|
Post by ron on Feb 23, 2006 10:39:46 GMT
Hi All I've noticed a couple of sellers selling 4" rotary tables on Ebay recently at a reasonable price and I'm tempted, are they a worthwhile accessory? at present I use the graduated scale on my milling vice [probably not very accurate] for indexing things like cylinder cover bolt holes etc would a rotary table be better? Ron
|
|
|
Post by ukjimoo on Feb 23, 2006 12:19:03 GMT
I bought a 6" one because i had 2 drill the 3 pinion shaft holes in my traction engine diff. They had to be at exactly 120 degrees to one another or the whole thing wouldnt mesh. It worked perfectly although at the time i thought i had wasted a lot of money. Since then it has had numerous uses. On one occasion i put my taper shank chuck into the middle of it to drill 6 tiny holes in the end of my safety valve adjusters. I could never have achieved that without it as they were very close together and there was hardly any room to play with. I think money is never wasted on tools, they often get you out of the brown stuff at a later date. 
|
|
|
Post by Jo on Feb 23, 2006 12:53:01 GMT
A cheaper solution may be to make yourself an indexing chuck using a large toothed gear. I have a 10" dia 120 tooth gear, with indexing peg with a 8" three jaw mounted on it and it is great.
But if you are looking to do a bit of milling with the table is a 4" not a bit small? Tool maker's buttons may be just as good.
|
|
|
Post by Malcolm on Feb 23, 2006 21:11:23 GMT
If you are going to buy one, definitely go for a six inch. Four inch is too small to be useful for most ME work.
|
|
|
Post by chris vine on Feb 23, 2006 21:23:01 GMT
Hi, I found that the indexing type with a myford nose spindle more useful as it takes a chuck directly. You can turn a cylinder cover, move the chuck to the divider in the mill and drill the holes.
Horses for courses I guess! Chris
|
|
|
Post by Tel on Feb 24, 2006 7:51:08 GMT
For some work they are just about indispensable. Mine is home made & mounts either a 4" table or a 3" 3 jaw chuck. A gear mounded indexer is OK, but you are limited to the divisions of the number of teethon your chosen gear. I have a home made one of those as well - no gears, just a reversable disk with 60 'oles one way, 40 t'other. Useful, but my rotary table (based on a 60t Myford gear) is graduated at 1/2° and I can get 1/4° pretty accurately - certainly good enough for the work I do.
 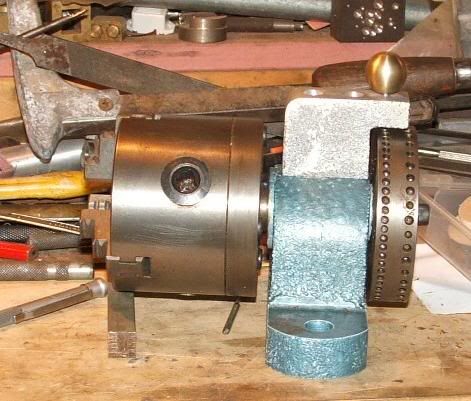
|
|
jackrae
Elder Statesman
 
Posts: 1,333
|
Post by jackrae on Feb 24, 2006 9:35:26 GMT
And today's competition is to count and identify the number of different tools lying on Tel's bench I reckon there must be at least 20 items Nice to see someone who uses his bench the same way as I use mine Makes me sick to see those model builder photos with not a sign of swarf or tools anywhere
|
|
|
Post by Tel on Feb 24, 2006 10:14:59 GMT
And that was on a 'tidy' day
|
|
|
Post by jgb7573 on Feb 24, 2006 10:17:57 GMT
I'd certainly go for one if you do much milling. With a peg mounted in the centre, it's dead easy to round the end of con rods (or whatever). Last thing I used mine for (probably not the most sensible, but I fancied having a go), was to machine the outside of eccentric straps from solid. OK so I could have done this by filing, but I had fun working out the angles and seeing it work.
I have a six inch table. I centre it under the spindle with a length of 3/8th silver stell held in the Posilock chuck and adjust the table until the rod slides into a reamed hole in the central plug of the table. Near enough for most work I do, and quick.
|
|
|
Post by 3405jimmy on Feb 24, 2006 12:56:04 GMT
I I have a six inch table. I centre it under the spindle with a length of 3/8th silver stell held in the Posilock chuck and adjust the table until the rod slides into a reamed hole in the central plug of the table. Near enough for most work I do, and quick. John, That sounds a good idea on centring the table I think I will give that a try. Jim
|
|
|
Post by havoc on Feb 24, 2006 13:18:50 GMT
Count me in as well.
|
|
dscott
Elder Statesman
 
Posts: 2,438
|
Post by dscott on Feb 24, 2006 15:02:59 GMT
I bought a kit one years ago and looked at it last week, trouble is that everywhere I have worked has one so never bothered to machine it. Then cnc comes allong and they all end up on ebay.
David.
|
|
|
Post by Donald G on Feb 24, 2006 21:28:47 GMT
Thanks very much for the idea for centring the rotary table on the mill, much easier and quicker I can see.
I will make bits tomorrow for that
Donald
|
|
|
Post by Peter W. on Feb 26, 2006 15:40:06 GMT
I have a six inch table. I centre it under the spindle with a length of 3/8th silver stell held in the Posilock chuck and adjust the table until the rod slides into a reamed hole in the central plug of the table. Near enough for most work I do, and quick. Yes, that's what i do usually. I once tried the "Osborne move" I think it's called -- using a wiggler, first from left to right, and then front to back alternately. After a few cycles, it's supposed to centre a spindle very accurately. My attempt turned out to be less accurate than the rod/reamed hole method ! I must have done something wrong, but blowed if i know what.
|
|
|
Post by jgb7573 on Feb 27, 2006 12:55:37 GMT
By the way, I wish I could claim credit for the 'rod in chuck and reamed hole in rotary table' idea, but it was told me by a member of my club, along with many other good ideas. Club's are a great thing, if prone to argument 
|
|
|
Post by the_viffer on Feb 27, 2006 16:37:24 GMT
By the way, I wish I could claim credit for the 'rod in chuck and reamed hole in rotary table' idea, but it was told me by a member of my club, along with many other good ideas. Club's are a great thing, if prone to argument  I've used the method furtively for a few years. I've never dared own up to it before in case it enhanced my cowboy status. I'm pleased to find it is pc!
|
|
JohnP
Hi-poster

Posts: 186
|
Post by JohnP on Mar 1, 2006 12:45:48 GMT
I've used the "rod in chuck" method the other way round. That is, I put the rod (snug fit) in the centre hole of the rotary table, then loosely clamp the chuck backplate to the table. Tighten the chuck jaws onto the rod and nip down the clamps. That way the chuck jaws are concentric with the rotary table (well at least at that diameter!)
JohnP
|
|