|
Post by ejparrott on Feb 4, 2014 10:20:12 GMT
I keep mentioning things that I do at work, and I thought folks might be interested in seeing some of what I get up to. I've just finished a jack body on the big lathe, that's been interesting - massively out of balance, boring a 180mm hole with a 560mm long boring bar, and to machine the flange I've been out to 1020mm diameter, heavy intermittent cut too... 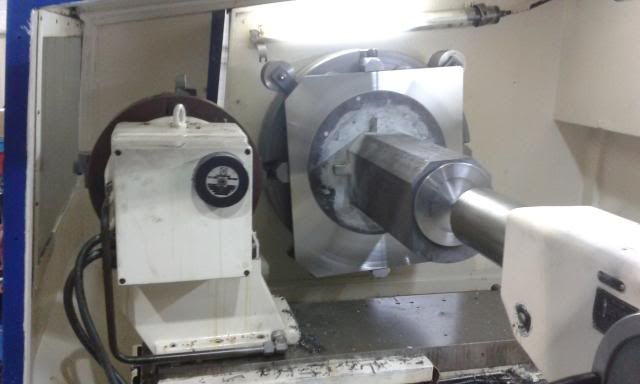 My previous job was a 3030 diameter ring in Weldox 1100...just about the worst material I think I've ever had to machine...its moving all over the place....  And then for something completely different, a little fitting job I did in between....the trip bolt sits on a 90degree cone, and the pair has to be fitted to achieve a distance of 0.25" + .003, then kept as a matched pair...this was a job for the manual colchester... 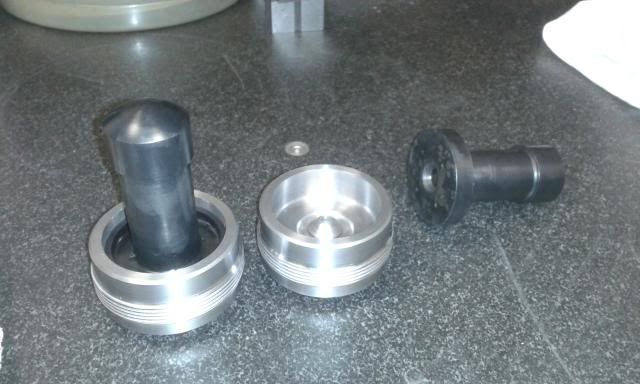
|
|
|
Post by Deleted on Feb 4, 2014 18:01:19 GMT
very nice Ed... I'm curios ...the large disc have you jury rigged a table for this to be cut on or does your machine handle this size on it's own? very nice..  Pete
|
|
|
Post by ejparrott on Feb 4, 2014 20:04:29 GMT
The rotary table on the Elgamill is 1800 square, quite big but shy for this job, so we've used outriggers of 3" x 2" steel to support a ring of 1.5" steel plates as a false surface for it. We used the same outriggers to support it on the table of my vertical borer, the table of which is 2440mm diameter, and the hole in the middle of the ring is 2120mm diameter. The Elgamill is capable of some truly massive pieces of work. If you look closely at the photo, you can see the floor in front of the machine is cast iron T-slotted floor plates. The machine has enough travel to machine a face something like 8m long, from a point 1m above floor level to 3.5m above floor level - in other words 2.5m of vertical travel but it can't get the spindle down to the floor - and could drill a hole in to that face about a meter deep. Wait 'til you see what I've got on the borer now and next.... 
|
|
|
Post by Deleted on Feb 4, 2014 21:10:08 GMT
wow.. .no I hadn't noticed the T slots.....that's an impressive piece of kit Ed...I love the versatility of it....
|
|
|
Post by vulcanbomber on Feb 4, 2014 21:14:40 GMT
Erm Ed, weldox 1100 is much much nicer than this Stellite i'm playing with at the minute. For them that dont know i'm ed's partner in crime at work (non of this pulling rank Ed!!!!) And for them that dont know Stellite, i'm playing with a piece of it around 560mm Diameter, its rough turned at 15 meters a minute, at 1.5mm deep and 0.1mm a Rev, after 1 pass an insert edge is worn out.
