|
Post by Roger on Jan 24, 2015 12:43:02 GMT
Hi Doug, I agree whit pretty much everything you say really. I think my frustration is that they are hopeless at documenting each element of the system. There are a few tutorials on YouTube and that's about it. Most of the documentation on boards tells you nothing other than the names of the jumpers and pinouts but they never reveal the underlying drive electronics so you have no idea what the driver outputs are capable of. I'm pretty sure my relays don't have that issue on the mill, but I think you're using a parallel interface. Have you used the charge pump? I thought that was supposed to keep everything de-energised during powerup. I think the ESS does that sort of thing internally but there's no documentation to say. I've fitted a proper 24V safety contactor in my system, so E-Stop isn't a polite request, it removes the power from the drive electronics. It's an expensive way to do it, but it's the safest and what you'd have to do in industry. It's frustrating that the machine isn't stiff enough, but at least you can achieve good accuracy with a final finishing cut. Mine's pretty good but it could always be stiffer. I try not to work with the quill hanging out any more than necessary. Fortunately, that neck extension doesn't seem to have any detrimental effect on the rigidity of the machine. Mind you, it's a solid piece of bar, so it's not going to flex much! I didn't bother with a "charge pump" I have used a relay that energises the drives (somehow I have missed the spindle tho) it is a setup that is also borrowed from industry but rather than the expense of a full safety relay I used a standard one, supposed to do the same thing. I don't like the software estop for me an estop should de-energise the power/ enables off the drives. I don't want my safety relying on some flaky software so my estops are all hard wired, the program stops are left to stop the program only. i love the mod on your mill for me that's the perfect engineering solution it should look like it was built like that and it does. the best thing about the conversion on my mill has been the work I have been able to do it has not only paid for the conversion but the machine as well, the only reason I haven thrown it away and bought a bigger one is all the work I have put into it and I still find it useful so I can't really complain. For now I am sticking with it and might one day build a bigger one but I have some very nice loco's to build first. edit i have just checked and I did miss a wire it's now ok, my spindle enable goes through my "safety" relay as well as the board enable relay so double protection I think the charge pump is a handy feature and makes sense if you don't have a separate safety circuit. What you have sounds completely satisfactory to me, and that relay is never going to fail as a safety relay. I went to extreme lengths to make my machine as clean as possible. The limit switches are all small and tucked away underneath. I'm a big fan of direct drives to leadscrews too, but it's not always possible if you're on a budget. Good news about the spindle wiring then, that's another issue out of the way. I'm waiting for Mach4 to become stable enough to risk the changeover. I'm not an early adopter, it causes too many heartaches. I do want to completely customise my screen and get the pendant working how I want it too. I could do it with Mach3 but it's really painful to change the screens so I'd rather wait. What you've done the that little machine is amazing. What I've done is easy, but on a budget, things are totally different. It's great that you've paid for your machine too like I have with paid work. It's hard to imagine how I coped without it, it's been a real game changer.
|
|
|
Post by Roger on Jan 24, 2015 13:35:50 GMT
Ok, this turns out to be a quirk of mach3. The Relay Control had Disable Spindle Relays checked because I know that the PWM switches the relays and logically it didn't make sense to apply an Output# pin to them. It turns out that although this is true, the PWM doesn't start unless the Spindle Relays are enabled. I set the CW and CCW Output# to 1 and the corresponding Output Signal Output #1 as Disabled using Port0 Pin0. The system now works as expected.
