|
Post by joanlluch on Mar 17, 2015 6:37:15 GMT
I give up, guys. I intent to help to someone who asked something and I just get replies of too basic stuff. Pete, BTW, it is not "there" it's "their". Basic grammar. What childish behaviour. Joan rule no1. If you're going to correct someone on their grammar try to ensure your own is 100% first. Language barrier or not. And secondly why the bitchy behaviour?There was absolutely no call for your last remark whatsoever. Tim. I was expecting this. Remember that I speak four languages and English is just the fourth. I can post in perfect Catalan if you wish.
|
|
|
Post by Deleted on Mar 17, 2015 6:43:12 GMT
Pete, BTW, it is not "there" it's "their". Basic grammar. Trolling
|
|
tim
E-xcellent poster
 
Posts: 236
|
Post by tim on Mar 17, 2015 6:57:33 GMT
What childish behaviour. Joan rule no1. If you're going to correct someone on their grammar try to ensure your own is 100% first. Language barrier or not. And secondly why the bitchy behaviour?There was absolutely no call for your last remark whatsoever. Tim. I was expecting this. Remember that I speak four languages and English is just the fourth. I can post in perfect Catalan if you wish. Post in what ever language you like but go and take a dump on your own thread not someone else's.
|
|
|
Post by springcrocus on Mar 17, 2015 7:18:05 GMT
Come along, gentlemen, please behave. Joan, please be patient, this is a build diary so things get recorded as they happen. There is no point speculating what will happen next, just wait for the next chapter. You dont start reading a novel, jump to near the end to discover "whodunnit" then come back and continue reading where you left off. It destroys the resulting pleasure of why you picked up the book in the first place. And yes, there is another way of fixing the cylinders to the frame which I shall document at the correct time.  However, please continue posting as you feel appropriate, your insights can be useful for myself and others. All I ask any of you is that you dont belabour a diversion to the point were we all lose sight of the original objective.  Steve
|
|
|
Post by springcrocus on Mar 17, 2015 7:26:31 GMT
To ensure that the frames pull up true and square during assembly, there are quite a few bits that all have to be the same size. On Britannia there is the front buffer beam, the bogie stretcher, the long top stretcher, the pony frame stretcher, two frame stays and of course the horn stretchers. Because I used 3mm plate for the frames I need to keep the inside dimension between them at 3.395", ideally plus or minus sod all. A couple of thou shouldn't be too bad, though. I had planned to make the front buffer beam next but then realised I would need something to accurately set the space between the steel angles used to fix the beam to the frames so decided to make the two frame stays next. These are available as a casting but I chose to make mine from mild steel bar. Then I spotted an old sash window weight in my scrap box so that was used instead. I also decided to make a couple of spacer pieces to help with frame assembly so the first job was to cut off four billets. These were just cleaned up in the lathe and the ends faced to finish length.  After that it was just a case of milling away all the waste and getting the general shape. Nothing here is important other than the length and squareness.  Final part of the job was to mark out the four holes at each end then drill and tap 6BA.   A little tip for those of you just starting out in model engineering. Get yourself a set of spiral point taps in the common sizes that you are planning to use the most. They are much stronger than hand taps and they are self-aligning so you can tap most of your holes freehand and be confident that they are square to the job.  The only drawback is that they push the swarf ahead of themselves so care is needed when tapping blind holes. Thanks for looking in. Steve
|
|
|
Post by simplyloco on Mar 17, 2015 7:42:26 GMT
SNIP Pete, BTW, it is not "there" it's "their". Basic grammar. WTF?  ?
|
|
|
Post by Deleted on Mar 17, 2015 7:42:59 GMT
I give up, guys. I intent to help to someone who asked something and I just get replies of too basic stuff. Pete, BTW, it is not "there" it's "their". Basic grammar. jesus...i give up......yes Joan I used the wrong word...my fault i should have proof read what i wrote.....it happens......I'll get over it even if you can't....I fail to see how anything that I wrote warranted your reply....believe me when I say that I shall not reply to anything you may ask again. Sorry Steve for being in part responsible for upsetting the flow of your thread...my apologies sir. Pete
|
|
pault
Elder Statesman
 
Posts: 1,500
|
Post by pault on Mar 17, 2015 9:13:01 GMT
for blind holes you could always use spiral flute taps, the swarf is pushed out of the hole rather than into it.
|
|
Tony K
Elder Statesman
 
