jma1009
Elder Statesman
 
Posts: 5,917
|
Post by jma1009 on Mar 10, 2013 21:37:53 GMT
one of the most important tools in copper silver soldered boiler making (in my workshop anyway) is a set of feeler gauges. a 2 thou and 4 thou feeler gauge is run around every joint. ideally i aim for the 2 thou feeler to go round easily but the 4 thou feeler to be tight. if not then corrective action is required before silver soldering up. very careful attention should be paid to the top and top curves of the inner firebox.
phil, the objection to a strip of copper round the outside of the barrel/throatplate butt joint is that the quality of the butt joint is hidden. such an addition would i think need the agreement of your boiler inspector first. adding rivets to the flanged joint to the throatplate to the outer wrapper doesnt prevent the butt joint itself against the barrel opening up later on. one just needs to be very careful, and the advantage of propane is that the whole boiler gets pretty hot avoiding localised stressing. i should add however that when i do 'new' joints near an already completed joint the whole lot gets fluxed up.
pete, if you can get tenacity 5 (for stainless) then you should be able to get tenacity 4A (or thessco F) which will be even better and also easier to remove after silver soldering. the companies who make the fluxes and silver solder have spent many years reserching the best for each application, and i see no reason to buy something for a valuable item such as a locomotive boiler that isnt exactly what is required.
cheers, julian
|
|
peteh
Statesman

Still making mistakes!
Posts: 760
|
Post by peteh on Mar 11, 2013 0:36:12 GMT
Both firebox plates have now been trimmed to the correct height and at a club run day shown , with the Northumbrian, to those who attended. A few had built boilers before and didn't say they were no good  . Also actually tested the fit of Northumbrian on our elevated track for the first time - and it fits  (of course it had to but it's nice to confirm that no mistakes in readings/building were made)
|
|
philh1
Involved Member
 
Posts: 64
|
Post by philh1 on Mar 11, 2013 20:35:48 GMT
Pete, That seems like a good plan to me i.e., to make sure the gauge fits. I have assembled my tender chassis and I plan to take it along to my local club to make sure it fits too.
Julian, when you say that the rivets do not prevent the butt joint from opening up - are you able to say what happens. For example, if the joint is riveted with the correct silver solder clearance between the plate and barrel, is it stress that pings the plate away combined with melting solder or is it just that the solder has the tendency to flow away from the joint because it gets too hot?
PhilH
|
|
jma1009
Elder Statesman
 
Posts: 5,917
|
Post by jma1009 on Mar 12, 2013 1:07:30 GMT
phil, to be honest with you i dont know the answer, because ive never had such a problem with my own boilers. however there is a very interesting old thread on this site regarding the LBSC BRITANNIA boiler, and many others i have examined that failed a test. i cut up one 5"g boiler to examine for myself. the results were somewhat startling especially as it was sold through the trade. the thermal stress when heated up to near enough (or at) the liquid re-melting point temperature of silver solder in subsequent heat ups must be a cause, especially due to the butt joint not relying on any mechanical assistance. however others far more expert than me would be able im sure to provide the reasoning. LBSC did comment on this a few times... but he used sifbronze to braze up most of his boiler joints using oxy-acetylene, and was therefore somewhat separated from what the ordinary model engineer was able to do at the time. i am a little surprised that others havent come forward to offer help and advice on this thread re the NORTHUMBRIAN boiler. cheers, julian
|
|
peteh
Statesman

Still making mistakes!
Posts: 760
|
Post by peteh on Mar 17, 2013 12:09:59 GMT
No pictures today but basically the boiler was pretty happy about my firebox plates, but suggested I use metal formers for tubeplate and backhead as they as 2.5mm (nearest metric to 3/32!) thick - I was finding that the 1/2" ply formers I made for the firebox plates were on their last legs by the time I had finished them. Spent most of yesterday afternoon and some of this morning making the new front tubeplate former and part of this afternoon sweltering and starting the copper bashing (very humid day here in W.A). Did 5 anneals and have got 3/4 of the way I reckon. My daughter has now started her 1st year of uni which is 15 minutes away from the office I work in, so I pick her up most days, the return trip however adds over an hour to my drive home so I am not getting any progress during the week 
|
|
RLWP
Part of the e-furniture
Posts: 319
|
Post by RLWP on Mar 17, 2013 13:43:02 GMT
Too late now, you could have made your formers out of 1/8" plate backed with plywood.
Richard
|
|
philh1
Involved Member
 