|
|
|
Post by Doug on Jun 13, 2015 11:52:05 GMT
A little more progress on this, I have been wanting to add a 4th axis for some time and now it's almost a reality I have all the parts I need except a coupling This is going to be one of the smallest cnc rotory tables around  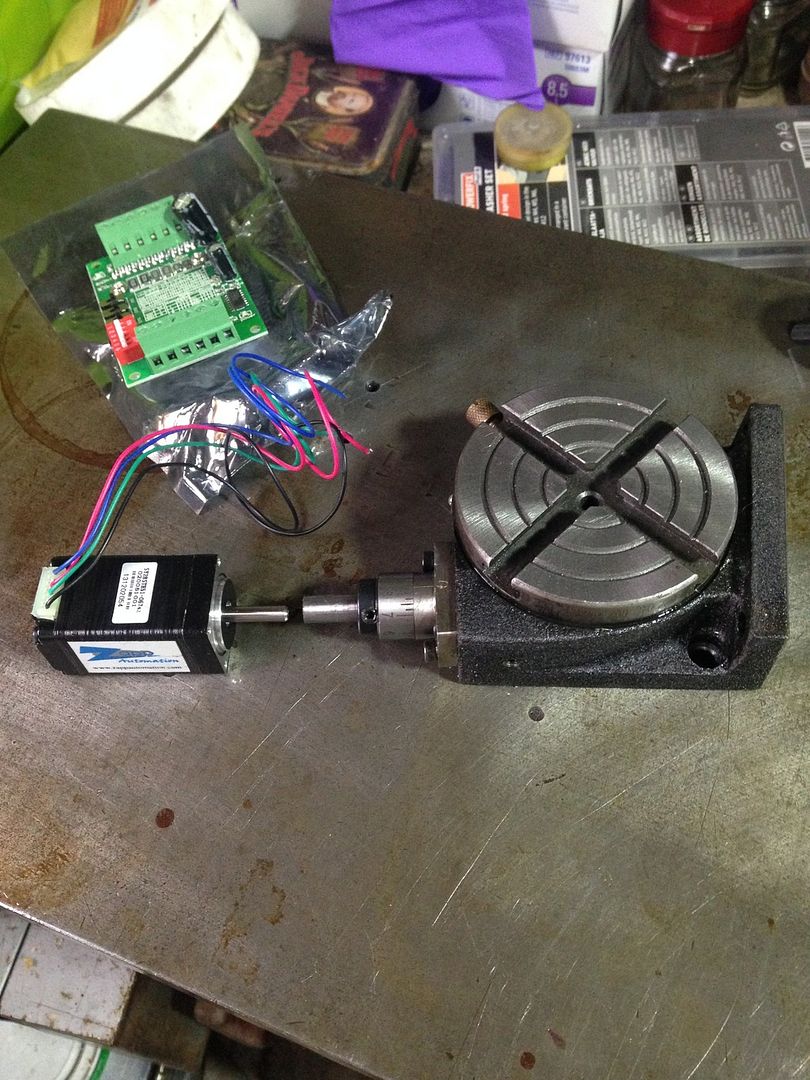
|
|
|
Post by GWR 101 on Jun 13, 2015 18:44:21 GMT
Hi Doug, I hope you don't mind me asking what might appear to be a silly question but what level of angular accuracy would you hope to achieve with that type of equipment, and is backlash a problem. Sorry that's two questions, regards Paul
|
|
|
Post by Doug on Jun 13, 2015 19:42:21 GMT
Hi Doug, I hope you don't mind me asking what might appear to be a silly question but what level of angular accuracy would you hope to achieve with that type of equipment, and is backlash a problem. Sorry that's two questions, regards Paul The first question is quite easy just simple ish maths; direct drive so motor connected direct to the worm one rotation of the motor is 10deg the steps on the motor are 180 per rev or 18 steps per deg which can realistically be chopped further by 8x (can do more but reliability gets a bit iffy and you can loose steps) so 18x8 =144 1deg divided by 114 which is very small indeed indirect drive say geared 2:1 then obviously double that regarding backlash this can be an issue however we have used a rather good method of reducing this at work by engaging the worm at the most slack part of the gear and then run the table for 24hours in both directions this wears the worm and wheel together to take out almost all the backlash. i have already run it in a bit and it improved the backlash to almost zero so another session should do it.