|
|
|
Post by ejparrott on Feb 5, 2014 13:28:18 GMT
Not overly exciting this piece, that's still to come, but non the less, an iron casting 1300mm in diameter and 500mm high. Running at a speedy 16rpm, I'm removing 3mm of material every cut, and advancing 0.5mm/rev......I'll have black snot for a month.... 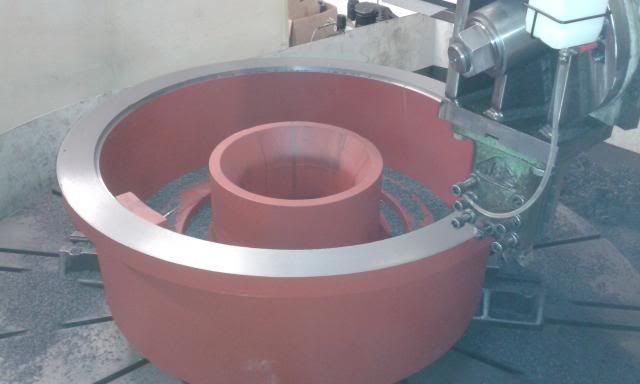
|
|
|
Post by ejparrott on Feb 12, 2014 7:10:35 GMT
Finished that casting..now on to the next one...slightly more tricky to set up this one...patternmaker really screwed up and put all the machining allowance for this casting on to the other one.... 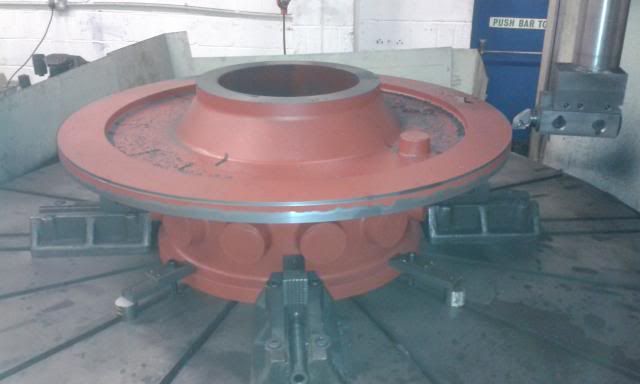
|
|
|
Post by ejparrott on Jun 5, 2014 10:05:30 GMT
Steam raising blower for a Duchess or Merchant anyone? 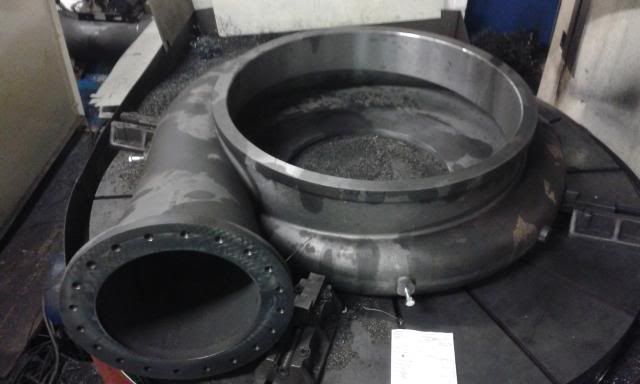 My current rush job...nightmare.... 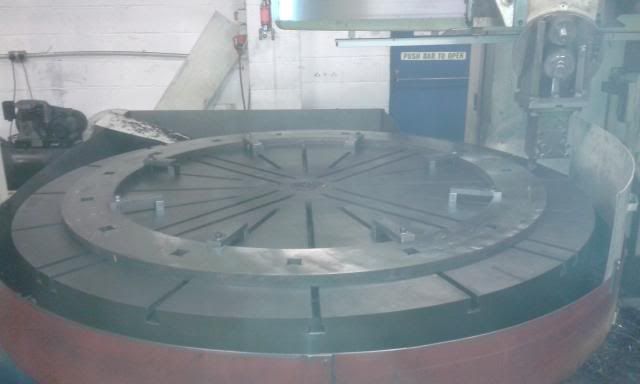 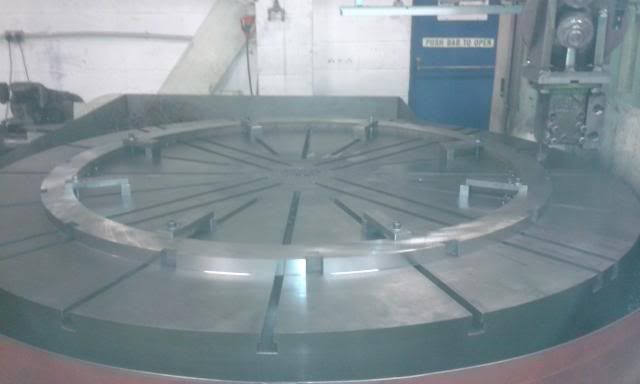 Mega urgent job, of course, been kicking around for a few weeks now. Word is the customer's already had these made....in China...they're scrap.... Flamecut good quality mild steel plate that's been tub ground to thickness, and no stress relieveing, so