shooter
Part of the e-furniture
If it 'aint broke....don't fix it!
Posts: 252
|
Post by shooter on Oct 26, 2014 7:48:10 GMT
superb as always Julian, top job.
|
|
|
Post by Roger on Oct 26, 2014 8:53:47 GMT
Those look superb, this it the sort of detail that really catches the eye.
|
|
jma1009
Elder Statesman
 
Posts: 5,922
|
Post by jma1009 on Oct 26, 2014 22:47:03 GMT
thank you guys for all your kind comments!
eye strain today!
ben, the threads are 4BA left hand and right hand. wilf (uuu) very kindly sent me the 4BA left hand taps and dies required for which i am extremely grateful. i will also use them for the brake rigging adjusters/turnbuckles.
cheers, julian
|
|
|
Post by sncf141r on Oct 26, 2014 22:57:01 GMT
Agree with others - once again, thank you for showing this work; well done, in many senses of the phrase.
John A. Stewart.
|
|
|
Post by Deleted on Oct 27, 2014 18:09:01 GMT
Hi Julian, a very fine paint job, but I wouldn't expect anything less. I have in front of me Martin Evans' book "Model Locomotive Boilers-their design and contruction" which on the front cover shows what I thought is a picture of your locomotive, but no this one shows large pipes coming from the side tanks into the smokebox. Apart from this difference looks similar to yours. Brian --------------- Julian, need I add any more ?? ---- Top Notch stuff !!-----------When researching and designing No.111's boiler I made use of this book ( Chapter 2 especially ) quite a bit, along with the BR Standard full-width designs as well......Looking through that book just now and I wonder what became of Mr E.C.Dearman of Australia and his featured Springbok boiler ??.........My copy says Published in 1969 @ 35/- ( That's thirty five shillings OR £1-15 shillings)---Using the Bank of England inflation calculator ( www.bankofengland.co.uk/education/Pages/resources/inflationtools/calculator/flash/default.aspx )---that's approx. £16.51 in todays money !!....................... Mentioning Boilers and this book might be of interest to you chaps new to this sort of thing}---- www.amazon.co.uk/Maintenance-Locomotive-Boilers-Allan-Garraway/dp/0711027463 ------------------------ and this as well }--------- www.ebay.co.uk/itm/Locomotive-Boiler-Explosions-Hewison-Christian-H-Hardback-Book-/141430334074?pt=Non_Fictio --------------
|
|
jma1009
Elder Statesman
 
Posts: 5,922
|
Post by jma1009 on Nov 4, 2014 21:16:43 GMT
roger was asking how to bend copper tube - well here's how i do mine!  knuckle joints very useful! anyway here's the partly bent radiant superheater elements of stainless to copper bent to fit the smokebox...   only took a few minutes and not worth making a jig! cheers, julian
|
|
|
Post by Roger on Nov 4, 2014 22:25:34 GMT
So how are those copper pipes attached to the stainless ones then Julian? That makes such a neat job of it. Presumably that's one per cylinder and just a combined wet header?
|
|
jma1009
Elder Statesman
 
Posts: 5,922
|
Post by jma1009 on Nov 4, 2014 23:20:20 GMT
hi roger, the hot header will in effect be a 'Y' or 'T' piece above the steam pipe to cylinder. this leaves the ends of the tubes clear for cleaning. Jim Scott has produced an excellent arrangement for his own 5"g terrier. neither are anything like the martin evans design! cheers, julian
|
|
|
Post by Deleted on Nov 5, 2014 8:02:41 GMT
that's nice and neat Julian....I was wondering why use two different materials and what method is used for the returns in the firebox? Is it simply due to copper being easier to bend the tight curves at the smokebox end? Last of all did you use normal SS/flux for joining the stainless to copper or is it something made for the job?