|
|
|
Post by GWR 101 on Jun 13, 2015 22:09:09 GMT
Doug thanks for taking the time to explain, I am well impressed both by the accuracy and the method to reduce the backlash. It's seems like something that will widen the scope of your miller and certainly a piece of kit that I will be considering for mine. Regards Paul
|
|
|
Post by Doug on Jul 26, 2015 12:15:16 GMT
A Small update to the mill I was using the mill a few weeks ago and I left it For a while while it was doing its thing and when I got back the z axis had lost its position this usually happens when the drive is in over current and the drive "slips" and looses counts. The problem is when I build the machine I had 1.25mm pitch screw on the z axis to it was geared very low indeed, not an issue as time is not important when I am milling. The new ballscrew on the z axis is a 5mm pitch so it's now lost the mechanical advantage it had. To overcome this and get back some of the lost gearing I have gone from the old direct drive and now have a belt drive. It is a 15/20 tooth ratio so it should give me a fair bit of extra torque. 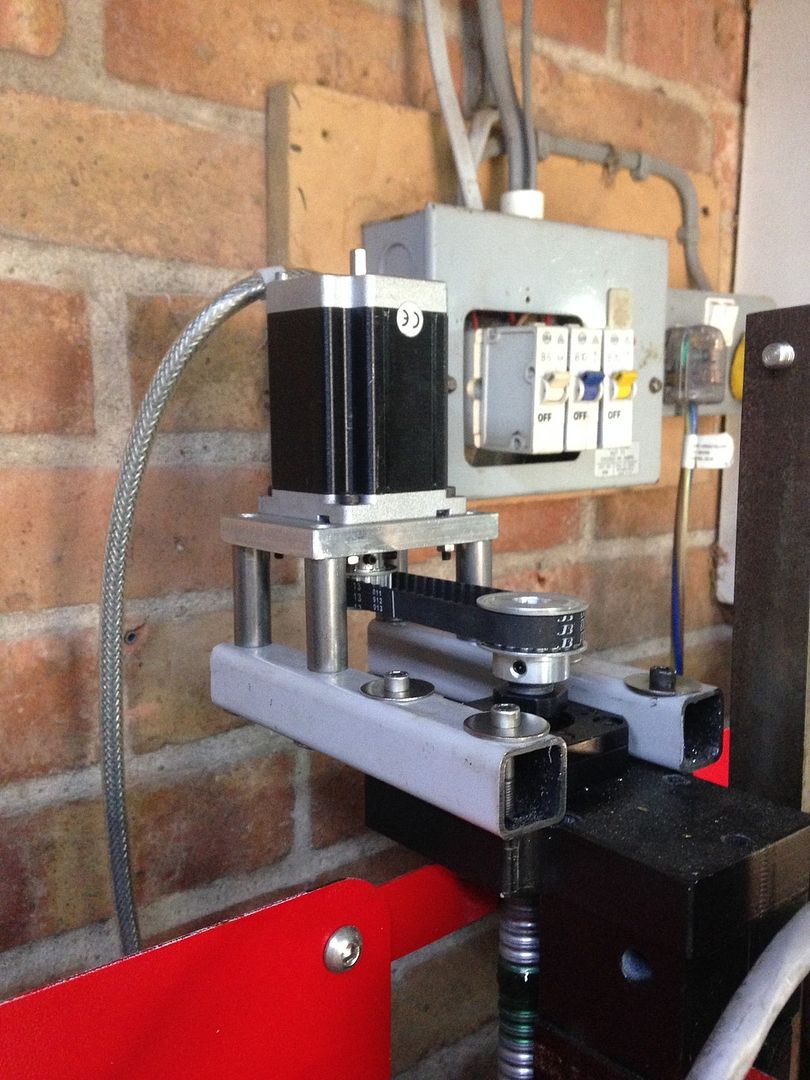
|
|
|
Post by Doug on Aug 1, 2015 16:41:26 GMT
Still not got round to fixing the c axis yet. I will have to get on this soon. anyhoo a mate came round with a large motor mount plate it had a hole 114.03mm and he needed 114.3 so I mounted it up and ran it round under size it was a little out and I had scaling issues. I managed to fudge the job so get it about right but it did show up the scaling issues I have so I set about fixing them. this is the setup I used 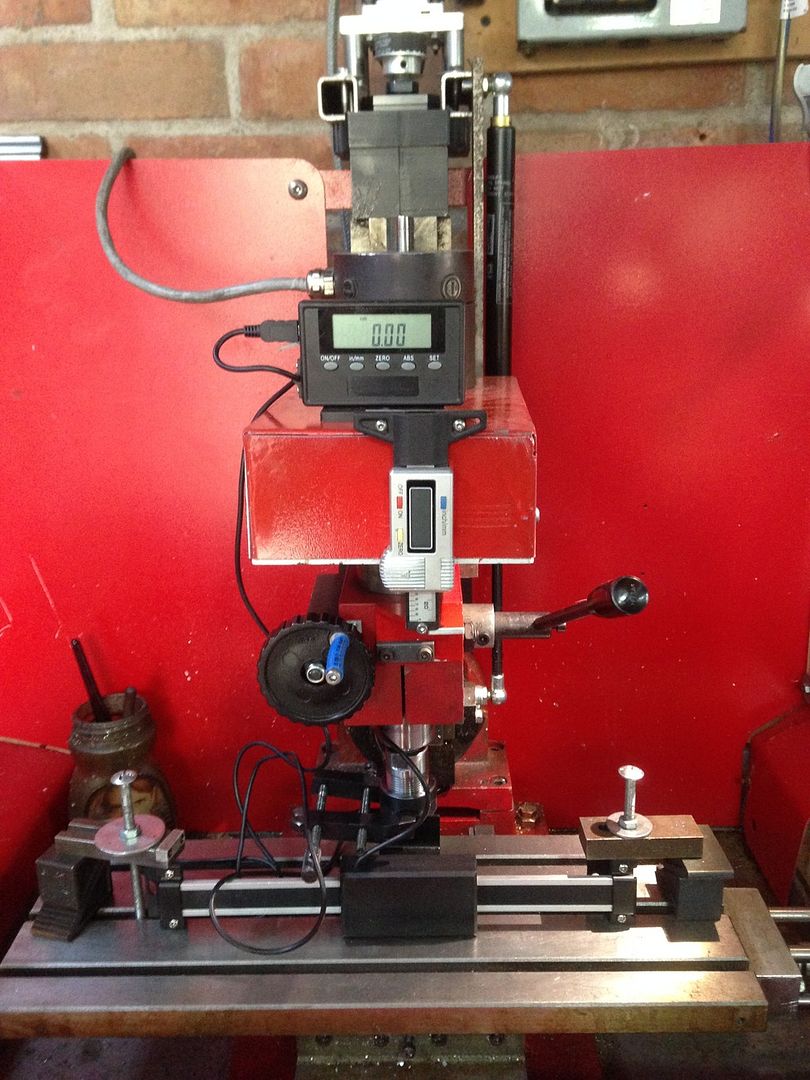 i checked over 150mm in both x and y and I have only 10um scaling issue. Backlash is now less than this, so any errors now are just deflection which on this mill can be an issue if I take heavy cuts so slow and steady it is. At last I have pretty good accuracy.
|
|
|
Post by jon38r80 on Aug 6, 2015 11:01:22 GMT
Doug and Roger I haven't posted on here before, I have read with interest what you have done and been very impressed with Rogers build diary. I ave a Warco wm16 mill school I have been considering adapting for numerical control. There is a great deal of information on the internet about CNC , even conversion of the Grizzly version of the mill in a lot of detail about making the metalwork. I am afraid that so far I have not been able to find a book or books that I can read about motor sizing, selection of controllers/power supplies separately or in combination and lastly the pros and cons of various bits of software. Your exchanges here about errors in software that irritate you prompted me to ask you if you able to recommend some reading. I am a Civil Engineer who just likes making things, anything. I am not a model engineer as such but have dabbled with RC pllanes and cars making better bits than stock for both. I have an em coming compact 5 lathe as well. along time ago I used to write engineering software for civil engineering design (a very long time ago when a mainframe had less power than the average desktop now) so perhaps have a different point of view than many. I look forward to a reply even if it's negative on the reading recommendation