Posts: 64
|
Post by philh1 on Mar 17, 2013 22:29:15 GMT
Pete,
Right!! I was hoping to avoid using steel formers (hence my previous question about them). Looks like Ill be hacking them from steel plate. Im glad that Northumbrian plates are simple.
PhilH
|
|
|
Post by Jim on Mar 18, 2013 0:22:56 GMT
Hi Phil and Pete, What material to use for your formers as always comes down to personal preferences. I used 5/8" MDF for all the formers for Boadicea's 2.5mm plates including the double flanged throat plate without any problems at all and certainly with no damage to the formers. The MDF is easy to shape, I used a jig saw and for the curved profiled edges, a router. For the small plates I used a single thickness and a doubled (off cuts held with liquid nails) for the big plates such as the throat plate. You do need to make sure the copper is firmly clamped to the plates to prevent distortion and that the plates are well supported at the back to stop springing, I used a bit of thick square section tube for that. In the end as always, the choice is yours and what you feel comfortable with, it's your model and your creation.  I added the pictures to show the MDF throat plate former after it was used and the method I used to clamp the copper to form the tube plate. Jim 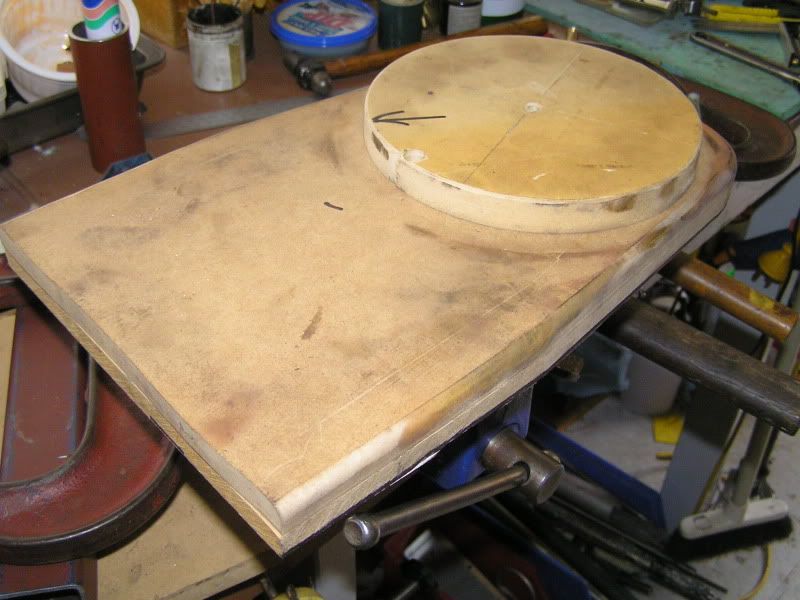 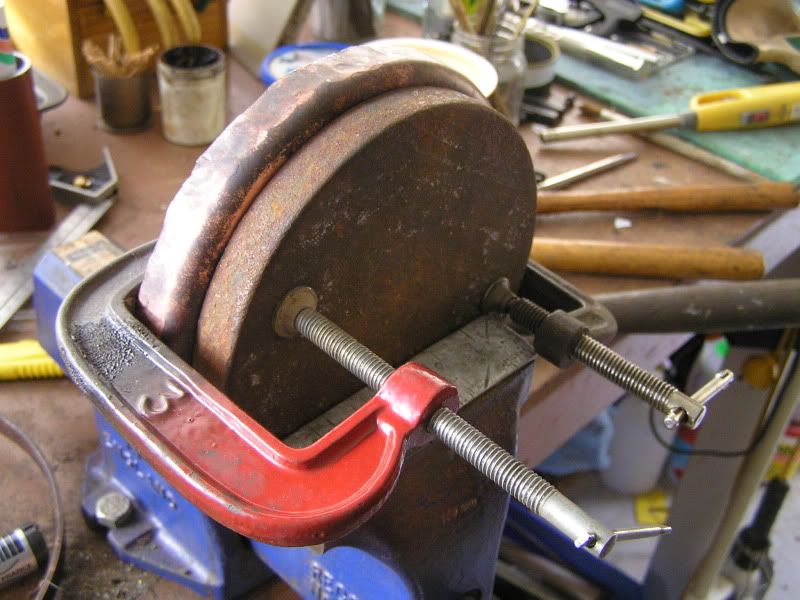
|
|
peteh
Statesman

