|
help!
May 10, 2013 17:15:35 GMT
Post by steamboater on May 10, 2013 17:15:35 GMT
I have been trying to complete a three and a half inch size boiler, although I was reasonably sure I had stopped a leak in the front nest of tubes and also a leak in the foundation ring they are both still leaking. It is pretty frustrating trying to pin down the exact point , I thought that the leak in the front was coming from where the tubes were joined.I acquired the boiler part constructed and bought a large amount of low melt silver solder, any suggestion would be most gratefully be received
|
|
chiptim
Part of the e-furniture
Posts: 270
|
help!
May 10, 2013 18:32:28 GMT
Post by chiptim on May 10, 2013 18:32:28 GMT
Hi Steamboater,
You need to pinpoint the leaks. Try putting some air in it and brushing some soapy water around the leak. It'll soon show up as bubbles. There's different methods for fixing leaks no doubt but one method I have successfully used (not on a join between boiler plate and tube though) is to drill into the leak and fit a piece of scrap copper round. Leave the end long and it will catch in the flame and help take the heat into the joint for soldering. You can trim the excess off after.
If its a join where a tube end protrudes through the plate I think your only option is to re-flow the whole plate although you can attempt just part but on a boiler this small its likely to be most of it in reality.
Remember if both tubeplates are soldered then you need to heat the tubes and barrel slowly and evenly - the same for cooling else distortion may cause more leaks. Remember the barrel will cool quicker than any tubes so you may need to cover it to retain the heat so the whole boiler cools very slowly.
I use a small burner on the spot to re-flow and a separate (larger) burner to raise the temp of the whole boiler evenly. Try to get the whole boiler nearly to brazing temperature and the small flame on the spot to re-flow will raise just that area to brazing temperature.
If you can locate the leaks a photo may help?
Someone else got any suggestions?
Regards Tim
|
|
|
help!
May 10, 2013 18:48:41 GMT
Post by steamboater on May 10, 2013 18:48:41 GMT
Thanks very much for the advice, I will try the air and soapy water and let you know what happens (eventually) as for a photo well I am a bit ashamed of the messy soldering so need to tidy that as well. I spent a whole day last week with a multi tool cleaning the foundation ring and nest of tubes, also two whole bottles (12 kg * by two!!!) of propane!
|
|
chiptim
Part of the e-furniture
Posts: 270
|
help!
May 11, 2013 6:57:16 GMT
Post by chiptim on May 11, 2013 6:57:16 GMT
Yes I understand but remember we won't judge the mess of excess solder on the outside its the solder through the joint that we can't see that matters.
Is the solder you have cadmium bearing or cad-free? If it's cad-free you need to get more heat from when it just starts to melt compared to cad-free because it has a wider temperature range between solid and fully molten compared to cad bearing. This is important if trying to apply the solder to the same side as the heat like on the last tubeplate when the boilers almost complete.
Tim
|
|
|
help!
May 11, 2013 9:43:32 GMT
Post by Shawki Shlemon on May 11, 2013 9:43:32 GMT
All above advice is very good , from my experience the biggest problem is CLEANING .If there is carbon in the joint then solder will NOT flow no matter what heat you apply .On a recent boiler ( Simplex ) , when soldering the stays I melted a few joints of tubes in the fire box side , I only found out when testing  . I cleaned it properly , plenty of flux , using cad bearing solder (pieces placed in required areas ) I heated with large gas torch and let the solder run . NO MORE LEAKS  .I didn't bother heating all the boiler .I hope this helps.
|
|
|
help!
May 11, 2013 15:08:10 GMT
Post by steamboater on May 11, 2013 15:08:10 GMT
everything is a help and much appreciated, hoping to make some plugs on Sunday, hopefully to get some air in the next two days Once again my thanks
|
|
chiptim
Part of the e-furniture
Posts: 270
|
help!