|
|
|
Post by Doug on Aug 6, 2015 16:49:04 GMT
Doug and Roger I haven't posted on here before, I have read with interest what you have done and been very impressed with Rogers build diary. I ave a Warco wm16 mill school I have been considering adapting for numerical control. There is a great deal of information on the internet about CNC , even conversion of the Grizzly version of the mill in a lot of detail about making the metalwork. I am afraid that so far I have not been able to find a book or books that I can read about motor sizing, selection of controllers/power supplies separately or in combination and lastly the pros and cons of various bits of software. Your exchanges here about errors in software that irritate you prompted me to ask you if you able to recommend some reading. I am a Civil Engineer who just likes making things, anything. I am not a model engineer as such but have dabbled with RC pllanes and cars making better bits than stock for both. I have an em coming compact 5 lathe as well. along time ago I used to write engineering software for civil engineering design (a very long time ago when a mainframe had less power than the average desktop now) so perhaps have a different point of view than many. I look forward to a reply even if it's negative on the reading recommendation Hi as you mention there are very many way's to skin this particular cat, However you will be happy to hear that pretty much all of them work. so if you are considering CNC the first thing is software Mach3 albeit very slightly buggy is the best standard package out there it is used everywhere on routers lathes mills 3d printers etc etc. its not the best but then its not £15,000 worth like our heidenhains at work (which are VERY good). it is very useful to have a CAM package although this is not essential i would not be without mine again the type does not really matter, they all work and i cant recomend any specfic one as all that i have tried are quite good. lastly in the software part you need a drawing package again there are lots to choose from Autodesk is a fave of mine but not everyone likes it. htere are lots of free packages too but they tend to be a bit harder to work with. you only need to export the drawing to .DXF this is standard for CAM software. 3D machining gets a bit more tricky and needs an .STL file output but that is a whole diferent kettle of fish. next you need a PC to run your CNC software on (i tend to try not to do any drawing or post processing or CAM work on this as i like to keep the two operations seporate and my office chair is quite comfy) the PC does not neex to be very quick i run windows XP and the computer really needs a parralell port (this is not essential but non parrelell port interface cards are usually more expensive) controllers are varied in both functionality and cost Roger has a high end controller where as mine is at the low end again both will work and i have enough functionality on mine for what i need. motors and sizing them is not too dificult there is a very easy way and that is to find out what someone else has used on your type of machine