they're going banana shape as soon as I take the skin off the bore and diameter. The slotted one is knocking seven shades of poop out of the machine. These go off and get fabricated into an assembly which we should be seeing back in a weeks time, i'll try and remember to take some photos.
|
|
|
Post by ejparrott on Jun 26, 2014 9:48:14 GMT
The last two plates I machined on the borer have now been back to the customer for assembly and fabrication, and they're now back with us for some further machining. Too big for the crane over my borer to handle now so they're being 'turned' on the rotary table of the elgamill You can see the first plate on top here with the core bars poking through the square holes... 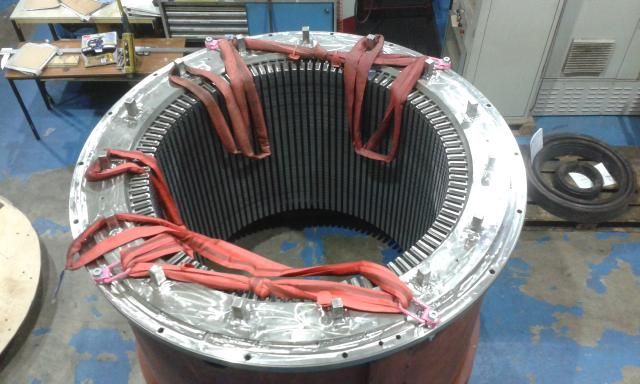 and then the second plate I did where the square holes were incomplete on the outer edge... 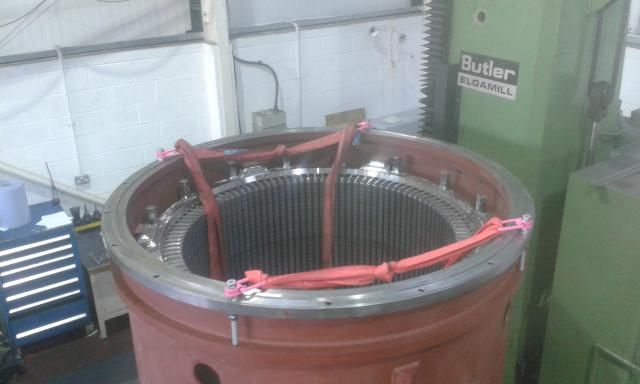 9 metric tons all up weight
|
|
|
Post by ejparrott on Sept 11, 2014 10:52:53 GMT
Not massively interesting, but quite chuffed with last nights efforts. Hidurely-5, copper alloy, horrible sticky stuff. 1/32" rad groove, 1/32" deep, 4 TPI up a .6875" bore.....bit twitchy, came out quite good in the end though. 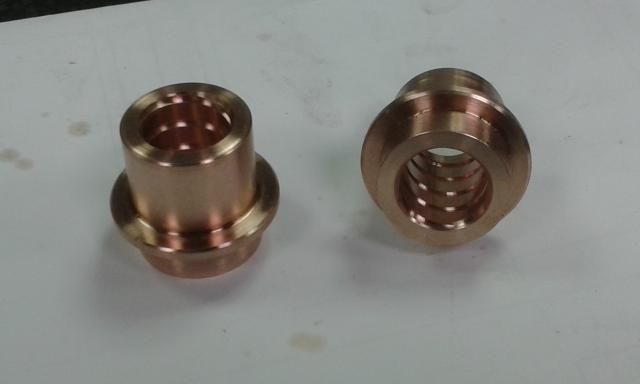 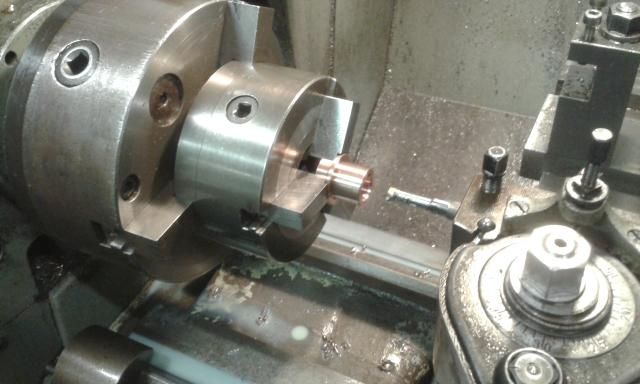
