|
Post by Cro on Aug 6, 2019 6:12:35 GMT
It machines very much like silicon bronze. As with most materials, you need sharp tooling but it does machine nicely. When I said hard, I meant in terms of its elasticity; it has a much higher Young's modulus and therefore is more springy unlike Silicon bronze which yeilds at much lower pressures. I have a 4mm diameter rod of it and one of silicon bronze which I show people. The silicon bronze rod is easily bent between thumbs and fingers but everyone struggles to bend the white bronze one. I tried, its amazing the difference! It will be perfect for this sort of component. Adam
|
|
|
Post by ettingtonliam on Aug 6, 2019 6:54:50 GMT
Is there are significant cost difference?
|
|
|
Post by 92220 on Aug 6, 2019 7:33:01 GMT
Lovely castings Mike. I wish I'd known you when I was fabricating my brackets!!
Bob.
|
|
|
Post by Jim on Aug 6, 2019 8:20:56 GMT
Mike's craftsmanship is second to none and his fully detailed BR Mk1 passenger coach would pass for the real thing. A true master modeller.
Jim.
|
|
44767
Statesman

Posts: 538
|
Post by 44767 on Aug 6, 2019 12:13:36 GMT
Is there are significant cost difference? At the precious metal foundry where these are cast, the unit cost for the casting is the same no matter what metal is cast. The price for the metal itself is then charged on top. For white bronze the cost per gram is NZ$0.25. Silicon bronze at this foundry is NZ$0.10 so more expensive but not a lot when most of the castings I have done are only 20 grams or so. At the foundry I use most often as it's only seven minutes drive from home, the price per gram for silicon bronze has just gone up from NZ$0.06 per gram to NZ$0.40! So it will actually work out cheaper than the new price.
|
|
|
Post by steamer5 on Aug 7, 2019 0:40:36 GMT
Hi Mike, Boy that is some price jump! Still that casting looks fabulous! Sorry to back track, but seeing your springs begs the question, how’d you arrive at the amount to cut out? Recently had the opportunity to check out another loco that had the same idea done to the springs, ready to roll weight around 300 kg, & I forgot to ask !
Cheers Kerrin
|
|
44767
Statesman

Posts: 538
|
Post by 44767 on Aug 9, 2019 11:55:26 GMT
Hi Mike, Boy that is some price jump! Still that casting looks fabulous! Sorry to back track, but seeing your springs begs the question, how’d you arrive at the amount to cut out? Recently had the opportunity to check out another loco that had the same idea done to the springs, ready to roll weight around 300 kg, & I forgot to ask ! Cheers Kerrin Hi Kerrin, I started off by working out the distance from where the axle box is on the keep i.e. no weight on the loco to the working height. This was 3.5mm for my model. I added a bit so that if there was no weight on the loco, the springs would still have a bit of preload on them so that the pull rods would not go slack. I made it 4mm then. Then I estimated the weight on each spring by taking the full weight of the full size loco (76000 kg) and dividing by the cube of the scale (11.3) this gave an estimated weight of the model of 52kg. Now, I assumed that 3/4 of the weight was on the 6 driving wheels which meant that there was 6.5kg on each driver. So I needed a rate that would give 4mm of travel for 6.5kg or 1.625mm per kg. Unscientifically, I had a guess at how much of the spring material had to be removed from each leaf. I guessed leaving a strip of 1.5mm down each side looked about right. I got a set of leaved laser cut, bent them to the required radius and assembled them into the buckle. I tested the deflection by hanging a bucket underneath the spring, which was upside down, and adding 500ml of water then measuring the deflection with a DTI. Readings were taken for each additional 500ml of water. The first set needed 13kg to deflect 4mm so I had another set made with only 1mm wide strips. This, although very linear in its deflection still only gave 3.0mm of movement for 6.5 kg. The width of the strip, I thought, should not be reduced further so I had to do the mathematics where the deflection is inversely proportional to the cube of the thickness. When I did the calcs, I found the thickness needed to be reduced from 1.2mm to 1.09mm. I did this on the surface grinder (on a new set of leaves before they were cut from the fret). I found this to give exactly the deflection I required. A bit of trial and error and a bit of maths got me there in the end.
|
|
|
Post by steamer5 on Aug 9, 2019 13:07:09 GMT
Hi Mike, Thanks for the info....looks like I'll need to brush up on my maths!
Cheers Kerrin
|
|
|
Post by silverfox on Aug 9, 2019 17:20:52 GMT
Mike
If i end you all the weights and dims,could you work put mine please? (lol)
However daft question
Are they spring steel or ordinary stuff?
Ron
|
|
44767
Statesman

Posts: 538
|
Post by 44767 on Aug 9, 2019 20:52:48 GMT
The leaves are made from pre-hardened and tempered 18 gauge spring steel sheet. They are formed after the thickness has been reduced and removed from the fret.
|
|
44767
Statesman

Posts: 538
|
Post by 44767 on Jul 16, 2021 9:50:51 GMT
|
|
44767
Statesman

Posts: 538
|
Post by 44767 on Mar 20, 2022 8:55:53 GMT
There's been too much water under the bridge! Here is the latest part I've been working on. It's the smokebox saddle and although it was one of the first parts I started working on, it has taken a lot of time to get to a final design of this part. Any way, here's the part now machined and ready to fit between the frames along with all the other stretchers.  This shows the part mounted on a sub-plate which, in turn, is bolted to a universal fixture I made a while ago to fit directly to the spindle nose of my Hofmann dividing head. This saves having a fixture held in a 4-jaw chuck which saves a lot of unnecessary overhang. I'll try to fill in the gaps leading up to here but I was so happy with the way this turned out that I just had to show it! Cheers,Mike
|
|
44767
Statesman

