|
Post by Doug on Jul 9, 2014 9:57:13 GMT
I'd be inclined to use a lower force than necessary for a complete balancing, you may as well use the weight of the head to help with the backlash. A lot of the high speed spindle designs are pretty grim technially. Kavo and Jaeger are pretty awful although they look good on the outside. Have a good look and find some users before you spend hard earned cash on something. oh and regarding the spindle i have a plan  i am thinking router, a cheap cheerful method that will have its own speed control etc that i can mount on the side of the mill head with a 24k spindle and 6mm collet already attached
|
|
|
Post by Roger on Jul 9, 2014 10:38:03 GMT
Sounds about right to me. I suppose you could set the machine at a jaunty 45 degrees in the X and y axes too and use gravity for your anti backlash system there too. 
|
|
|
Post by Doug on Jul 10, 2014 22:11:25 GMT
Ok all but done now I just need to get some aluminium bar for the z axis pillars and I am finished (with the main build) I still have lots and lots of mod's to do like the spindle upgrade and coolant etc. here is a pic of the gas assist ram it seems to work well I have a small amount to fitting to do to check the position of the ball screw but for the most part it's completely done. 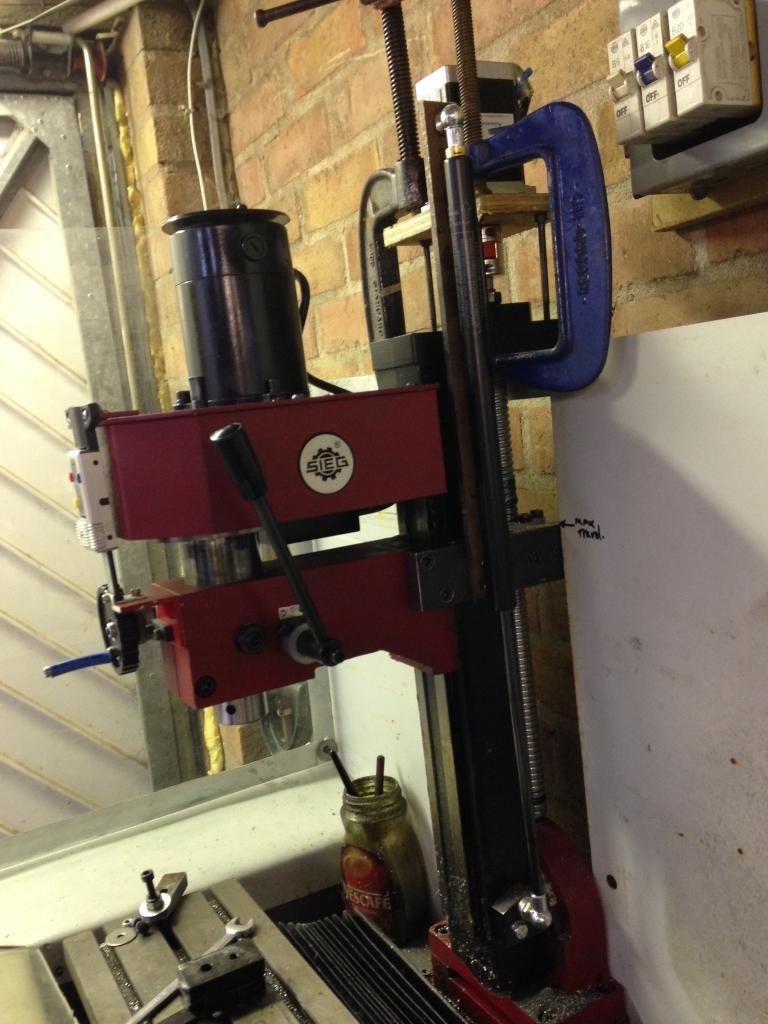 It is nice and neat and fitted upside down to prevent coolant and swarf getting at the seals. i can get on with loco bits now while I wait for my aluminium bar.
