|
Post by Jim on Jan 1, 2015 4:41:31 GMT
I was interested to see that someone thought it was worth 3D printing and investment casting these, I really don't see the point. It's all about time, Roger, it's all about time! Thanks for those links and photo Alan, very interesting. Was the 21 day cleaning/washout schedule related to the water quality being used or part of a standard routine? Roger if it's Adam you're thinking of with the lovely cast washout plugs. I think he hopes to set up a small model castings business at some stage. Before Allan beats me to it, I should add I'm not giving Adam a free plug here.  Jim
|
|
|
Post by Deleted on Jan 1, 2015 7:16:56 GMT
Hello Jim--------- would that free "Plug" count as a Loss-leader for Adam's embryo business then ??-LoL------------ From what I can gather the washout frequency nowadays is due to H & S directives ( Which I assume have already taken into account the local water quality etc....) ..PS}---That would be 21 OPERATIONAL days, not calendar ones....From coming "On-Shed" with a live fire, to leaving again for revenue service, a full boiler wash-out can take anything up to a week overall to accomplish for a big Pacific type....( That's for a Heritage Railway where you don't expect to see any night workings..)..Remember it must be stone cold before the Fitting Staff can remove the 20 or more plugs, check each one for wear and fitment.... do the actual wash-out....grease and re-place the plugs IN ORIGINAL POSITION ......fill the boiler and re-light the fire............Along with that would be the opportunity to clean out the smokebox ( maybe rod the tubes ??) and oil-up.......So all-in-all not a 5-minute job...
|
|
|
Post by Roger on Jan 1, 2015 8:12:48 GMT
It's all about time, Roger, it's all about time! Thanks for those links and photo Alan, very interesting. Was the 21 day cleaning/washout schedule related to the water quality being used or part of a standard routine? Roger if it's Adam you're thinking of with the lovely cast washout plugs. I think he hopes to set up a small model castings business at some stage. Before Allan beats me to it, I should add I'm not giving Adam a free plug here.  Jim I don't think many builders worry much about how long things take to produce, it's more about the journey than the destination. There's not much work in making the washout plugs however you go about it, they're pretty simple. It's a totally different kettle of fish if you're making vacuum valves. I don't know what the economics are of getting washout plugs built up into a waxed tree for investment casting, but it's not a trivial task. I can see why people want to play with this technology, it's truly amazing, I just don't see the point in using it for that sort of thing. If it's a business decision, I'd love to see a comparison between the casting and CNC machined cost. My guess is they would be cheaper to make by traditional methods. I think it's being done simply because someone fancied doing it, not because it's a real business decision.
|
|
44767
Statesman

Posts: 539
|
Post by 44767 on Jan 1, 2015 9:09:04 GMT
I don't think many builders worry much about how long things take to produce, it's more about the journey than the destination. There's not much work in making the washout plugs however you go about it, they're pretty simple. It's a totally different kettle of fish if you're making vacuum valves. I don't know what the economics are of getting washout plugs built up into a waxed tree for investment casting, but it's not a trivial task. I can see why people want to play with this technology, it's truly amazing, I just don't see the point in using it for that sort of thing. If it's a business decision, I'd love to see a comparison between the casting and CNC machined cost. My guess is they would be cheaper to make by traditional methods. The thing is Adam needed 30 of these. By my estimate, a rapid prototyped tree of 10 washout plugs would cost about $20.00 and a rubber mould made from that would be in the order of $30.00. Each casting (of 10 washout plugs) made using a wax produced from that mould would be about $10.00 so for the 30 needed they would be $80.00 ($2.67 each). My machine is worth $80.00 per hour and there is no way I could make one of these every two minutes, including set up time with material and tooling on top,for a run of only 30. Add to that, Adam now has the ability to make 10 washout plugs for $10.00 without any effort and it is these that he can now offer for sale to help fund his own project and instead of spending his time making these he can use that time on other parts. You can either spend your own time or you can spend your money- your choice. Mike
|
|
|
Post by Roger on Jan 1, 2015 9:49:10 GMT
That's interesting, I'm guessing that there must be some kind of automated plant involved in creating the shells from the waxes to get the price down. Do they cast a whole wax tree from a silicon mould of 30 parts? It's hard to see how they extract the tree if they do. I can see how they can cast lots of individual waxes from separate moulds and then combine them into a tree. If that's how they do it, the hourly rate for hand crafting them onto a tree must be very low. Don't get me wrong, I'm very much in favour of this process, it's just this doesn't seem like a great candidate for it. I reckon I could make one of those on my mill in maybe ten minutes as a 'part on a stick' and then just part it off. That's with my inefficient amateur methods, I think they could be knocked out in no time on any old mill. You don't need a state of the art machine for something mundane like that. The only thing that's going to take any time at all is the square pocket recess, the rest is just cleaning up the outside of a piece of stock bar. Anyway, sorry to have taken over too much time on this thread on that topic. Clearly someone thinks it's worthwhile doing them that way and good luck to them.
