|
Post by vulcanbomber on Mar 25, 2015 21:58:48 GMT
Anything above about 300mm diameter we use length bars.. These, as there name suggests are a predetermined length, about half inch over what needs measuring and then measuring the gap with slips, very easy and reliable and old skool as well. We use stick mic's in bores, again can be made different sizes. The glass company also has a Faro arm... A sort of portable CMM machine.
|
|
|
Post by ejparrott on Mar 26, 2015 9:17:12 GMT
Glass company David? You having fun with your phone again??!!
We've got length bars that can reach to about 3000mm, if we combine the metric and imperial sets, but the biggest problem then is sag, so we have to be careful to support the bars across the hole in the ring. Bore mikes are the same, again we can reach 3000mm, but they usually get cable-tied to a piece of thick legged aluminium angle to stop the bending, and even that's not enough sometimes. We have got a couple of circumference tapes as well but they aren't big enough for the work I do.
All great fun!
|
|
|
Post by Deleted on Mar 26, 2015 9:25:25 GMT
Thanks for both replies .
|
|
jem
Elder Statesman
 
Posts: 1,075
|
Post by jem on Mar 26, 2015 18:11:29 GMT
Its great to see these interesting work pieces, more please,
best wishes
Jem
|
|
|
Post by vulcanbomber on Mar 26, 2015 21:53:54 GMT
Glass company David? You having fun with your phone again??!! We've got length bars that can reach to about 3000mm, if we combine the metric and imperial sets, but the biggest problem then is sag, so we have to be careful to support the bars across the hole in the ring. Bore mikes are the same, again we can reach 3000mm, but they usually get cable-tied to a piece of thick legged aluminium angle to stop the bending, and even that's not enough sometimes. We have got a couple of circumference tapes as well but they aren't big enough for the work I do. All great fun! yeah I am, thing is, on that occasion I didn't even put a word there and deleted it Once!!
|
|
|
Post by ejparrott on Mar 27, 2015 18:28:45 GMT
So, my week has consisted of a couple of hundred of these little blighters..... 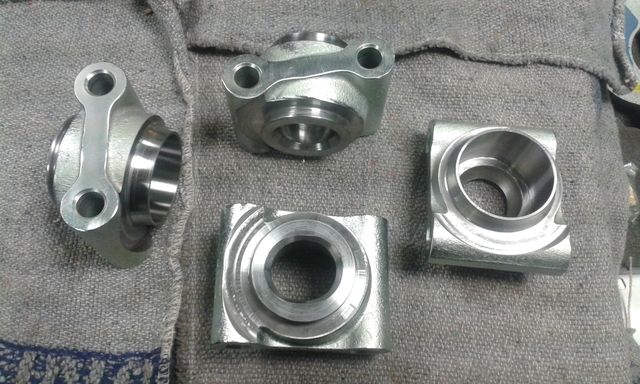 Boredom has now set in... Allegedly they are for Ferrari, but I'm sceptical myself, happy to be proved wrong though. They are a socket ball joint for a 30mm ball, very similar to a Track Rod End found on a Land Rover and probably a whole load of other cars I don't work on. You see the sphere in the bottom of the right hand piece, and apparently the ball joint is dropped through and then a machine rolls in the raised lip you can see on the left and right pieces. The other side of the joint which is the side I've been doing you can see in the top and bottom pieces. This is just a clearance for the joint, and the groove around is for the gaitor. It's a mostly milled job and frankly done badly, but it was a rush job and we used supplied tooling and fixtures. I've got a form tool to make the groove which is a disaster - 4.75mm wide, with a groove to form a lip that's about 1.5mm wide, and there's also 4 rads.... All in all far too much tip loading, and the tip is just plain and flat carbide with no hint of any kind of cutting edge or rake or anything. IT's bouncing like buggery! Simple plunge in to size and job done..... Hmm.... The millers are doing the socket side, they've got 2 expensive form tools, a not cheap 30degree tool, and a special step drill. All of it could have been turned with no special tooling at all, and would have been a much better job. Cycle time is 10minutes for the millers, 7.5 for me.