|
|
|
Post by Roger on Jul 11, 2014 6:37:13 GMT
As you say, that's very neat. Actually, by accident you've mounted that the recommended way up. You're supposed to have them that way so that the seal always has the working fluid in contact with it. That's why some of these fail prematurely, they're mounted the wrong way up. They don't last forever as it is, but you'll probably get at least five years out of it.
|
|
|
Post by Doug on Jul 12, 2014 21:07:50 GMT
A little celebration today this chapter has come to a close and my CNC is finished  Obviously as with pretty much everything I own I will be modifying it in the future but I can now say it's built and working well my next jobs can be Speedy related I have quite a few tasks I would like to get done. Then I really need to get my cylinders done. anyway a final shot of the z axis motor mounting 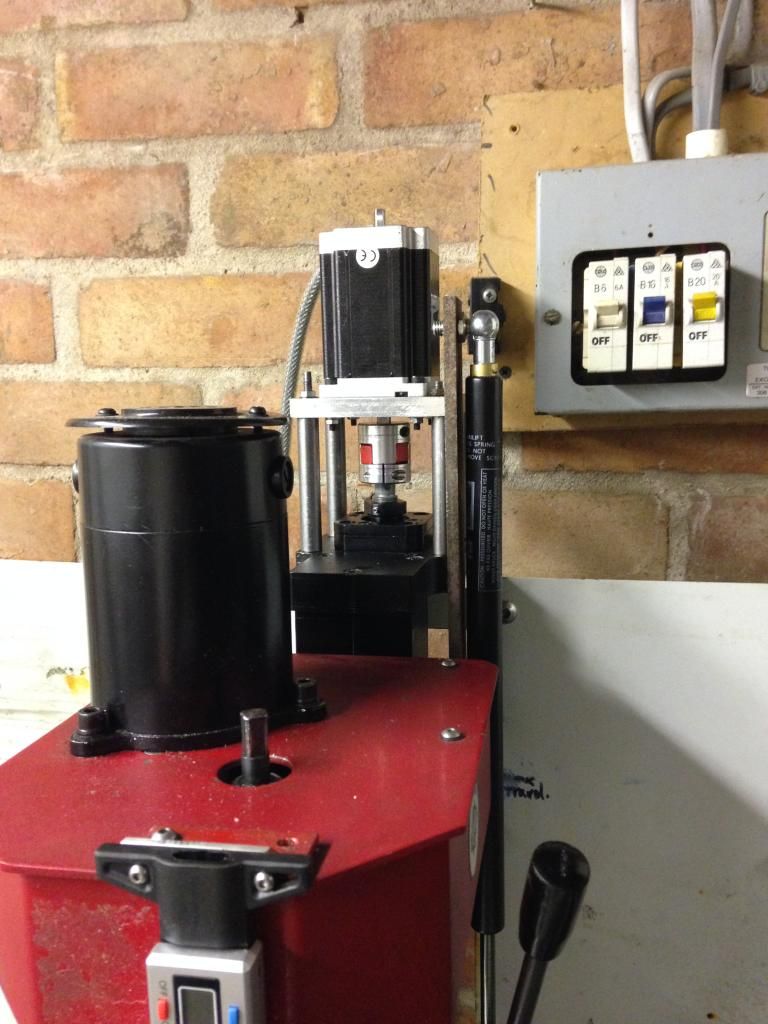
|
|
|
Post by Roger on Jul 12, 2014 21:39:19 GMT
I'm really impressed with what you've done with this neat little machine. You've turned it into something that is in a totally different league to what it was, you must be delighted.
|
|
uuu
Elder Statesman
 
your message here...
Posts: 2,858
|
Post by uuu on Jul 13, 2014 6:38:17 GMT
I'll second that. You'll be able to do all sorts with it.