|
|
|
Post by chester on Sept 11, 2014 16:54:01 GMT
Nice work Ed always good to see parts being manufactured more please.In the distant past used to work a 36" webster & bennet and a pre-op capstan 4.
|
|
|
Post by ejparrott on Oct 21, 2014 9:04:45 GMT
Just a bit of little shaft work....centering 550mm of bar without a steady...yes I did leave the crane round it... 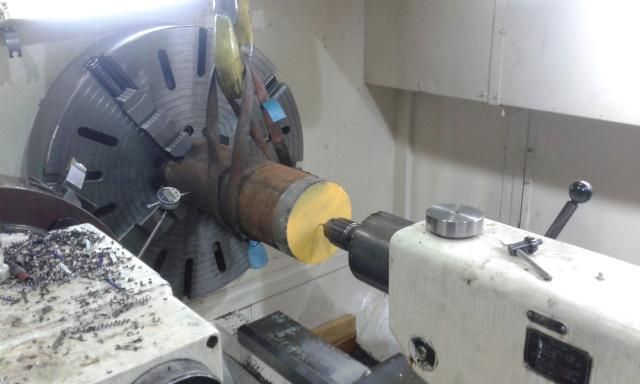 The joys of black bar...anything but round...decidedly ellipse where it's collapsed under it's own weight... 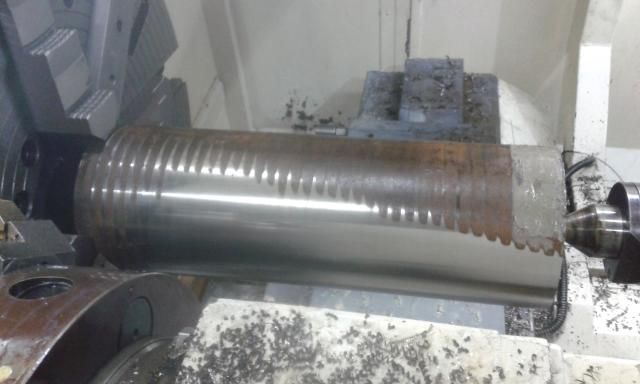 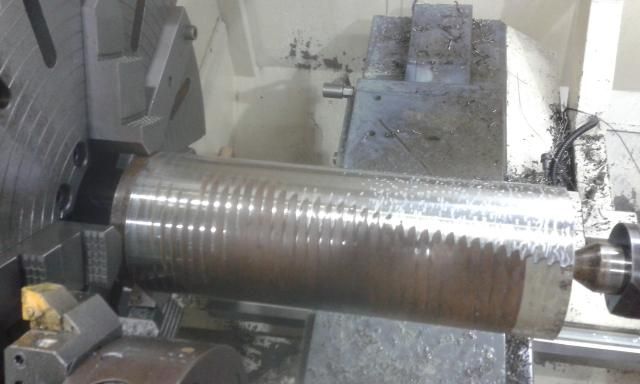
|
|
|
Post by ejparrott on Oct 25, 2014 9:37:17 GMT
I've been back on the small machines back end of this week....Hitachi Super HiCell 250... 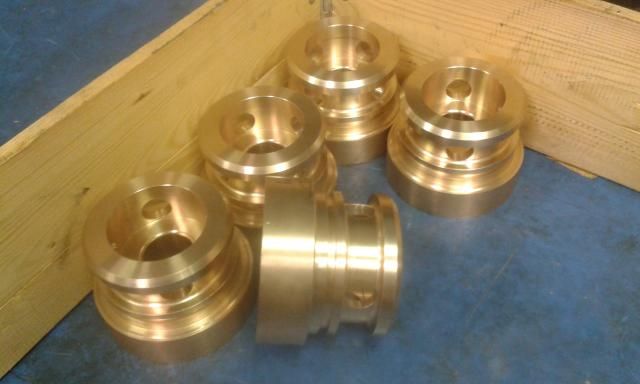 Unfortunately most of them are scrap...centri-spun castings that are full of porosity and not acceptable to the customer. Catch 22 though, we have to prove the material is rubbish for the supplier to replace it...yes we'll get the material