|
|
|
Post by simplyloco on Mar 27, 2015 18:39:16 GMT
So, my week has consisted of a couple of hundred of these little blighters..... SNIP Hmm.... The millers are doing the socket side, they've got 2 expensive form tools, a not cheap 30degree tool, and a special step drill. All of it could have been turned with no special tooling at all, and would have been a much better job. Cycle time is 10minutes for the millers, 7.5 for me. I know where you are coming from there. I used to receive layout sheets and special tooling from Rotaprint for capstan work, and I would take one look at it, shake my head in disbelief, and tool it up myself. We would then do it in half the quoted time and make more dosh! John
|
|
isc
Statesman

Posts: 708
|
Post by isc on Mar 28, 2015 8:26:19 GMT
Ferrari do build tractors, and other agricultural machinery. isc
|
|
|
Post by ejparrott on Mar 28, 2015 8:40:45 GMT
Do they? Hmm..that may explain a few things...
|
|
|
Post by Deleted on Mar 28, 2015 9:08:52 GMT
In the days before CNC was common there were several different types of turner to be found in the large factories with many machines that did most industrial mass production work . One of these types was the production turner . This was a fully skilled turner that spent all of his time making large quantities of identical components on a standard manual lathe . The production runs were usually at least several hundred components and could sometimes be many thousands spread over months of work .
They sometimes made simple parts but their forte was making more complex parts with relatively tight tolerances .
These turners - often on piece work - knew every method and trick to make quality components but at the same time reduce part manufacturing times to absolute minimum .
Always allowed a few scrappers to practice on they would develop their own procedure for the job and often adapt it further as they progressed through the production run .
They all had their pet methods , personal special tools and and usually a collection of old machine parts and DIY jigs which got bolted on to standard lathe .
Saw a few of these people in action in my earlier years . Fascinating to watch and to talk to .
|
|
|
Post by simplyloco on Mar 28, 2015 9:32:03 GMT
I forgot to mention that once I'd used a few scrappers and got the setup running, I'd pass it on to someone else who didn't get bored as quickly as I did! Well, I was the foreman after all...
|
|
|
Post by ejparrott on Mar 28, 2015 9:53:57 GMT
That's a problem I have, days and days of doing the same thing for hours on end is not my forte!
|
|
|
Post by ejparrott on Nov 4, 2015 12:48:22 GMT
12 Rings that David and I have been working. Nasty job first off for me parting them off from blanks on the big lathe, fully CNC and parted off under auto powered feed 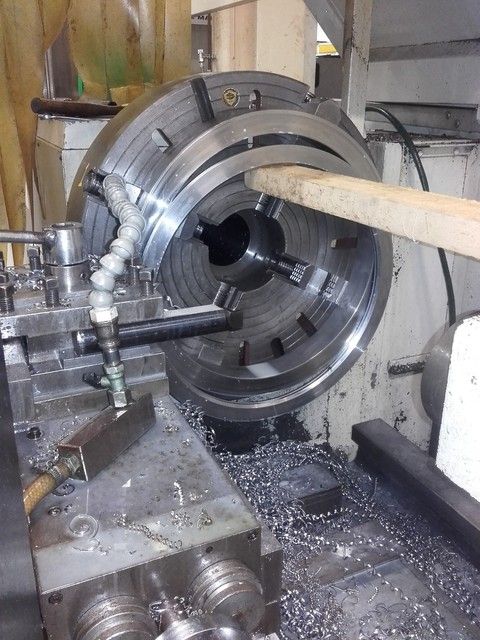 Then on to the borer for finishing to thickness, and 8 little V grooves 1/32" deep 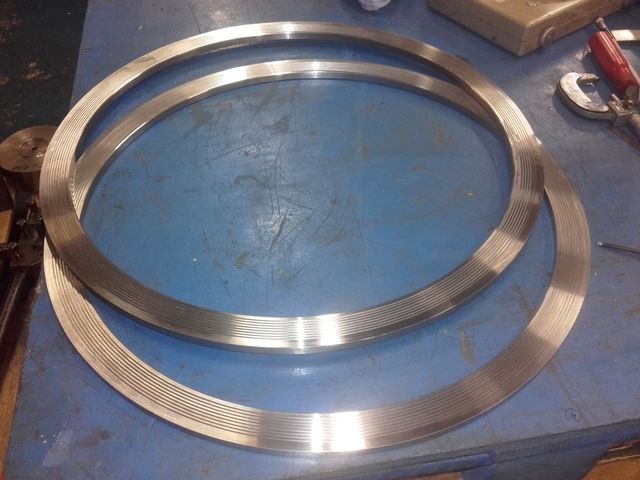 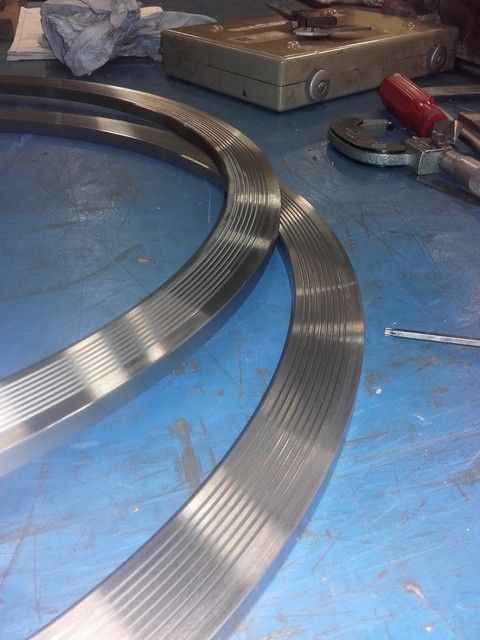 Nothing else exciting at the moment, not much at all as it happens.
