|
Post by suctionhose on Aug 19, 2014 11:56:41 GMT
The main luxury Hydraulics has is oil - lots of it!
This is a very interesting subject and a technical improvement on traditional soft packing for pistons would be a break through.
I would readily chuck my oring glands in the bin and use PTFE with a scarfed joint. Haven't had to though.
Where I have played with PTFE I've found with temperature it expands a lot and becomes very soft, making it difficult to hold mechanically or use where dimensional stability matters.
Truth is I've abandoned it now and removed it from any place I was using it.
One fellow here swears by it for piston valve rings but then I can imagine them squelching in the out of the ports in the liners without problems if the edges are not sharp.
Please keep posting your findings. Love to know the solution.
|
|
jma1009
Elder Statesman
 
Posts: 5,922
|
Post by jma1009 on Aug 19, 2014 12:26:00 GMT
can i just add a small but important clarification - ordinary silicon 'O' rings ARE NOT Viton 'O' rings! confusingly the Blackgates catalogue lists 'Viton' 'O' rings as 'silicon' 'O' rings! Viton 'O' rings are now generally black whereas when i was playing about with these things 20 years ago they were white.
if doug was supplied with Viton 'O' rings then they ought to be ok. however if he was supplied with ordinary silicon 'O' rings they will not be!
Viton 'O' rings are considerably more expensive!
i have seen Viton 'O' rings to be stated to be used up to 200 degrees C, and even 250 degrees C, but not for prolonged periods at these higher temperatures.
the late Jim Ewins carried out extensive tests on his famous 5"g 0-6-2T loco and which had radiant superheater elements fitted and the maximum temperature of the cylinders was recorded at 146 degrees C.
my advice to doug would be to pick out what remains of the squashed 'O' rings on his piston rods with a bent scriber and fit graphite packing soaked in steam oil and made into coils that dont overlap and are just long enough when wrapped round the piston rod tightly. no need to remove the crossheads from the piston rods. tighten the glands up hard as you can then slacken off 1/2 or 1/4 turn. make sure the gland studs have locknuts fitted.
i would be very dubious about using vesconite as a packing medium in steam locomotive pistons. whilst it is stated by the manufacturers to be used in gland 'neck' rings' this is quite different to what we can achieve in miniature. i dont know of any miniature steam loco that has proper 'neck rings' as per fullsize.
cheers, julian
|
|
|
Post by Roger on Aug 19, 2014 12:44:17 GMT
Is that right about the gap? I thought the idea was to make the OD almost the size of the bore with the gap fully closed so that the gap was as small as possible. I've never made anything like that so I'm only guessing. I do like the idea of two rings though.
|
|
|
Post by Deleted on Aug 19, 2014 13:10:49 GMT
Just to muddy the water even more, I wonder how piston rings made of Vesconite would perform. I think the material is rigid enough to make them in a similar fashion to cast iron ones, ie on a compressed after slitting an holding them on a mandrel for finish turning. Again, they could have a Silicon 'O' ring as a backing spring. SPEEDY has pretty long pistons so I guess you could even fit to piston rings in the space so the gaps are not opposite each other. Roger, I don't think Vesconite would stand the temperature. According to the data sheet it has a melting point of only 260°C and is only rated at 100°C continuously. I use two PTFE rings with the gaps at 180° and they've never given any trouble. I've have actually still got the original silicon O rings in the piston rod and valve rod glands on Helen and they've never given any trouble but they probably get an easier life than a piston ring. I've used packing for glands made from a tube of PTFE which has worked well. Also PTFE tape twisted into a string and used like graphite packing. That also works well. I did try measuring the cylinder temperature on Helen when I first ran her on a rolling road. I used a digital thermometer reading to 150°C and it went off the scale! I've got one of these fancy infrared ones now but have never repeated the experiment. John
|
|
|
Post by Roger on Aug 19, 2014 13:38:00 GMT
Hi John, You're probably right about the Vesconite then. Do you use a Silicone 'O' ring under the PTFE rings? Did you split them, close the gap and turn the OD to get the gap virtually closed? How do you keep the rings at 180 degrees to each other?
|
|
dfh
Hi-poster

Posts: 197
|
Post by dfh on Aug 19, 2014 14:40:58 GMT
Hi John, You're probably right about the Vesconite then. Do you use a Silicone 'O' ring under the PTFE rings? Did you split them, close the gap and turn the OD to get the gap virtually closed? How do you keep the rings at 180 degrees to each other? Hydraulic cylinder seals that use an inner O ring with some type of PTFE or similar material outer seal, the outer seal is not split, suitable tools are used to stretch the seal over the piston. The bearing/guide material on the piston are split at an angle and just wrap around the piston. Video at this link shows fitting seals, of that type. www.youtube.com/watch?v=qqZ8LV21tQkThe point being could you use the same approach with PTFE for cylinder seals, the seal would have to be not to thick and would need a bit of work to find the correct groove depth for the O ring to give the correct amount of pressure on the back of the seal. The O ring would give a seal between the piston and the seal so any leak past would soley be between cylinder bore and the seals outer face.