May 17, 2013 18:51:57 GMT
Post by chiptim on May 17, 2013 18:51:57 GMT
hi Steamboater, here's a foundation ring I sealed using this method. I think I tapped the plug 6BA in this instance having failed to seal the leak simply re-flowing in the normal manner without the plug. 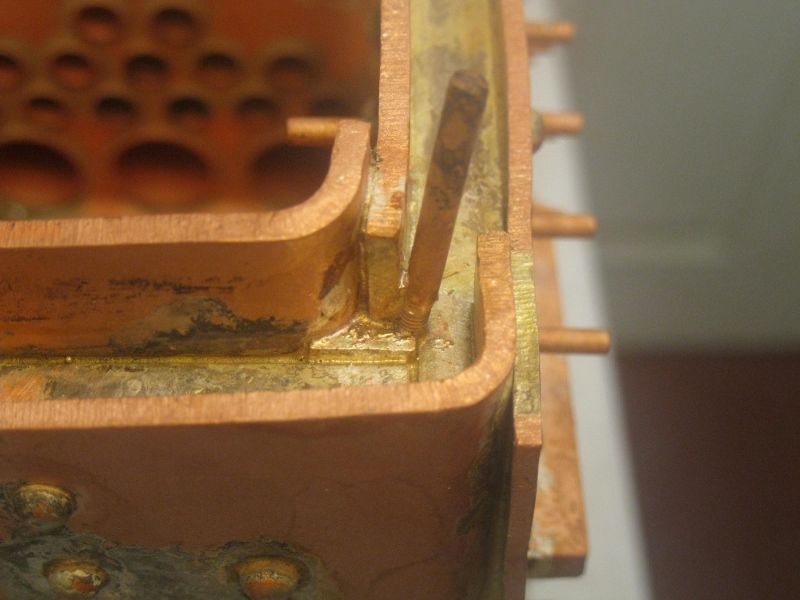 Tim
|
|
|
help!
May 17, 2013 21:19:06 GMT
Post by doubletop on May 17, 2013 21:19:06 GMT
Two tips I was given when in a similar situation chasing leaks and creating more as I went on. Caulking small leaks with soft solder is acceptable as they don't impact the structural integrity of the boiler. My local ME supplier recommended Bridgit solder www.harrisproductsgroup.com/en/Products/Alloys/Soldering/Lead-Free-Solders/Bridgit.aspxI was told, or read somewhere that you can silver solder over it so it isn't a problem if rework is required. If there are slightly larger leaks sprinkle copper turnings/dust around the joint along with some short lengths of silver solder. The copper dust helps the solder fill the larger gaps. Opinions sort on both these methods as I'm pretty new to all this myselfOf course these are remedial steps after everything else has been done. Even Martin Evans acknowledged in his boilers book "Even the best of us will have a leak in a newly built boiler" Pete
|
|
|
help!
May 24, 2013 16:49:04 GMT
Post by steamboater on May 24, 2013 16:49:04 GMT
dont know what happened, I thought I had put a reply and my thanks to those who replied? But here it is again, I think I have got somewhere, but last Monday was a nightmare to get the boiler hot in this very bad weather, cold and showery
|
|
|
help!
Jun 3, 2013 12:18:34 GMT
Post by Nigel Bennett on Jun 3, 2013 12:18:34 GMT
Who is going to inspect this boiler and issue a Boiler Test Certificate if you intend steaming the boiler in public? I suggest that you contact your Boiler Inspector and ask if he is prepared to accept the boiler for testing. A boiler of unknown provenance, which has not been inspected during its construction, and - without in any way casting aspersions in your direction - not exhibiting good workmanship may well be turned down, even though it may pass a pressure test. A Boiler Inspector is entitled to refuse to test any boiler he is not happy with!
|
|
|
help!
Jun 9, 2013 18:07:45 GMT
Post by steamboater on Jun 9, 2013 18:07:45 GMT
Thanks for the input, but I do not envisage running the locomotive in public. I will be very happy to get it in steam and probably only run it the once? I have heated the boiler up a number of times and am still experiencing leaks in the seams (firebox body on the outside to main barrel) I was pleased to finish the tube end successfully, but I am now considering if I should seal theses irritating leaks with soft sold4er caulking. Any suggestions would be very much appreciated!!
|
|
jma1009
Elder Statesman
 
Posts: 5,917
|
help!
Jun 16, 2013 10:56:02 GMT
Post by jma1009 on Jun 16, 2013 10:56:02 GMT
i hate to be the bringer of bad tidings, but if your barrel to outer firebox joint is leaking then that's a pretty serious structural fault and frankly i'd scrap the boiler. if such a major joint has poor penetration and is badly done i am not very optimistic and myself wouldnt want to go anywhere near such a boiler in steam whether privately in your garden or anywhere else! soft solder caulking (with say comsol) doesnt add strength...you are simply covering over the 'cracks' so to speak in both senses.
cheers, julian
|
|
|
help!
Jun 17, 2013 16:05:47 GMT
Post by steamboater on Jun 17, 2013 16:05:47 GMT
Thanks for your suggestion Julian, but since my last post I have "re-worked" the boiler and after cleaning all the joints that were causing problems i.e. leaky, I can now say that the leaks have ceased. I intend to give it a hydraulic test before any usage
|
|