Cheers
Pete
|
|
|
Post by Roger on Nov 5, 2014 8:31:33 GMT
It's super neat, I really like that.
|
|
|
Post by ejparrott on Nov 5, 2014 9:43:23 GMT
Copper is easy to bend and make the connections in the smokebox, but will not tolerate the firebox environment. Using collars to silver solder the copper to the stainless tube gives you the best of both worlds. I recently discovered the club's Scot was fitted with a copper superheater assembly when it was rebuilt...all copper...I wasn't very chuffed....
|
|
|
Post by Jim Scott on Nov 5, 2014 10:49:49 GMT
Re Julians superheater elements . The tubing is 316 ss and the sleeves are bronze. The silver solder used is Argobraze 56 and the flux Tenacity No5. (see www.jm-metaljoining.com/pdfs-products/Argo-braze%2056.pdf) The hot ends are TIG welded in the form of a return bend rather than the usual spearhead. My elements are joined by a scarf joint with the stainless socketed into the copper then soldered as above. A little neater than sleeves. The finished elements have been tested to 200psi, and similar elements in my Maid of Kent have been in use for 60+ hours so far. Ed is correct in his reasoning for the copper tails. It is a very tight bend to reach the wet header and whilst not impossible, would risk having to remake the welded ends if the element was bent incorrectly. Also, I reckon it is less risky assembling and testing the elements first, leaving the relatively easy silver soldering of the wet header till last. Jim S 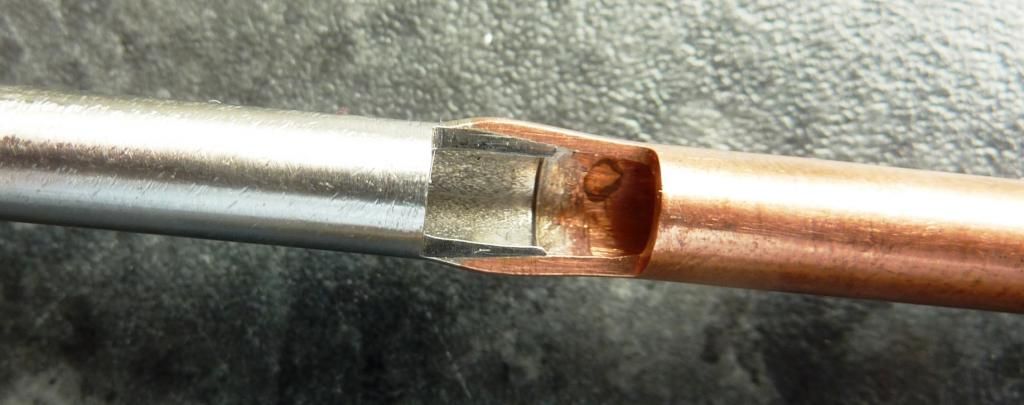 1/4" dia stainless/copper transition joint silver soldered with Argobraze 56 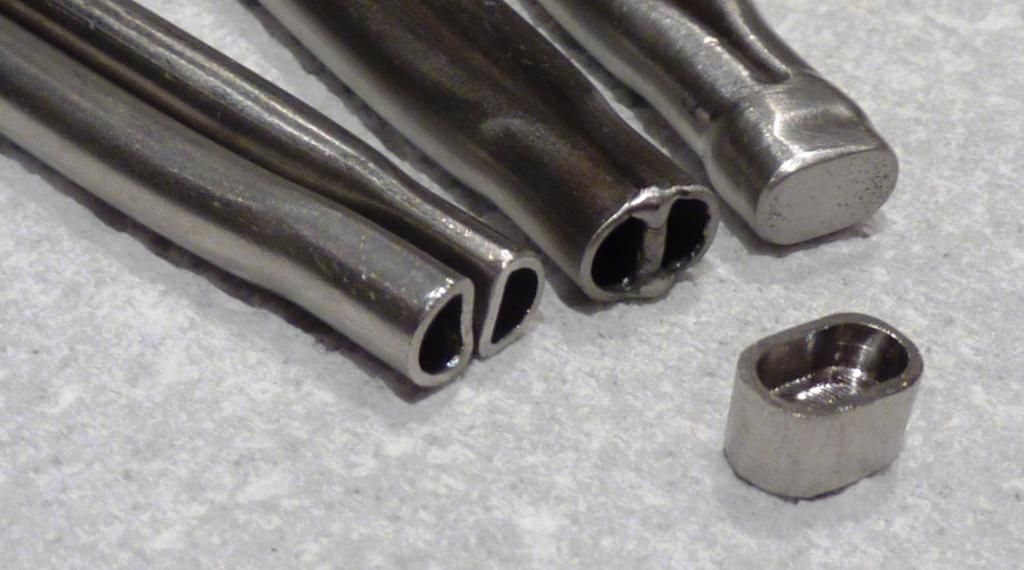 Stainless steel return bends, TIG welded.