Wilf
|
|
|
Post by Doug on Jul 13, 2014 7:09:19 GMT
Thanks guys I am really happy with it. It has impressed me already with what I can now do, that was impossible/very difficult before the only limit now is my imagination really. The biggest gain from doing this is that the 5" loco is now in its machining capability where before just about every job was too big for it.
|
|
|
Post by Roger on Jul 13, 2014 7:17:05 GMT
I guess that's because it's practical to take loads of small cuts on big pieces of material and that really isn't practical when you're turning handles. I'll be very interested to see what you make on it.
|
|
|
Post by Doug on Sept 6, 2014 12:23:58 GMT
Ok it's been a while since I updated on this and a lot of refinement and learning has taken place, I have now setup and use the backlash comp on Mach3 the repeateablity is spot on and comes to zero on my 10 um clock so no dramas on that front, I have had an issue with the z axis getting overloaded and slipping (missing counts due to being in current limit on the drive) this was caused by a twist on the z axis ball nut mounting plate, a very easy fix and very silly mistake, I should know better always good to check every thing twice before tightening up! any way ended up with some very profitable work once my work had got wind of the fact I now have CNC they asked me to do some work for them (about 15 hours worth!) even got supplied with a cutter and fixture i have been making good use of my new ER20 collets too I got two nuts for it so the tool swaps are very quick. i need to make a spindle lock for it though two spanners is a pain. 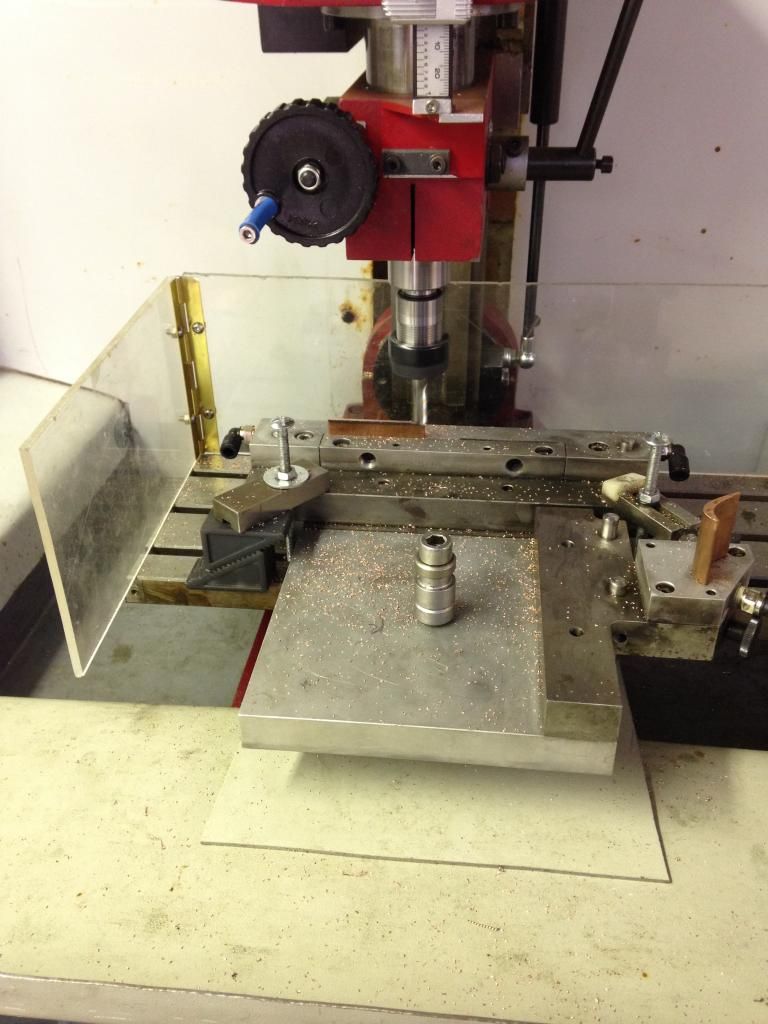
|
|
|
Post by Doug on Sept 6, 2014 20:24:50 GMT
I have just spent the afternoon adding a couple of buttons "cycle start" and "cycle stop" to the front of the machine I have added another hole for an extra e-stop as well. Mach 3 allows all the functions to be added externally via the I/O system so it's not too difficult to do. Having these buttons on the front means I don't have to fiddle around with the mouse to get to the start and stop buttons while my hands are greasy or dirty I can just press and go.