back for free, but I've spent 17 hours machining these, a lot of it overtime, and that we won't get back. 32 minutes to turn bore and drill these, still the second end to do which I estimate will be about 16-20mins each
|
|
Midland
Elder Statesman
 
Posts: 1,875
|
Post by Midland on Oct 30, 2014 19:42:20 GMT
Fascinating stuff Ed. Used to watch our people in the machine sh0ps and they made it look so easy. Then tried it in minature and found out how not easy it is!!!! Those buffer bits will arrive one day. I keep a head on my desk to keep it upper most in one's mind! David
|
|
|
Post by ejparrott on Jan 10, 2015 15:27:20 GMT
Oversize turning to the max....literally just got this piece to swing in the Colchester... 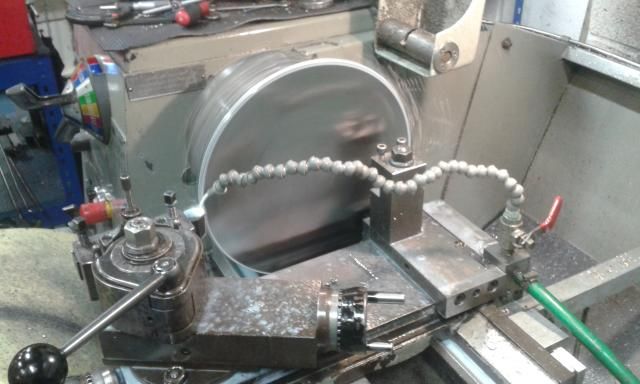 17-4 stainless, A Condition, 90rpm to turn the outside of this....was quite chuffed I got it to fit!
|
|
|
Post by Rob on Jan 17, 2015 12:39:36 GMT
Always enjoy seeing pictures/vids like this - Keep 'em coming Ed!
|
|
|
Post by ejparrott on Jan 17, 2015 15:31:06 GMT
I've got a lovely nasty shaft on the machine at the moment, well an ali test piece for it anyway...wait till you see that....