|
|
|
Post by vulcanbomber on Nov 4, 2015 18:31:01 GMT
Plus and minus 1 thou on the thickness and due to the worn nature of the Pallet Changer means the tables use most of the limit up just by holding the job down.... An easy job they said...
|
|
|
Post by ejparrott on Nov 6, 2015 9:33:32 GMT
This one's not interesting per say, but it is a challenge and is giving me grief. Job was quoted on a fag packet drawing. Sounds simple enough. Customer has a 3M tube, they want it cutting in half and new bolt flanges welding on so they can bolt it back together. Flanges all have mating spigots that are 5mm long and 420mm diameter. Sounds simple enough yeah? Proper drawing turns up - get this....requirement for 0.04mm concentric between the existing end spigot and the new one.... End faces parallel to 0.04mm.... Ok, fine, I'll give it a go but that's a big ask on a job like this, do-able, but time consuming. ...... Then the first four arrived.....I was not happy!!!!!!! These are old parts that have been in service already. They've been shot blast to get rid of rust, but the corrosion pockets on them are significant. Also, there's an .04mm limit of the diameter of the spigots, but the ones I measured last night were a minimum of 0.1 below bottom limit already! So how do I even go about setting these up? Well, to set the old flange up true one would have expected for the top diameter of the flange to be turned so that I could clock it in the 4-jaw... No... Rough flame-cut, which judging by the chamfer that's machined on it is not even round, and certainly not true. The spigot is only 5mm long so I can't get my clock down the back of it as it's a 1/4" shaft, and even if I could, it's too far down the face to reach anyway! I've ended up telling our customer they need to supply us with a plate that I can bore to fit the spigots on the tubes, with a row of bolts to hold the job to it and drive it. I've bored the plate in the machine, and not removed it to fit it to the tube. It's bigger than the flange too so I can use that face which I've also machined to measure the length against. To get it ready for working on the other end, I obviously haven't got a centre being a pipe, so I use a 4-jaw chuck which has got a plate in it's middle with a centre in the back of that. Tailstock goes up the centre, use the four jaws to clock it true.....being a pipe - true ISH! Once it's setup I'll then skim a portion on all 4 tubes that's the same diameter and true, then I can drop them all on the steady one after the other and away we go....he says..... 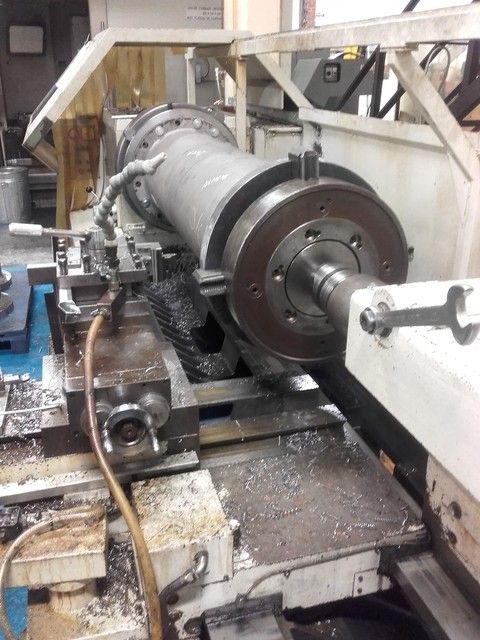
|
|
|
Post by ejparrott on Nov 6, 2015 9:39:06 GMT