|
|
44767
Statesman

Posts: 539
|
Post by 44767 on Jan 1, 2015 10:19:56 GMT
The foundry I get my castings done is a precious metal foundry and so they are used to doing one off rings etc. The cost of a casting depends on the volume it takes up on the tree. They then put everyone's waxes onto a tree and cast all jobs at the same time. The cost of the material is extra. So I can take one casting the size of a ring and it only costs $2.70 plus material (which in silicon bronze is almost negligible but in platinum it's a bit different!) But if I took 100 of these waxes it would cost $270- no economies of scale for me; it's their gain. However my pony truck main casting must virtually fill the whole flask so that one costs about $80 plus material. They would be using any space available to put other waxes on the tree though.
I agree this is a very simple part to make by all manner of ways but quite well illustrates that lost wax casting is not only for very complicated parts. It can be used for extremely simple multiple parts too.
Jim, sorry for discussing this here. We can do it on my class 3 build thread if you like.
|
|
jma1009
Elder Statesman
 
Posts: 5,922
|
Post by jma1009 on Jan 1, 2015 10:37:06 GMT
i would make the washout plugs exactly as jim has done. once the lathe is set up for the 2 parts they can be knocked out in batches on the stops and parted off quite quickly. the silver soldering together will also take very little time. Stepney will need a few on top of the firebox cleading.
cheers, julian
|
|
|
Post by Jim on Jan 1, 2015 11:16:37 GMT
I agree this is a very simple part to make by all manner of ways but quite well illustrates that lost wax casting is not only for very complicated parts. It can be used for extremely simple multiple parts too. Jim, sorry for discussing this here. We can do it on my class 3 build thread if you like. Hi Mike, It's no problem I'm actually interested in the issue of making castings not that I have any thoughts of doing any I hasten to add. It's also interesting too to hear of how others approach the same or very similar task. Jim
|
|
|
Post by Roger on Jan 1, 2015 17:50:22 GMT
The foundry I get my castings done is a precious metal foundry and so they are used to doing one off rings etc. The cost of a casting depends on the volume it takes up on the tree. They then put everyone's waxes onto a tree and cast all jobs at the same time. The cost of the material is extra. So I can take one casting the size of a ring and it only costs $2.70 plus material (which in silicon bronze is almost negligible but in platinum it's a bit different!) But if I took 100 of these waxes it would cost $270- no economies of scale for me; it's their gain. However my pony truck main casting must virtually fill the whole flask so that one costs about $80 plus material. They would be using any space available to put other waxes on the tree though. I agree this is a very simple part to make by all manner of ways but quite well illustrates that lost wax casting is not only for very complicated parts. It can be used for extremely simple multiple parts too. Jim, sorry for discussing this here. We can do it on my class 3 build thread if you like. That sounds like a really handy foundry to have, it's rare to be able to get one offs bundled in with other people's ones to make a batch of anything.
|
|
|
Post by Cro on Jan 1, 2015 22:55:10 GMT
Jim,
Sorry to jump in on your thread, just thought I'd give a quick explanation as to why I did the plugs as castings. I new I needed a large amount and I knew that they were available via our friendly supplier of scale items (no names mentioned) but I was blowing away by the price. I agree they are simple enough to make but at the time I was experimenting with 3D printing and wanted to try something simple and these seemed simple enough and it worked out cheaper to print, make a mold and cast a set for myself than to buy them from previously mentioned supplier (you would be looking at around £76 for 10 from them) - crazy right? So I thought I would have a go and I know a lot of people like buying bits like these so I had a batch made up to help others along. The whole task gave me a better understanding of 3D printing and casting and since, as some have seen, I've been able to progress with some more complex bits! Look forward to next update Jim! Adam
|
|
|
Post by Jim on Jan 3, 2015 11:45:47 GMT
Not much to show for the last few days what with visitors and and family get togethers and a steadily rising thermometer. Apart from making washout plugs I've now made up a trial removable section that covers the long edge of slide out grate and also completes the bottom section of fire box cleading. The removable section also contains two washout plugs which brings the final total to 21. I've fitted one washout plug to see how it looks while the upper row are held in place with blue tack to check the spacing. Jim 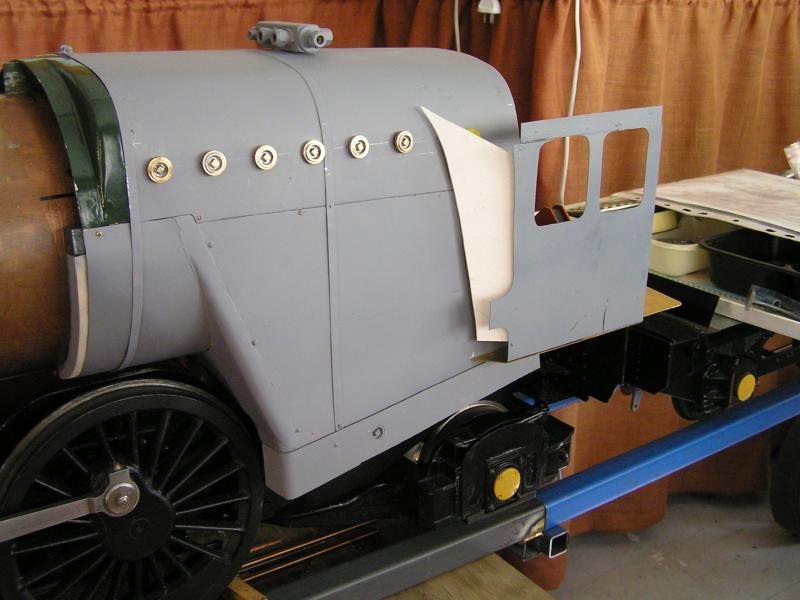
|
|
|
Post by Deleted on Jan 3, 2015 12:33:32 GMT
are there any on the backhead (doorplate) ??