|
|
|
Post by Doug on Sept 11, 2014 6:08:49 GMT
Not finished yet still got loads to do but I have been making massive progress this week, got the guard painted and started on the button enclosure 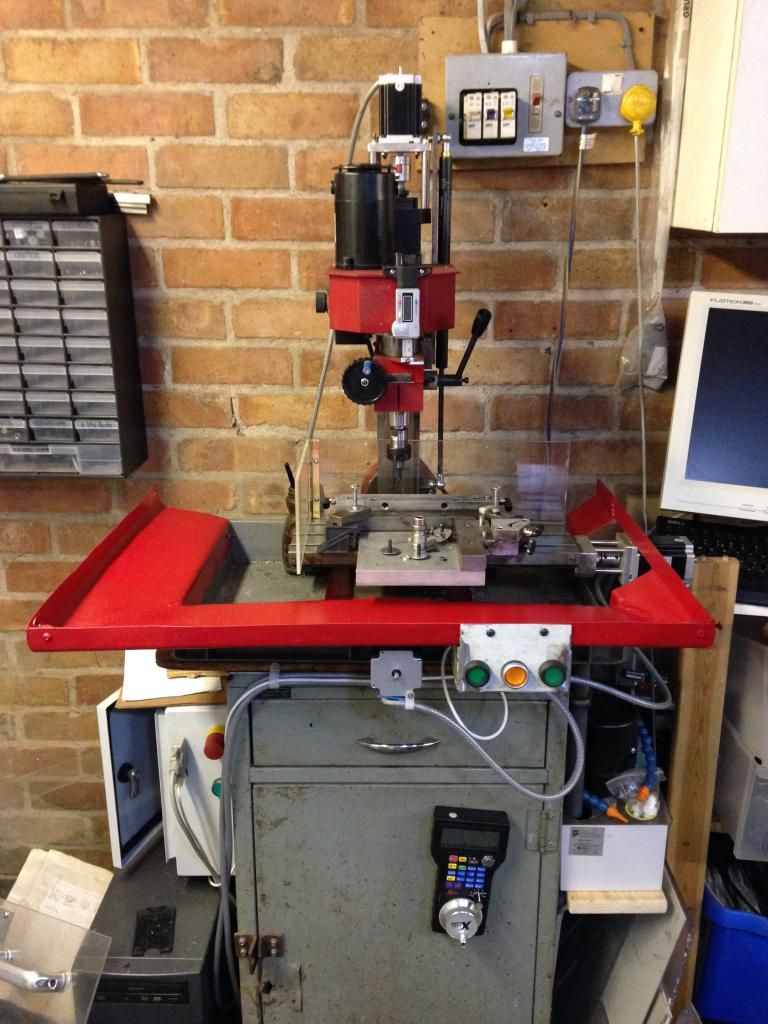 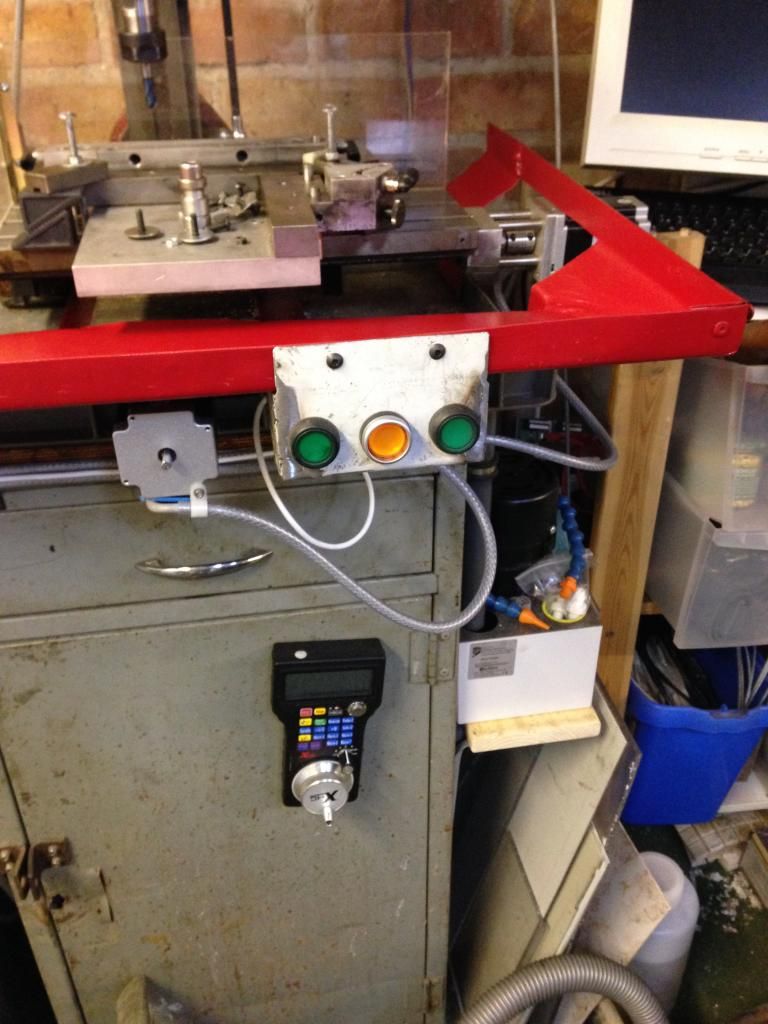
|
|
|
Post by Roger on Sept 11, 2014 13:10:26 GMT
That's neat and tidy Doug. I meant to ask you how you were getting on with the MPG and Mach3? I'm using the Aqua skin and the MPG implementation is rubbish. I'm going to have to get on and finish my own custom version of that and make it do what I want. The modes and what they do seem to have a mind of their own!
|
|
|
Post by Doug on Sept 11, 2014 17:23:05 GMT
That's neat and tidy Doug. I meant to ask you how you were getting on with the MPG and Mach3? I'm using the Aqua skin and the MPG implementation is rubbish. I'm going to have to get on and finish my own custom version of that and make it do what I want. The modes and what they do seem to have a mind of their own! I didn't like the screen set on Mach3 so I have also moved over to the aqua screen set the buttons and displays just make more sence. i don't get the mpg modes at all I just use continuous and step jog on the mpg. I want to program some of the buttons to have a plus and minus direction button so I will need to get into the macro program's at some point. i have been porting some buttons off the screen into "real buttons" that I can press which make the machine more like a regular CNC. the whole setup allows full access to all parts of the control so you can make it what you want really which I like a lot. i have a lot of hardwear upgrades to do before I get into the control though. I want a direct belt drive spindle before I do anything else. My plate is full to overflowing with jobs at the moment though as I have a factory move to plan at work, two trains I am building and a very active family life to juggle so spare time for more projects however interesting is a bit of a big ask.
|
|
|
Post by Roger on Sept 11, 2014 18:29:13 GMT
I think Mach 3 is a joke to be honest when you think how long they've had to sort it out. They've tried to do too many things with it and ended up not doing anything properly. Although you can change the button functions easily enough, you can't easily change the graphic layer to suit. I don't know if you've played with the screen builders but it's a nightmare. I've recreated some similar looking buttons and effects as the Aqua set and mine will eventually look like a simplified version of that. At the moment I'll live with it. I don't know what you think of the way you have to start part way through a program, but in my opinion it's bloody dangerous without having much idea where it's going to rapidly charge off to next. At the moment I'm avoiding using that because it's an accident waiting to happen. I'm crazy busy too so I'm not getting much done on SPEEDY either. I will try to make some progress on the axle pump this weekend if I can though. I need to see some progress, however small.