Still making mistakes!
Posts: 760
|
Post by peteh on Mar 18, 2013 3:38:11 GMT
Thanks for those photos Jim, looking at the second one I wonder if I am not clamping sufficiently - basically using a single F clamp in the centre. - something else to investigate and experiment with. Phil - Once I've made my boiler I could always mail you my formers - one option if the timing works.
|
|
|
Post by Jim on Mar 18, 2013 6:35:06 GMT
looking at the second one I wonder if I am not clamping sufficiently - basically using a single F clamp in the centre. Hi Pete, Forming boiler plates is rather like rolling dough in that you're squeezing and stretching the soft annealed copper with your hammer to form a new shape. Basically you clamp the copper so the only metal free to move is the section being worked on, in this case the flange. Keep experimenting and you'll soon get a system that works for you.  Jim
|
|
peteh
Statesman

Still making mistakes!
Posts: 760
|
Post by peteh on Mar 18, 2013 10:31:59 GMT
Thanks Jim
|
|
peteh
Statesman

Still making mistakes!
Posts: 760
|
Post by peteh on Mar 29, 2013 11:19:07 GMT
After reading Jim's advice re backing the copper to prevent springing things have progressed more quickly, up to a point. Formed the tube plate to final former dimension and went to test fit into boiler tube - in a nutshell, it didn't. Quickly realised I had only reduced the former by 2.5mm, not 5mm to allow for the material thickness on BOTH sides of the former (insert head plant here!  ). Reduced the former by another 2.5mm and re-formed, now a nice snug fit in the barrel with a sliver of daylight discernable when held up to the light. Sunday is club public run day so won't get much if anything done but Monday hope to start on the back plate. All in all a Good Friday  (sorry guys!) Attachments:
|
|
|
Post by Jim on Mar 29, 2013 22:23:05 GMT
Well done Pete, it's a nice feeling when you get things just the way you want.  Jim
|
|
Smifffy
Statesman

Rock'n'Roll!
Posts: 943
|
Post by Smifffy on Mar 29, 2013 23:38:04 GMT
Two doors hung and a radiator swapped here. Most definitely not a Good Friday :-(
|
|
peteh
Statesman

Still making mistakes!
Posts: 760
|
Post by peteh on Mar 30, 2013 5:57:21 GMT
Cheers Jim, always nice when there is forward progress. Smiffy - Only bad if you have to rehang the doors!, otherwise they are done and tomorrow can be a workshop day 
|
|
peteh
Statesman

Still making mistakes!
Posts: 760
|
Post by peteh on Mar 30, 2013 11:24:50 GMT
A little more forward progress - I have cut and shaped the back plate former from 3mm steel and added a wood backing, and also cut out the blank rectangle for the copper plate. After this plate has been formed I will have tried three methods of former - Solid Wood (ply), Solid Steel and steel plate + wood. It will be interesting to compare ease of making the former and ease of forming the flanged plate with each method. The one thing I love about this hobby is there is generally more than one way of being 'right'  Run day tomorrow so will probably wait until Monday - I LOVE long weekends !
|
|
peteh
Statesman

Still making mistakes!
Posts: 760
|
Post by peteh on Mar 30, 2013 13:35:10 GMT
Question to Doubletop - was your throat plate flanged to the boiler barrel?
|
|
Smifffy
Statesman

Rock'n'Roll!
Posts: 943
|
Post by Smifffy on Mar 30, 2013 20:31:01 GMT
Sadly, today was patching up the floor from fitting the radiator, followed by painting two ceilings and a trip to the dump. Tomorrow, is the walls.
Roll on return to work :-(
Smifffy
|
|
|
Post by doubletop on Mar 30, 2013 20:47:42 GMT
Pete No I didn't. I checked to see if I had a picture but I haven't go one I'm afraid. This is the nearest I have  I did extend the outer flanges to make some 'ears' to allow a rivet at the top and patch the hacksaw cut at the point the barrel and firebox join. Hope that helps Pete
|
|
peteh
Statesman

Still making mistakes!
Posts: 760
|
Post by peteh on Mar 31, 2013 7:50:14 GMT
Thanks Pete,
Originally my boiler inspector had said if I was doing a straight butt joint it would need to be made with 'Tobin bronze' (as per our codes) or flanged and silver soldered. Today he was happy if I butt silver soldered and made a larger fillet on the outside of the join - much simpler and no double flange ;D
Very busy day with 6 parties + general public but with up to 6 locomotives on 2 tracks we coped very well. I was also given a linisher for free ( I will be buying a good bottle of wine for the gentleman involved however!)
Hopefully tomorrow I will get the backhead finished which will then just leave the throat plate and crown stays. Then the drilling of all the holes and inspection before the assembly can begin.
|
|