|
|
|
Post by Deleted on Jan 3, 2015 15:17:15 GMT
That is looking very good Jim ... This is going to be a stunner when done.
Cheers
Tom
|
|
|
Post by Deleted on Jan 3, 2015 15:30:04 GMT
lovely work Jim..I'm loving the way the cleading is coming together....looks great
Pete
|
|
|
Post by Deleted on Jan 3, 2015 16:54:50 GMT
Don't make my mistake Jim, remember it's five of one and half a dozen of the other! John
|
|
|
Post by Jim on Jan 3, 2015 18:28:09 GMT
are there any on the backhead (doorplate) ?? Hi Alan, At last count there were 10. I have to confess that I've modified the doorplate somewhat to accommodate water gauges that I can see easily plus I have fitted a hollow stay to take steam forward to the blower which means it won't be exactly as the full size but I'll certainly be including as many plugs as I can. As Julian noted, once you're set up they are quick easy to make, or at least until my mind drifts off task and I create yet another 'waster'  Jim
|
|
|
Post by GWR 101 on Jan 3, 2015 19:08:37 GMT
Looking good Jim as always, I used to hate capstan work when I was an apprentice as it seemed so boring but it's different when it's in a good cause. Regards Paul
|
|
|
Post by Jim on Jan 16, 2015 6:20:04 GMT
Over the last few days I've made up the 22 washout plugs needed and started on the mud hole doors. There's nothing very complex in making these parts the biggest problem is maintaing concentration and remembering where I put the 10 BA tap.  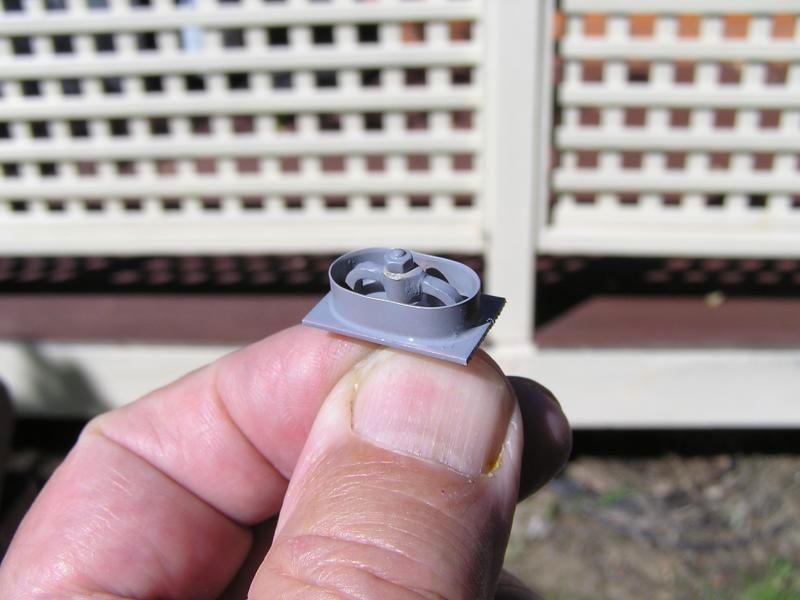 Jim
|
|
|
Post by Roger on Jan 16, 2015 6:49:42 GMT
Wow! That looks absolutely superb Jim, what a cracking job! How did you go about making that, it's so neat?
|
|
44767
Statesman

Posts: 539
|
Post by 44767 on Jan 16, 2015 6:53:37 GMT
Looking good, Jim!
|
|