|
|
|
Post by Roger on Nov 5, 2014 10:57:22 GMT
Those connections between the dissimilar metals look very neat and slender, is there some kind of collar involved there then because I can't see one? I'd be tempted to put a shallow taper on the end of the copper pipe and a tapered hole in the stainless part so the joint was long and the full diameter of the copper pipe could be retained at the end of the joint. It also throws up another question.... why not make the Stainless part to be just the last third of the length where it needs to be protected but switch to copper where it isn't so you can get the benefit of the better conductivity? Stainless is a rubbish conductor of heat compared to copper. Ah, that answers the question.... our posts overlapped. What's the benefit of the separate return bend over the other split, formed and Tig welded version like this? 20140609_212439 by rogerfroud, on Flickr
|
|
|
Post by Deleted on Nov 5, 2014 11:24:17 GMT
Thanks Jim.. that's very informative... i like this approach used by you and Julian....in a few years time if I can still remember this i'll do the same...  cheers Pete
|
|
jma1009
Elder Statesman
 
Posts: 5,922
|
Post by jma1009 on Nov 5, 2014 12:27:18 GMT
i stated awhile back that Jim Scott had very kindly sent me a set of superheater elements he had made of stainless radiant type. i cant weld at all, and cant claim any credit for the elements which are entirely Jim's excellent work.
to catch up on a few queries, as jim says the copper 'tails' are there to provide a material that is easier to bend. there would be no point making just the last 3rd of the elements out of stainless as due to jim ewins' research very little heat transfer takes place in the flues other than in the first few inches of a miniature boiler. because they are of radiant type (ie extending into the full distance of the inner firebox) they have to be made of stainless otherwise they will burn out in next to no time. even the non-radiant type have a limited life on our miniature locos with copper elements and copper return bends sifbronzed. the annual accumulation test doesnt do them much good either!
notwithstanding the use of stainless, the radiant type provide a much higher superheat temperature. this results in a considerable saving of water and coal plus makes the loco more lively and more responsive to shorter cut offs if you have a decent valve gear fitted and if same is properly set. neither LBSC or don young used or described the radiant type, but they have been around in miniature locos since the days of 'uncle' jim crebbin of SMEE fame for over a hundred years.
cheers, julian
|
|
|
Post by Roger on Nov 5, 2014 13:16:23 GMT
That's really interesting Julian, because that sheds more light on why concentric types might not perform as well. If there's very little hear transferred along the flue length, you don't want the inner and outer tubes conducting heat to each other because that's only going to cool down the superheated steam created from the radiant end. I'd love to see how much difference it makes if that's done. Anyway, you've answered my questions and that all makes good sense.
|
|
|
Post by Jim Scott on Nov 5, 2014 23:25:05 GMT
.........What's the benefit of the separate return bend over the other split, formed and Tig welded version like this? Hi Roger Spear type return bends are relatively easy to weld in sizes above ¼”dia and wall thickness greater than 20 gauge. At or below this size and at 22 gauge (better for heat transfer) this becomes more tricky, requiring a great deal more care to prevent burn through. However, the main difficulty is in ensuring that the weld is sound where the two tubes lie together as this is a very poor joint configuration for TIG welding. In my arrangement the tube ends are formed into a ‘D’ shape using a press tool, the flat faces placed together and the joint fused, using filler wire only at the start and finish of the weld. The integrity of this 'soon to be hidden' weld can readily be checked before continuing. The endcap is machined (or it could be pressed from sheet) and after lightly truing the tube ends presents a straightforward, accessible butt joint ideal for TIG welding. With regards to the ‘poor’ heat conductivity of stainless, I feel this is a bit of a red herring when considering that the heat path is only 0.028” (22 gauge) and subject to direct radiant heat from a very hot fire. I suspect that the whole of the exposed elements will very quickly reach a high and pretty well uniform temperature irrespective of the amount of steam flow. Jim Ewins data may well show whether this is the case. Also, I would be surprised to see laminar flow conditions prevailing immediately following a 180 degree reversal at a spearhead... My 5” G Maid of Kent has