|
|
|
Post by Roger on Aug 19, 2014 16:58:01 GMT
Hi John, You're probably right about the Vesconite then. Do you use a Silicone 'O' ring under the PTFE rings? Did you split them, close the gap and turn the OD to get the gap virtually closed? How do you keep the rings at 180 degrees to each other? Hydraulic cylinder seals that use an inner O ring with some type of PTFE or similar material outer seal, the outer seal is not split, suitable tools are used to stretch the seal over the piston. The bearing/guide material on the piston are split at an angle and just wrap around the piston. Video at this link shows fitting seals, of that type. www.youtube.com/watch?v=qqZ8LV21tQkThe point being could you use the same approach with PTFE for cylinder seals, the seal would have to be not to thick and would need a bit of work to find the correct groove depth for the O ring to give the correct amount of pressure on the back of the seal. The O ring would give a seal between the piston and the seal so any leak past would soley be between cylinder bore and the seals outer face. Thanks, that's a useful video. I'm guessing that it would help if the PTFE seal was heated up and pushed on while it's warm? It's certainly possible to make a flexible tool like they show from Nylon and slit it with a saw. I suppose the other alternative is to make the PTFE a thick one but split like a proper piston ring. I'm also guessing that it would leak too much if just one were used.
|
|
pondok
Part of the e-furniture
My 5" gauge SAR class 15F
Posts: 359
|
Post by pondok on Aug 19, 2014 19:17:48 GMT
Many ways to skin the proverbial cat, and it's often enjoyable to complicate things for the fun of it, but on the off chance my experience with PTFE is helpful, after installing both piston rings and valve rings on 4 locos so far, diameters from 1" to 2.75", I can confirm they have all been a total success with complete seal under steam with the simplest of arrangements, which are: > no o-ring underneath - not needed, the annular expansion takes care of pressure outwards under steam. "some" clearance underneath , 1 mm or whatever > one single ring, no need for 180 deg arrangement, one ring with one cut seals 100% > no sign of any cheese grater effect over the (sharp) ports, even after years of use -didn't happen > no need to machine clearance to account for later heat expansion, a snug push fit is all that's needed, so you can still use the valve setting method Julian mentions.
..fit and forget.
as Ross says, its not strong, but as its nicely contained between piston groove and cylinder wall, it doesn't have to be. Others may have had a different experience.
|
|
|
Post by Roger on Aug 19, 2014 19:58:08 GMT
Can you just clarify the comment 'one ring with one cut seals 100%'? Do you mean that it's a split ring, that's how I read that comment. If that's the case, how did you go about making them? What about the thickness of the ring for say a 1-1/2" bore? If that's a split ring, is that a scarf joint? If you've cut a joint, did you cut that first and then close the gap and hold it on a mandrel before machining the OD?
|
|
|
Post by Doug on Aug 20, 2014 5:34:50 GMT
Can you just clarify the comment 'one ring with one cut seals 100%'? Do you mean that it's a split ring, that's how I read that comment. If that's the case, how did you go about making them? What about the thickness of the ring for say a 1-1/2" bore? If that's a split ring, is that a scarf joint? If you've cut a joint, did you cut that first and then close the gap and hold it on a mandrel before machining the OD? If I read it right then yes one ring, split with a scaf cut turned to size first with od a push fit in bore and 1mm clearance below the ring cut after making one diagonal cut with a stanly blade would do it
|
|
pondok
Part of the e-furniture
My 5" gauge SAR class 15F
Posts: 359
|
Post by pondok on Aug 20, 2014 8:41:53 GMT
yes spot on, in my case I've always used solid valve bobbins and pistons - ie simple groove in solid bronze. Turn the ring to size, firm push fit in the bore, and about some clearance between groove and ring minor diameters, part off for a firm fit in the groove width. As Doug says, cut with a stanley blade. I use a scarf cut but a straight cut would be fine too. I'd avoid a diagonal cut, that would leave quite thin ends. PTFE being weak, I tend to try keep it chunky, but Baggo used it quite thin with great success. For 1.5" bore, you can have it 1/4" thick no problems. Of course, for piston valve bobbins, its best if the rings determine the admission and exhaust events, so I've always turned the metal to have coned cheeks that simply hold the rings and play no part in events. Again, I've always turned up solid bobbins for this - and cut the PTFE rings to slip into the grooves. Easy peasy.