Posts: 1,574
|
Post by Tony K on Mar 17, 2015 9:41:33 GMT
Springcrocus (Steve) - something a little more light-hearted. The Golden syrup tin used to have a slogan "Out of the strong came forth sweetness" - perhaps it still does but the calories have got me!  So, I think you deserve better than the present demeanor of this thread and a little encouragement. Under the bench I have these bronze castings for Britannia axleboxes which are surplus to requirements. I have checked them against the Perrier drawings...  To encourage progress, you can have them for the cost of postage. If you would like them, please send me a PM with an address. No, this is not a scam.
|
|
Midland
Elder Statesman
 
Posts: 1,875
|
Post by Midland on Mar 17, 2015 10:07:28 GMT
Remember that I speak four languages and English is just the fourth. I can post in perfect Catalan if you wish. That would be preferred. David
|
|
|
Post by Jim on Mar 17, 2015 10:28:30 GMT
You're doing some very nice work there Steve and nice to know that Britannia will be shedded at Stratford along with Boadicea  Jim
|
|
gwr7800
Part of the e-furniture
Member of Portsmouth mes
Posts: 388
|
Post by gwr7800 on Mar 17, 2015 12:35:50 GMT
This is a really a good build diary let's not spoil this as well with bickering please! Keep up the good work regards a die hard GWR fan!! Regards Chris
|
|
|
Post by springcrocus on Mar 17, 2015 15:54:21 GMT
Thank you all, gentlemen, for your kind words and encouragement and I do mean ALL of you.  Please be assured that I will continue this build diary regardless of any diversions we may encounter along the way. I know that some of this stuff is quite simple for most of you but I hope by describing what I did to get this far may encourage others to undertake their own projects. I do not claim that my way is the right way or the best way but it's how I did it and please feel free to offer better or different ways of achieving the same result. That is how we all learn and become better craftsmen and I don't use the word lightly for craftsmen is what you/we all are at one level or other. As I said in my first post, I am actually much further along than this but I have my build notes and I have many duplicate parts (I originally planned to build two side-by-side) so I am able to re-create the original set-ups without too much hassle. The only difference now is that I don't have access to the larger machinery that I had when I started. For instance, some bits were made entirely on the Bridgeport VMC460 CNC mill so I will probably gloss over making those bits. I don't half miss that machine now! So for the next couple of months I shall be playing catch-up by posting the old stuff every couple of days, and any new work I do I will record for posting at the right time. And the reason I am doing this build diary at all is because I, personally, have taken much inspiration from those of you who care to share your work and experiences on here and from ALL the other build logs on here. Just because I'm building Britannia doesn't mean I don't want to read about Speedy or Juliet or Stepney etc, I read just about everything that's posted and enjoy every minute of it. Anyway, enough waffle, time to make some swarf... Steve P.S. Tony, a pm is on it's way.
|
|
|
Post by springcrocus on Mar 17, 2015 22:03:33 GMT
The next item I made was the main top stretcher. This is fabricated from a piece of 16 swg zinc-plated mild steel, chopped slightly undersize, that I scrounged from the guy with the guillotine. The other bits are the two pieces of brass angle that affix to the frames and support the top plate. The first job I did was to cut the 3/8 x 3/8" x 1/16" brass angles to length and then mark out, drill and tap the eight 6BA holes in each. There's also a cutaway in each to clear the bolt holes for the expansion link brackets. These were then bolted to their respective frames and put to one side for a while.  There are eighteen equispaced 1/16" rivet holes on each side of the top plate which were marked out and drilled, and I also marked out the fancy cutaways using tracing paper. I then stitch-drilled them and chiselled out the waste, finishing off the shapes with my dremel and a variety of files.  I clamped the mainframes together with the stays and spacer between so that I could rest the top plate in position and clamp the plate to the angles at each end.I also spotted through one hole each side, about half-way along, with a 1/16" drill in my hand drill and dropped a pair of 1/16" rivets through to help keep everything in place.  Then it was just a case of unbolting the stretcher from the frames and drilling through the rest of the holes, pinning with rivets as I finished each hole. 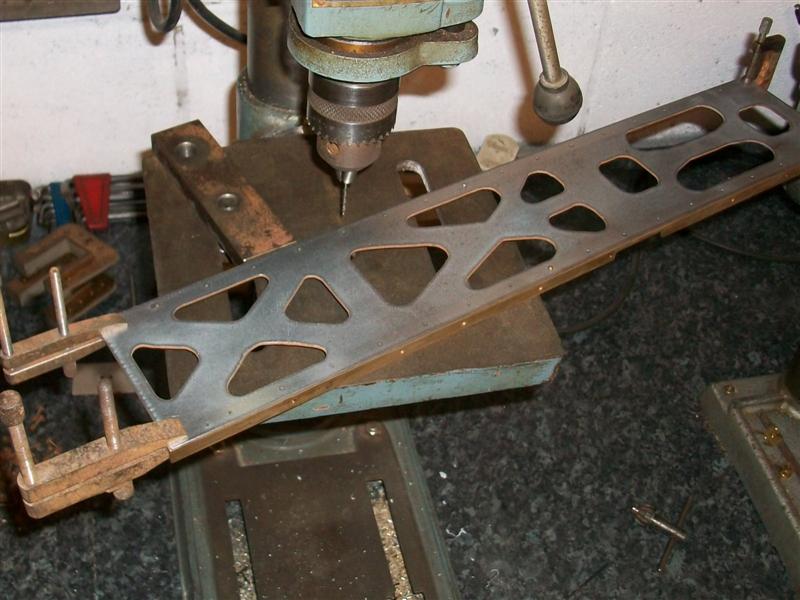 Finally, I rivetted the bits together properly, removed the clamps and drilled and rivetted the final four holes. And here I have the finished top stretcher ready to fit and bang on size.  Thanks for looking in Steve
|
|
jma1009
Elder Statesman
 