the other way is to measure for this you need to know how much force is required to turn your hand wheel a 1m bar and a fish scale can give good results for this. bigger is always better though with motors. if like me you get it a bit wrong (my z axis dynamics changed when i swapped my lead screw for a ball screw) then you can always gear up the drive to give extra torque. power supplies were selected for the drives i use so a 10A 12volt system is enough to cover my requirements. the best thing if you are unsre is take it step by step and follow someones build. also dont expect to be throwing out amazing parts right from the off like all machining skills it takes alot of time to get to where Roger is with his machining its a total myth that CNC is easy its not its actually much harder to get right than conventional machining but the results in the end are worth the steep learning curve. all the best Doug
|
|
|
Post by Roger on Aug 6, 2015 18:31:13 GMT
Hi Jon, I don't have much to add to Doug's comprehensive answer. I think it's probably worth giving Mach4 a try now that it's been out there for a few months. It's a much more modern piece of software than the antique that is Mach3. I'd certainly use an Ethernet or USB connected controller whatever you choose, Mach4 expects the pulse generation to be done elsewhere, not on the PC which was always its Achilles Heel. The speed of the table movements isn't hugely important unless it's painfully slow in the rapid traverses. Mine's capable of 10M/Min which is frankly dangerous in our environment and I've clipped that to 3M/Min which I rarely use. The reason I have this capability is that it's a by-product of wanting to direct couple the motors to the end of the leadscrews for elegance and convenience. It's costly to do it that way though, mine cost £1000/axis because they are AC Servos. That's much more than most sane people would throw at such a conversion. Pass the straight jacket...
|
|
|
Post by jon38r80 on Aug 6, 2015 19:38:50 GMT
Gentlemen Thank you for your answers. You are echoing what I have read elsewhere, there are quite elegant cnc conversions out there. My aim was to try and understand the math behind the sizing of the motors and why one controller might be better than another. There is a lot about Geckos on the net but their website isn't that helpful. The PCs isn't a problem , one of my other pastimes has been assembling Pc's out of scrapped components. XP is ia much more stable platform than later windows operating systems, it was out there longer and most of its bugs ironed out. I have Autocad LT as I have done engineering drawings for the odd complicated component. I suspect that at the end of the day it will be the cost that stops at least for now anyway. There are some inexpensive packages of kit out there but I suspect that they are not powerful enough to drive the mill axes. Do you believe it is essential to have ball screws drives as they carry quite a hefty tag in the sirt of sizes I need? I expect your answer will be what sort of accuracy I need. The answer to that is not as tight as you do for steam work. Anyway thank you again for your clear answers.