|
|
|
Post by ejparrott on Feb 4, 2015 12:01:25 GMT
Last week was great fun with this little shaft...80mm black bar that was bent in two places, had the devils own job getting it setup so it would machine... 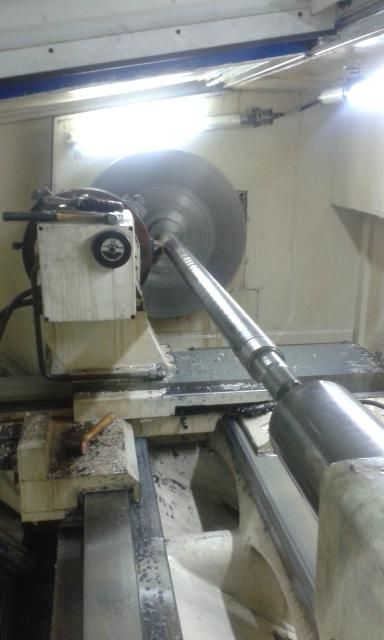 And just to prove it's not all big stuff I do! 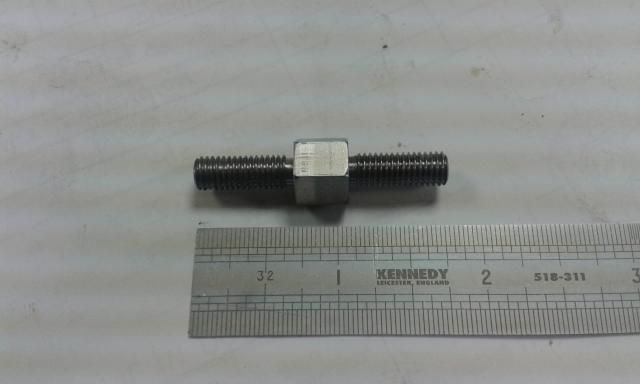 1/4" BSF LH and RH....literally screwcutting a thou at a time. LH came out ok, starting in an undercut so I could get the spindle speed up...RH wasn't so good, had to use the front toolpost for that, the rear toolpost requires internal inserts and we hadn't got any. 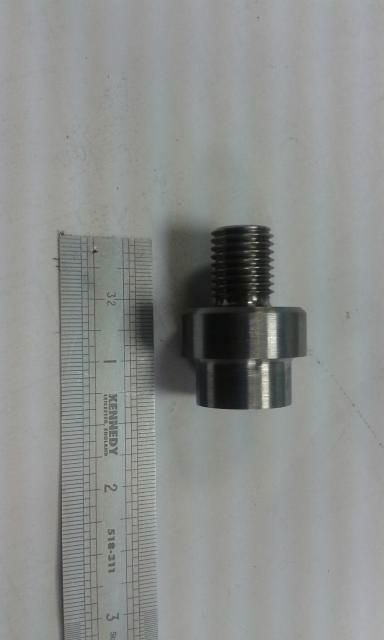 This was a bit nicer, 1/2" BSF on this one, and internal inserts for the rear toolpost to cut the thread
|
|
|
Post by ejparrott on Feb 10, 2015 11:25:43 GMT
Just to keep me on my toes last night....I'll be glad to get back to the big stuff.... 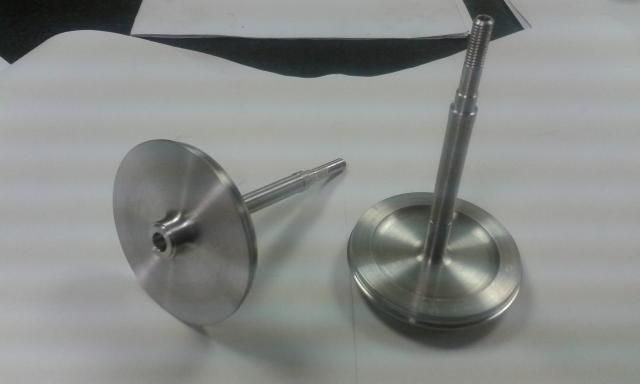 Started life as 5083 Aluminium bar 80mm diameter...that's an M6 thread on the end of there.... 3 diameters all true to each other with a 9 micron limit on the diameter...I was not enjoying it!!
|
|
|
Post by Deleted on Mar 25, 2015 20:26:43 GMT
Hi Ed ,
This is a general interest question :
How do you get on with measuring such large diameter workpieces ?
Where I worked originally large diameter engine casings were machined all day long and I know that even the highly skilled turners there had fun and games trying to get an accurate measurement sometimes .
An engine casing is usually a few feet diameter , thin wall and with a flange each end . When not bolted to anything else it flexible to the extent of several thou .
MichaelW
|
|