Posts: 5,917
|
Post by jma1009 on Mar 17, 2015 22:51:00 GMT
well i must say that steve is doing a very good job, plus teasing us with snippets of earlier work! i will watch how the build has already progressed with considerable interest! keep it going, steve! cheers, julian
|
|
|
Post by springcrocus on Mar 18, 2015 10:05:30 GMT
After re-reading my previous post, I realise that I have left out a couple of lines of text and a photo. Although of no significance to the majority of you, the info may provide a bit of guidance to a less experinced person. My build notes just said "table packing!!!" On freehand drilling the first hole about half way along, I promptly broke the 1/16" drill. The reason for this was that, because of the flimsy nature of the brass angle, the pressure of the cut was deflecting the angle down and away from the drill point. At the moment of breakthrough, it promptly sprang back putting a sudden sideways force on the drill. Result - a much shorter drill. To overcome the problem, I fixed a 5/16" packing piece to the drill table to support the angle and from then on the rest of the drilling continued without mishap. At the time I loctited the packing piece direct to the table (ten seconds with a blowlamp breaks the bond when finished) but I have since made various size packing pieces which bolt through the table using a penny washer below.  Hope this bit of info saves someone else breaking a drill. Steve
|
|
|
Post by peterdanastas on Mar 20, 2015 10:34:44 GMT
Try a product called Devcon in mistake holes . This product is a two part epoxy and then fill the hole and when dry just file off excess peter
|
|
|
Post by springcrocus on Mar 20, 2015 16:15:39 GMT
The next bits I made were the two arms of the pony frame and the associated stretcher. Both of these items were very easy to make but I am including all the parts I've made for completeness. The pony frame arms are just an exercise in marking out followed by lots of arm-ache and some swearing (or was it the other way round?). I started with two plates of 3/16" black steel sawn to 11.1/8" x 3.7/16" and marked out and drilled all the holes while the plates were still rectangular. Next I marked out the profile and and then it was sawing, filing, sawing, filing, sawing.....  At least I managed to get the holes correct where they connect to the mainframes. I don't know why I didn't use the CNC mill to profile these at the time because it would have made light work of them. An ideal job also for laser or waterjet. The pony frame stretcher is just four bits of 1/4" mild steel welded together and milled to be a snug fit between the two lots of frames. I set the width by clamping one of my spacers close to the end of the mainframes. Then the fixing holes were marked out and his time the holes are tapped 2BA so that bolts can be used to pull the whole lot together.  There is also a 3/8" reamed hole at the bottom to take the pony truck pivot pin. The two cutaways at the front are to clear the rear spring hangers on the mainframe.  Thanks for looking in. Steve
|
|
|
Post by joanlluch on Mar 20, 2015 20:20:10 GMT
Hi Steve,
as noted before, the T shaped cuts of the locomotive frames are designed to fit the main axle horns. The frames already cut as shown in this thread have the top sides of the T fully parallel. However, according to the 5" Britannia plans the top of the T is not parallel but it has a trapezoidal shape (inclined sides on the top of the T shape). This is to prevent the main horns from wanting to move out of the frames. Said trapezoidal shape must match the shape of the main horns as seen in the picture just above.
So to my understanding there is something wrong somewhere. Either the frames need more machining, or the main horns are not being done according to the plans.
Please can you clarify this?
Thanks
|
|
|
Post by simplyloco on Mar 20, 2015 20:48:21 GMT
Hi Steve, SNIP So to my understanding there is something wrong somewhere. Either the frames need more machining, or the main horns are not being done according to the plans. Please can you clarify this? Thanks I await Steve's reply to your criticism with great interest.... John
|
|