Another little interesting job, not one I'm doing it's a milling job, bit too big really for our Bridgeport clone when you consider there's 8 of them and some pretty tricky measuring, but our man's on the case! 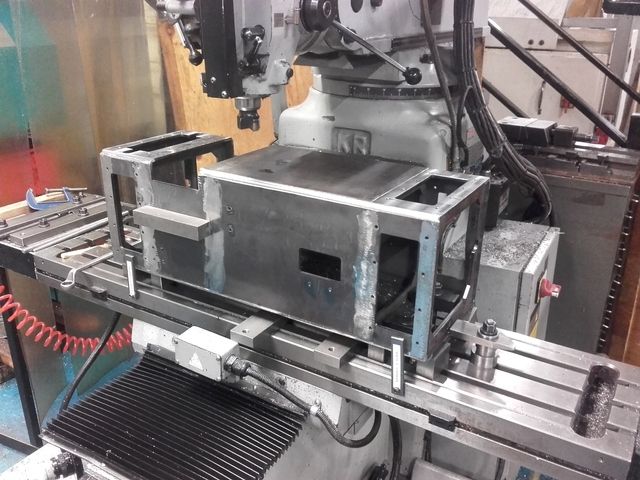 I haven't the foggiest what they're for, it's a job for ITP group. What was interesting was the method of construction..... 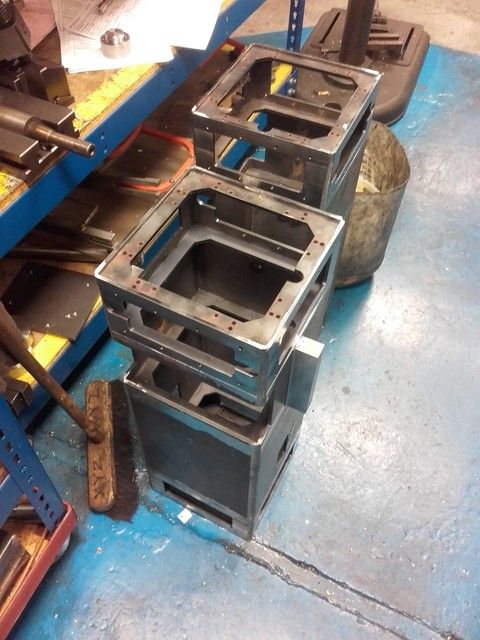 You can just see on the top inner plate of the further one - 3 stripes each each slightly discoloured? Yes, Malcolm could almost have been on the case! They're laser cut slot and tab and then welded, exactly the same way countless ME's are producing various stretchers for engines and my angles for the valance and bunkers! The box section is built up from 4 flat plates clamped around the four inner plates, the corners welded along the entire length and then the slots and tabs welded up too.
|
|
|
Post by ejparrott on Nov 21, 2015 10:30:17 GMT
This is proving to be a really nasty job....  All stainless, with a tube running the length and three bits welded to it. The tolerances on runout are ridiculous, and of course it's bent with welding. Turns out it bends if you sneeze at it too. Was having no end of trouble with it last week. The only good thing to come out of it was the machine got a cross-slide rebuild in the process, after we discovered that we'd suddenly got massive amounts of backlash, when the rear bearing carrier all but fell off!
|
|
|
Post by ejparrott on Nov 21, 2015 13:22:53 GMT
Thanks Steve, it's nice to know people are interested in what we do. Trouble with weekly updates, some of our jobs are on the machine for several weeks - I think the record is Dave's at 12 weeks!
|
|
|
Post by ejparrott on Nov 21, 2015 13:27:46 GMT
An update on this one - Customers scrapped them. The Fab shop told them they'd be better off starting from new rather than trying to shorten existing parts and fitting new ends, customer decided they knew better without actually checking up on the parts. Once I'd pointed out that the existing details were so far out of tolerance, things started to change slightly, once we understood exactly what they were trying to achieve, things started to change again. Customer doesn't like our steady bands, but we've got no choice but to do that if they want to achieve what's on their drawing, which they obviously hadn't appreciated or understood and they're now concerned about the wall thickness. The fab shop has suggested welding bands around the tubes which I can turn which then doesn't affect the tube. We'll see where we go with it, but by not listening to the experts at the start, they've wasted a lot of money. There are a number of sets of these around that apparently all need doing, so hopefully they'll listen to the fab shop now, and do the job the right way.
|
|
|
Post by fostergp6nhp on Nov 21, 2015 13:38:20 GMT
For the steady bands how about rings cut in 2 put in place and welded at the joint so the contraction of the weld makes the band a shrink fit, skim to true, use, then cut thro the weld with a cutting disk on the grinder when the machining is finished. Transfer the band to the next workpiece and repeat.
|
|