|
|
|
Post by Doug on Sept 11, 2014 18:53:17 GMT
Haha I think your software bar is set way too high I have had a lot worse to deal with. i do find it very buggy especially when you use the "start from" function however the work around is to press cancel when the prep move mini tab comes up and it jus starts from where it is currently, I will at some point find the macro that is this mini program and remove the mini tab as I can see no useful need for it. your progress on speedy is well speedy if you take a look back a year and see how much you have got done the work rate for a hobby is very impressive indeed, I have started with half a loco and you are nearly up to the same point. The pump design looks pretty good with your usual modern bent on the design. Anyway a bit more progress 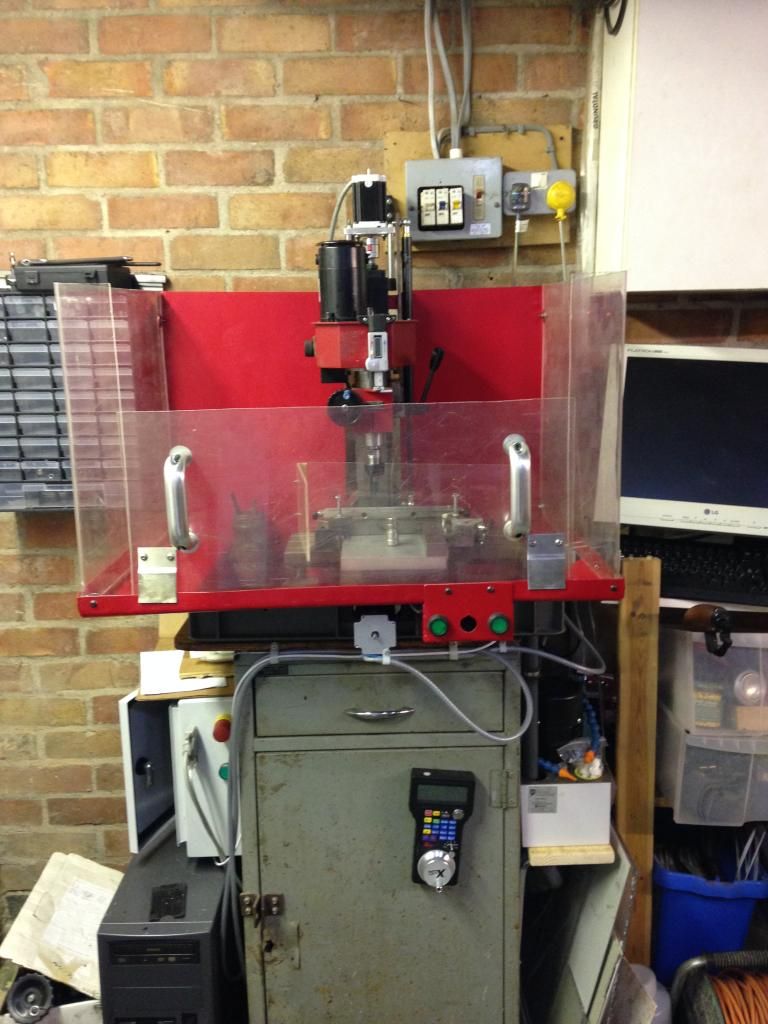 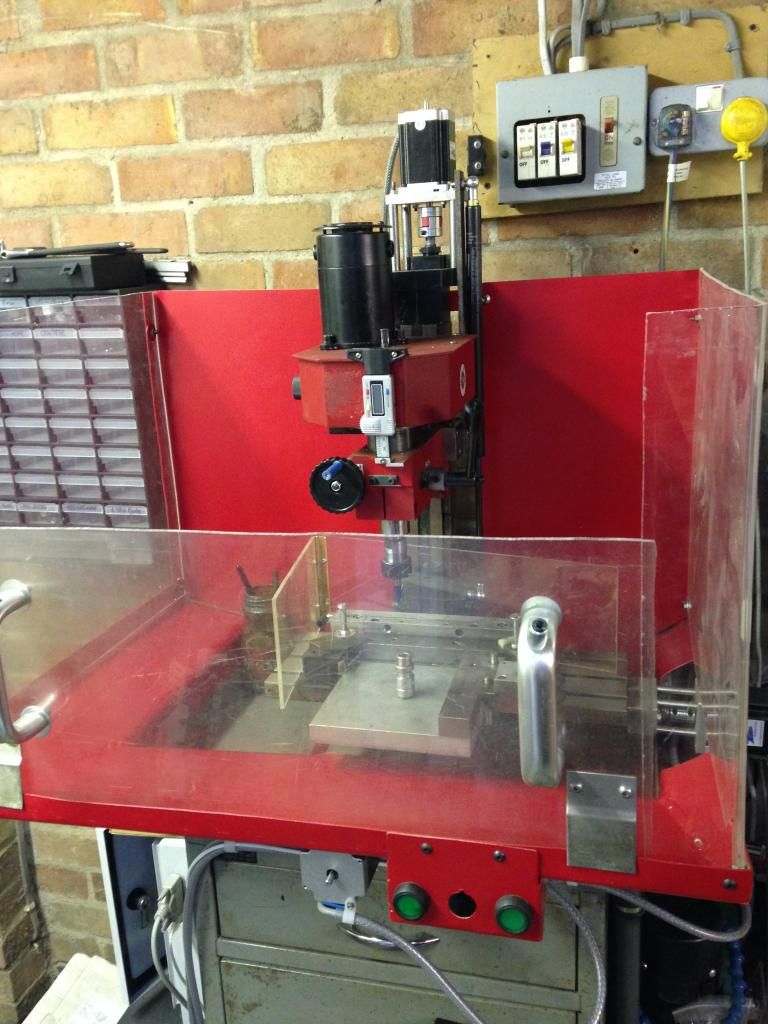
|
|
|
Post by Roger on Sept 11, 2014 19:13:09 GMT
Well, I had to design a CNC for the PCB industry, and that had to go all over the world. The last thing you can afford is for it to be flaky. I can't say there are no bugs in it, but you'd have to really try to break it to find one. With Mach 3, you only have to sneeze and it does something unexpected. Lets hope they finally do make Mach 4 but I'd like to take a bet that they won't ever release it into the wild.
|
|
|
Post by RGR 60130 on Sept 11, 2014 19:49:17 GMT
Mach 3 has always worked for me every time without doing anything unexpected. I haven't tweaked it at all and just use a very simple ShuttleXpress pendant.
It does just what it says on the tin for me.
Reg
|
|
|
Post by Doug on Sept 11, 2014 22:17:03 GMT
Hi Reg I think Rodger is talking about the very silly habit it has of doing a pre start move if you jump to a line in the program and I have fallen fowl of it myself say you want to run the program from half way through you pick the line number and hit the run from here button it then has a dialog box that tells you the cord. For it's pre start move so if you press ok it just runs off to a (what I would describe as random) new position before it starts to run which you need to press cycle start for. It's a silly macro I have never seen on any normal CNC and I can't think why on earth they put it in. It made me scrap a bracket I was making when I was building the machine. other than that little foible and the fairly silly MPG (which could be a lot simpler and better IMO) I really like it.
|
|
|
Post by Roger on Sept 12, 2014 8:03:14 GMT
There's also an anomaly when you turn the spindle on and off manually or with the M03 and S1000 for example on the MDI. Sometimes it enables the spindle but doesn't output an analog value so the spindle just sits there whistling. There are other things that aren't right too. If you just run a program from start to finish it does behave itself though.
|
|