|
|
|
Post by Roger on Aug 6, 2015 19:57:03 GMT
I think the stability of Win7 is about as good as it gets and I can surf the net, play streamed music and manipulate a massive 3D model while running the machine with the same PC. You really don't need to stay in the dark ages with XP for a CNC conversion, it's not necessary. For the maths you need to google about Moments of Inertia and apply that to the masses you have in your prospective system. I'm sure there are some online calculators for that so you don't need to do the maths. Don't forget that the motor inertia must also be included in any modelling. You need to decide what your maximum traverse speed is going to be and the rate of acceleration too. I didn't have to do any of this because my system was close enough to a system that I knew the motor sizes for. Personally I wouldn't use anything other than ball leadscrews if the machine is anything larger than Doug's machine. The bigger and stiffer the leadscrew, the more accurate it is and the less it will wear. You don't have to use the top grade ground leadscrews that I used, there are rolled versions that are less expensive. The biggest issue with ball screws is their size compared to the simple threads on standard machines. I had quite a job finding ones that were big enough to take the loads but with a small enough nut. The one for the X-axis still needed an angle grinder taken to part of the flange else it wouldn't fit. I'd wait until you completely strip down the machine to see what's commercially available in whatever screw style you choose and what will fit. I'd be inclined to make a 3D model of the machine so you can see that it all fits as expected. Don't forget that you also need to fit 6 limit switches and these can be tucked neatly away if you think about that at the same time as you are modelling the rest of the conversion. I think it would be fair to say that almost any motor is powerful enough to drive the mill axes, the issue is more to do with whether it can do it quickly enough to be satisfactory. Bigger is certainly better in my opinion but of course that costs more.
|
|
|
Post by ejparrott on Aug 7, 2015 16:14:21 GMT
I was going Mach3, but now I'm going over to Centroid, and ditching steppers in favour of servos.
|
|
|
Post by jon38r80 on Aug 8, 2015 19:20:12 GMT
I now have a lot of reading in front of me ( downloaded software manuals etc). You have all given more to ponder over than I had before. I like the idea of messing the force I need to over come stiction and inertia with a small spring balance and a stick. I've used that before to torque up tensioner so on a timing belt. As a Civil Engineer momements of inertia are no strangers to me but the other advice is appreciated. For the moment I am going to be a happy spectator following the build diaries on here which really do inspire. i have to ask, why servos rather than steppers?
|
|
|
Post by Roger on Aug 8, 2015 21:46:53 GMT
Steppers tend to be very bulky for the small amount of power they produce and they can stall and lose steps if you try to accelerate too quickly or something resists the motion. Servos don't suffer from these problems but they're more expensive. AC Servos offer the best performance in terms of size against power but are the most expensive of all. The ones on my mill are very small but immensely powerful. I also hate the noise of stepper motors, but that's an emotional reason rather than a rational one!
|
|
|
Post by jon38r80 on Aug 9, 2015 7:12:42 GMT
Roger Nice explanation why, I thought I read somewhere in your thread that you have to keep the power on to maintain position as they don't hold position like a stepper does,, I imagine that the only problem that may give is if for some reason you have to stop the machine, I like that they are smaller for a given power like most people on here my workshop doesn't have a lot of room. Small steppers sin printers, floppy drives and the like don't seem to make a noise so it's intriguing that that they do when scaled up. I presume that is some sort of electronic whine which would set your teeth on edge. I will look at the rolled ball screws that you suggest. The ones I have been looking at are probably ground judging by the price. It wasn't just the thread price that surprised me, the nuts aren't exactly pennies either. Size of the nut does seem to be a problem in conversions with bits of cast iron being consigned to swarf to get the opening in the carriage castings big enough. The y and z aces on my machine have a floating end (no support or bearing) presumably to keep cost down, less effort to align but it seems to me that it will wear the nut with or without ball screws from supporting the overhanging thread. Is that how it's done on your much larger machine?