|
|
pondok
Part of the e-furniture
My 5" gauge SAR class 15F
Posts: 359
|
Post by pondok on Aug 20, 2014 8:50:53 GMT
so Roger, just to be clear, no need to cut first then final skim. Turn to final size as solid ring first, then cut afterwards and slip over the groove. A slight chamfer on the leading edge of a piston ring can help it go back into the cylinder, but obviously its best to keep piston valve ring edges as sharp as possible, as they should be determining the timing, so just take a lot of care getting those into the valve bore.
|
|
|
Post by Roger on Aug 20, 2014 9:13:44 GMT
Right, I've finally got it. I must say I like the idea of thicker rings rather than wafer thin ones. One thing does puzzle me though. If there's a slot in the ring, doesn't that always leak? By a scarf cut, I presume you mean that it's not a radial cut from the circle centre but at a slant? If so, what sort of angle are we talking about, presumably not too steep? If solid rings are best for valves, is there a good reason why the piston isn't fitted with them too? It's easy enough to make a piston in two pieces to get them on and off. I hear what you're saying about the retaining pieces of the valve bobbin not taking part in valve events, that makes sense. It certainly sounds like PTFE is the answer though, I'm certainly going to give that a try.
|
|
jma1009
Elder Statesman
 
Posts: 5,922
|
Post by jma1009 on Aug 20, 2014 9:33:25 GMT
the methods used by andy and john(baggo) for piston valves with PTFE are well tried. the downside, as found when the SR Schools class piston valve heads were altered is that the sides of the bobbin encasing the PTFE no longer form the vital dimensions of the valves, and can affect the sharpness of the valve events. this isnt a problem as long as this is borne in mind and the PTFE is made so that it replicates the dimensions and spacing of the solid head bobbins, and the sides of the valve heads are relieved and chamfered accordingly.
cheers, julian
|
|
|
Post by Doug on Aug 20, 2014 10:14:01 GMT
this describes it quite well  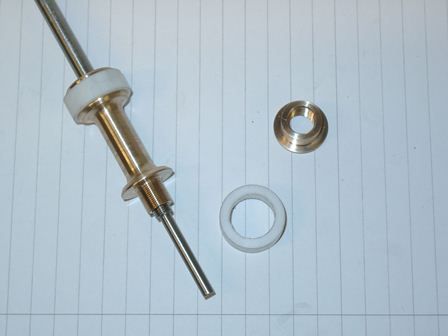
|
|
|
Post by Roger on Aug 20, 2014 10:45:40 GMT
Very good point Julian, the spool is going to have to be that bit longer. Fortunately there's plenty of room on SPEEDY to accommodate that.
|
|
pondok
Part of the e-furniture
My 5" gauge SAR class 15F
Posts: 359
|
Post by pondok on Aug 20, 2014 11:39:14 GMT
"If there's a slot in the ring, doesn't that always leak?" - nope, the cut closes again so it can't leak, material expansion makes it even tighter. "By a scarf cut, I presume you mean that it's not a radial cut from the circle centre but at a slant?" - OK, so scarf cut is not in fact what I do - terminology issue there. I use a step cut but really it matters not a jot how you cut the ring: www.precisionrings.com/images/STEP%20CUT%20GAP.JPG"the methods used by andy and john(baggo) for piston valves with PTFE are well tried. the downside, as found when the SR Schools class piston valve heads were altered is that the sides of the bobbin encasing the PTFE no longer form the vital dimensions of the valves" - sorry I wasn't clear enough in my previous posts, I have always ensured the PTFE ring replaces the bobbin end and determines the valve timing events. The metal supports the rings, and plays no part in timing. "this describes it quite well" - not the method I've always used Doug, mine is simpler, keep the bobbin solid, cut the rings and slip them into the grooves. The split piston method introduces the need for grub screws etc to make sure the end plates don't unscrew. Horses for courses!
|
|
pondok
Part of the e-furniture
My 5" gauge SAR class 15F
Posts: 359
|
Post by pondok on Aug 20, 2014 11:42:52 GMT
"If solid rings are best for valves, is there a good reason why the piston isn't fitted with them too?" - as you'll see from my previous posts, I've never used solid rings for valves either, no need. In theory, one might be worried about the split edge catching on a valve port, which is not an issue on the piston. In practice, its always been fit and forget.
|
|
|
Post by Roger on Aug 20, 2014 12:55:13 GMT
Ok, I think I've finally got there. I can see how a stepped cut can seal where the gap is because the faces can meet. I'm not sure how neat a job I could make of that with a Stanley knife though! I've got a pointy scalpel that might be easier to work with. I like the idea of parting it with a knife though so that you don't lose any material in the process. You make it all sound so simple, it's a wonder anyone does it any other way!
|
|
|
Post by Doug on Aug 20, 2014 15:45:32 GMT
I am going to go with pondoks suggestion I like the idea of fit and forget I have been messing about with this issue for way too long time to put it to bed. I will hold off on further progress on speedy till I have a working solution as well. Time to get shopping again for some PTFE round bar
|
|