thermocouples fitted, one in the steam pipe immediately above the steam chest, and during fairly light load conditions it usual to see 270 to 300 degrees C at this point. Over 400 degrees C was noted on one occasion when the blower was inadvertently left on, resulting in some scaling of the steam pipework in the smokebox. I still wonder just how much superheat is desirable. Having a new and effective superheater on the MoK, the most noticeable effect was the better than 50% reduction in water consumption. Can’t quantify any reduction in coal consumption but from the driving viewpoint, the engine is definitely more lively above 300 C. Interesting to note that I don't seem to have had any lubrication issues at these temperatures. Jim S
|
|
|
Post by Roger on Nov 6, 2014 8:34:27 GMT
Thanks Jim, I don't much about welding but I can see that it looks to be easier to make them with the cap. Do you use 316L for all of the tubes and the cap? The poor conductivity comment was aimed at the part of the tube that's in the flue. That's why I wondered if you could have only a short length of stainless, say the last third. I can understand that if the temperature of the steam coming back from the radiant portion is high, it's unlikely to get any hotter as it travels back down the flue. I suppose it's even possible that it gets colder.
As for the amount of superheat being desirable, I suppose it's a sliding scale of benefit where the greatest improvement is in the region where any condensation takes place anywhere in the circuit except the exhaust where I guess it would be of benefit. If the steam starts to condense at any point then you aren't getting the benefit of it having been steam so that's wasteful. I would suggest that anything above that point is going to show a further improvement in efficiency but to a lesser extent. 300C seems a very long way from wet steam, do you know what the temperature of that is at working pressure? Without doubt there is more energy in ever higher temperatures of superheated steam so it's logical that you should find it more lively. I suppose this is all down to proportions really. Somewhere between a wet steam boiler and one with a huge array or superheaters (almost a flash boiler) I guess there's a sweet spot to get the most energy from a given grate area into steam at the highest possible temperature.
|
|
|
Post by Jim Scott on Nov 6, 2014 21:40:57 GMT
Hi Roger.
I don't want to clog up Julians thread with superheater issues as these are being discussed at length on a concurrent thread, but to answer your last post directly:
I didn't say my method was easier but in small diameters and with thin walls I found it gave more certain results. I think I'm right in saying that most stainless sold today as 316 is carbon controlled (ie 316L = low carbon) to improve weld metallurgy. Similarly, stainless steel welding wire contains stabilising elements to the same end.
The 'hot' leg of the element may be well above the flue gas temperature along most of its length so I would think that some loss of temperature will occur but this may be minimal. Nevertheless, keeping the transition joint as far away from the hot end as possible seems a good idea to me.
Surely there must be a temperature drop between the radiantly heated return bends and the hot header/steam pipe connected to a steam chest? Conduction, radiation to a lower smokebox temperature?
The Maid of Kent has a working pressure of 80psig which from steam tables equates to 162 degrees C. The thermocouple located about 2" into the boiler steam pipe reads this accurately if allowed time to settle (its not actually in the boiler steam space). Thus 300 C at the steam chest indicates 138 degrees C (280 F) of superheat. As Julian has noted elsewhere, these figures are in line with those obtained by Jim Ewins test results with radiant return bend superheaters. For interest I have posted on the spearhead v concentric thread a copy of Jim's tabulated results as published (I think) in ME. I'm sure Julian will have the full article somewhere.
I suspect maintaining adequate lubrication will limit the max useable superheat and this wil in turn depend on other factors such as material selection etc. MoK seems quite comfortable with up to 350 degrees C, and this with gunmetal cylinders.
Jim S
|
|
|
Post by Roger on Nov 6, 2014 22:28:15 GMT
Thanks for all that Jim. I'm not at all sure you're right about 316 and 316L. I've had some experience of using 316 in an HHO cell and the Iron gets ripped out from it leaving just a brittle shell. That doesn't happen with 316L. Maybe I was just unlucky. I agree that there must me a loss of temperature from the radiantly heated end to the smokebox. It makes you wonder if insulation would help there but it's not very practical to implement.
|
|