Post by drjohn on Oct 19, 2009 23:21:50 GMT
What a bummer JB.
I'm no expert, but I'd be inclined to do the same kiln experiment on some scrap copper, then afterwards see if you can get it to flow with a load of flux and oxy-propane.
DJ
|
|
redmog
Part of the e-furniture
Not Morgan weather
Posts: 461
|
Post by redmog on Oct 20, 2009 13:49:20 GMT
Chin Up.
It was worth a try JB. I'm sorry that it didn't work out, but it might have done! Then we would all have been 'much he wiser'. In fact we are much the wiser. If it were not for folks like you, this forum would not have the spirit it has. OK - back to the blow torch. I don't see much of a problem with what you have, unless I've missed something. It all seems structurally secure and is just waiting for the silver solder to make it structure sound. I see no problem with something like easi flo no 2 and a good blowtorch making good joints of the firebox. The parent metal needs to be up to temperature and the easi flow applied, letting the metal melt the solder - Not the torch.
Whatever the outcome - keep us posted. If it were not for the 'I told you so's' model engineering clubs would be boring.
Chris
|
|
|
Post by drumkilbo on Oct 20, 2009 14:00:57 GMT
I'm sorry to see that result as well JB, particularly as you were getting on so well. Was it you or someone else on the forum who had already tried silver soldering in the kiln ? I seem to remember it worked alright then. Ian.
|
|
|
Post by Deleted on Oct 20, 2009 14:26:37 GMT
Yes, it was me who started the kiln thread over a year ago, It works with EasyFlo 2, no problem. GRRRRRR! I've nearly fixed the firebox, you'll see some piccies tonight! JB
|
|
|
Post by garethp on Oct 20, 2009 18:42:55 GMT
I dont get it, the kiln was hotter than the highest temp in the range of the solder yet it didnt completely melt? I'm thinking that the mixture of high and low temp materials lowers the overall melting temp so that if the low temperature materials melt and presumably boil off then the remaining material's melting point increases?
If thats the case then wouldn't vastly shortening the heating time fix the problem? I'm thinking that your kiln is a few (3?) kw and the usual boiler making kit seems to involve a massive amount of heat (many 10's of Kw's) to keep the heating times down. Doesn't the flux disappear well before the 45 mins heating period is up?
Keep up the good work anyway, I'm very jealous of the progress your making!
|
|
|
Post by Deleted on Oct 20, 2009 22:31:39 GMT
Gareth, I do believe that you are spot on with your analysis. However, it's not pretty, or up to the standard I wanted, but I seem to have rescued the thing this afternoon. About five stages were involved, pickling and cleaning in between each one. I must have used about £25 worth of solder though! If it leaks after all this trouble I will go back to steam boats!  Every rivet head had a litle ring of solder on it to prevent leaks......  Rivets have been covered inside and out.  Seem to have proper penetration. Ooh, what a lovely word....   Fire tubes and foundation ring to finish it tomorrow.......
|
|
|
Post by baggo on Oct 20, 2009 23:19:51 GMT
Well done, good recovery JB. I think a quick celebratory drink is in order  John
|
|
|
Post by drjohn on Oct 21, 2009 4:47:51 GMT
Well done, good recovery JB. I think a quick celebratory drink is in order  John I'm on my third bottle of Beer na Beer in his honour, and it's only just lunch time. DJ
|
|
brozier
Part of the e-furniture
Posts: 335
|
Post by brozier on Oct 21, 2009 7:34:11 GMT
Looks Good JB,
I might be tempted to add a bit more Silver Solder round the tube plate join when you come to do the tubes. May just be shadows on the picture though!
For cleaning that area a Dremel tool with a circular brass brush works wonders with any stubborn flux.
Cheers Bryan
|
|
|
Post by Deleted on Oct 21, 2009 7:54:56 GMT
Thanks everyone for the sympathy and encouragement! I won't finish it today as I've just realised that I have to make all the bushes and braze 'em up. Perhaps tomorrow......!
BTW:our boiler inspector suggested Monel for the 20" x 3/16" longitudinal stays. If I take that on board where would one obtain such exotica? And at what price?! JB
|
|
|
Post by Shawki Shlemon on Oct 21, 2009 9:20:32 GMT
Hi JB What is wrong with hard drawn copper rods for the longitudinal stays ? I think they are better . has the boiler inspector a reason for that ? If so what is it ?
|
|
|
Post by Deleted on Oct 21, 2009 9:29:12 GMT
Hi Shawki. I told our man I couldn't find any copper material at the model show and I can only quote the (always helpful) response.
It is usual to use Monel stays for the longitudinal stays these days most of the side stays can be done with copper rivets leave them long and cut them off after the boiler is completed. Leaving them long helps the flow of solder as they act as heat sinks.
What does 'usual' mean? Mandatory? JB
|
|
redmog
Part of the e-furniture
Not Morgan weather
Posts: 461
|
Post by redmog on Oct 21, 2009 11:04:07 GMT
Drawn PhBr Long Stays?
I'm in the same boat JB. I was thinking on the lines of Drawn Phosphor Bronze. Not that I have researched its availability.
Chris
|
|
|
Post by baggo on Oct 21, 2009 11:16:07 GMT
JB, I would be very surprised if anyone uses Monel nowadays. Martin Evans used to recommend it but I believe it's dreadful stuff to work with and very expensive (assuming you can find a supplier for small quantities). If you want something a bit stronger than copper then use phosphor bronze. You can get it in small diameters. Your blower stay will have to be copper anyway, usually 16g copper tube. Martin Evans was of the opinion that the horizontal stays probably do b/all anyway. I think LBSC fitted them to hold the barrel onto the throatplate  ;D John
|
|
|
Post by mutley on Oct 21, 2009 11:20:10 GMT
copper is 'usually' used for the longitudinal stays. I havent seen monel around for a long time.
My understanding of silver solder is that when you heat it the lower melting point elements like cadmium melt/burnout first. This is why you need to get the assembly up to heat before applying the solder. If the solder doesnt run when you apply it then the assembly isnt hot enough. Cadmium free solder doesnt run unless the work piece is hot enough for this reason.
Talking to Gerry Burchill at one of the shows recently he had all his assemblies vacuum brazed with copper. The conversation got around to could you use the same process on a copper boiler. His supplier reckons so but I seem to remember there beign some issues around how and what you use for the solder medium.
Hope this all makes sense, I hate writing hence most of my post are short!
Andy
|
|
|
Post by Deleted on Oct 22, 2009 8:09:12 GMT
I'm probably going with drawn PB stays instead of the copper: it costs about the same and is stronger. I just have to check out their respective C of LE.
BTW the boiler inspector is away until the 31st, and I can't put the boiler together until he's seen the two components. I'm suspending further work on the boiler until then so that I can get on with a bumper edition of the SMME Newsletter!
You're OK for now Chris, take a holiday! JB
|
|