|
|
|
Post by Roger on Aug 9, 2015 11:04:55 GMT
Hi Jon, You're absolutely right about keeping the power on to guarantee that they don't move. I'd never assume that the table was in the same place if I hit the Emergency stop or disabled the drives. In reality they don't move more than a few microns but it's not good to assume they are in the same place. Open loop systems assume that the machine follows every step and they are unaware if you turn off the servos and move them. I'd love to have a proper closed loop system but I haven't found one that's worth converting to as yet. You can overcome some of these problems if you have precision homing sensors that will allow you to find your way back to a machine reference position. I don't have those so I would have to clock the job up again. I don't find it a big problem in reality. I just leave the machine on, sometimes for days if I have a really long and complex part I'm making. I didn't think you could buy the rolled threads and nuts separately, for goodness sake never take the nut of or you will have balls everywhere. Every other ball is usually a different size so you'd have to sort them into two piles before reassembling! This is what my X-axis looks like and you can see how tight it is in there. Most ball nuts seem to have round flanges but I found these that didn't. The ends of the leadscrews are only supported when whirling is potentially an issue. That's unlikely to be the case if you use stepper motors because the speeds are usually quite slow. It's a big issue on servo machine where the traverse is high such as in the PCB industry where 10M/Min is considered slow. Most of those machines have now gone over to linear motors because it's impossible to get the required performance from even AC Servos. Mine has a supported end of the X-axis because it might be a problem at the highest traverse speed. I'm very unlikely to use that though. My ball screws have a 5mm pitch and you'll need to factor that decision onto your design process. Again I chose that because the machine I know to be similar used that too and it worked well. You definitely want to keep swarf away from the ball screws although many industrial designs just rely on the seals in them. I think it's asking for trouble, especially when you look at the cost of replacing them. I've seen PCB machines use them open like than and they get covered in fibreglass dust. Not exactly ideal. DSCN1548 by Roger Froud, on Flickr If you have a rummage around this album you'll see what my machine is like in pieces and what I did with it. Some of the pictures I took before modification so I had a record of how it all went together!
|
|
|
Post by jon38r80 on Aug 9, 2015 14:16:41 GMT
Roger Once again many thanks for sharing your own experience. a browse through your photographs was an education. Since you got rid of the blue swarf tray I presume you always machine dry. (That is my preference as well) due you run with a work shop vacuum clearing dwarf or just let it build up and deal with it the end. The components you made for the conversion and for the high speed spindle are as impressive as the parts for your steam engine. As with others here I have adopted machining all but the last half mill and then finishing by hand as you have demonstrated works so well. I will probably end up using step motors rather than servos due to the budget.
|
|
|
Post by Roger on Aug 9, 2015 19:15:05 GMT
Hi Jon, You're most welcome. I'm very much aware that my conversion was much more expensive than most people would find acceptable. Doug has amply shown that it's possible to do something on a much smaller budget without compromising much. High traverse speeds have little benefit, and in my opinion 0.5M/Min is adequate for fast moves although 1M/Min is preferable. Much more than that can be scary, especially when you consider that most jobs are one offs and your first run is to prove the program and hopefully make a part! I rarely cut metal above 100mm/min and I can't remember ever cutting anything at more than 250mm/min
I've actually retained the blue swarf tray but you're right, I don't use lube other than from a brush. I'd love to use running coolant but it makes a shocking mess unless you're prepared to sheath your machine all over in catch wings and guards. I don't have space for all of that so I tend to run slowly by comparison to how I might do with full lube.
Machining as much as possible saves so much time, not just in the process of removing the metal, but in the time saved in subsequent operations to make things fit and spotting through which is largely unnecessary. There's absolutely nothing wrong with stepper motors, they work well when sized correctly and it's hard to argue with the cost. I look forward to seeing what you come up with, it's a big decision but you'll be thrilled with what you're easily able to make.
|
|