Posts: 538
|
Post by 44767 on Mar 20, 2022 10:04:37 GMT
Here are a few images of what has been happening over the past months. It's all coming together quite well now and as I go, there are a few "standard" bits which get developed, which anyone can make use of- e.g these sanding nozzles which were common on most steam and some diesel locomotives.  Front buffer beam and buffing gear. A lot of standard parts here!  front horizontal stretcher, as yet unmachined. 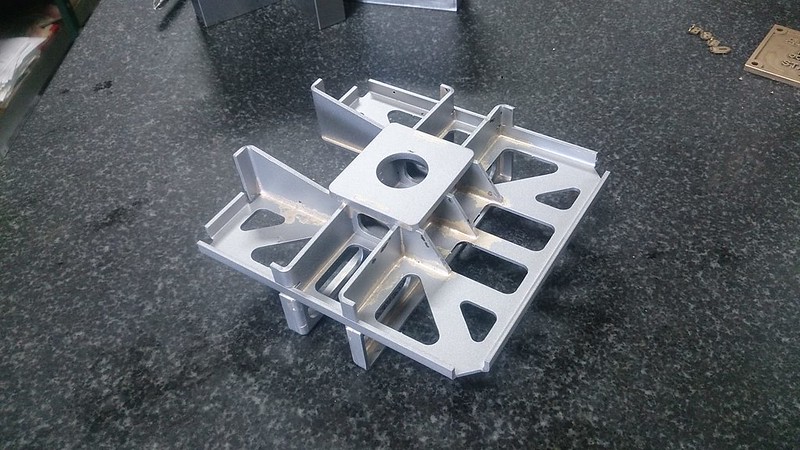 The front and rear pony truck pivot stretchers. These used the new press brake and took full advantage of its micrometer-adjustable fence and limits. 
|
|
44767
Statesman

Posts: 538
|
Post by 44767 on Mar 22, 2022 6:05:50 GMT
Today I received some pictures from one of the builders in the UK. He is my guinea pig and gets to machine and fit the parts from my drawings and materials before I get to the main batch of them. This way I can hit the ground running and everyone should get 100% accurate drawings as a result as we refine the drawings and materials to suit. I had developed a press tool to roll the edges of the driving wheel balance plates. These are positioned each side of the wheels with rivets, in full size, but here they are split into two parts with male and female threads to sandwich the plates onto the wheels. The heads have a 60° taper under them which bites into the plate's countersunk holes and so allows them to be tightened. One side has a drive portion which shears off leaving the slightly domed head showing on the inside of the wheel and a flat head, slightly proud, on the outside. The inside of the main wheel showing the "rivets" holding on the balance weight plates.  The outside of the same wheel  A trailing or leading wheel showing the drive portion of the screws before they were sheared off.  And a photo of 82045's wheel set at Bridgnorth for comparison.  I'll find the photos of the press tool I developed to roll the edges and get them up here too. Cheers, Mike
|
|
44767
Statesman

Posts: 538
|
Post by 44767 on Apr 9, 2022 10:38:37 GMT
My attention has turned to piping of the boiler and smokebox. Here is an image of the piping in the smokebox (with the smokebox ring hidden, for clarity). One can see the ejector piping including the drains, the blower and ejector connections, the main steam pipes and the blast nozzle cap and ejector ring around the petticoat pipe. Also visible are the superheater elements and manifold. The blasts from the blast nozzle and the blower are represented too.
|
|
44767
Statesman

Posts: 538
|
Post by 44767 on Jun 5, 2022 11:12:13 GMT
Jumping ahead a bit but this is what I've been working on for the last couple of days. I will soon need to machine the motion brackets which support the rear of the slide bars and supports the expansion link pivot brackets. I think this is the most difficult casting to hold for machining and, since the machining is critical, I have gone about adding to my collection of small clamping elements. The first new addition to my small clamping system was is a plate with a matrix of M6 tapped holes over its whole face. See it here with the motion bracket being set up for the initial skim of the pads.  The C-frame is not supported here so side clamps were made to stop it moving while machining took place. Note the finger clock used to make sure it does not move from its relaxed position while the clamps were tightened. This means it is not strained, and therefore remains true when the clamps are released.  These side clamps were made for the third op and have curved slots to allow for about 30° of swivel.  The bracket now set up for the second operation:    I thought I'd better see if I could machine it the way I had described on the drawing so I set the fixture plate I made the other day on my rotary table. This will not be necessary in the production run as I can machine all the features in one set up on the machining centre but so that the set up can be rotated without disrupting the clamping, I suggested doing it this way. In fact, the rotary table is not necessary if you have a separate fixture plate like mine. The first set up is with the C-frame parallel with the machine and the centre of the C-frame is found for one datum, Y and the centre between the bosses for the slide bars is the other, X. Also Z is the centre of these bosses too. The machining for the ends of the slide bars is done and the hole in the mounting flange is bored to the coordinates given on the drawing as well as two dowel holes. The set up can now be rotated and clocked true to the two dowel holes. The centre of the bored hole is found and the X and Y datums calculated back from here. Z is moved from that in the first op to be the finished mounting flange. This face is now machined, with its shoulder and all remaining holes drilled. It sounds complicated but I think it will work OK. Here is my first off set of frames, assembled to prove the side plates. Now I can alter the laser cutting profile to incorporate all holes added since these were cut. 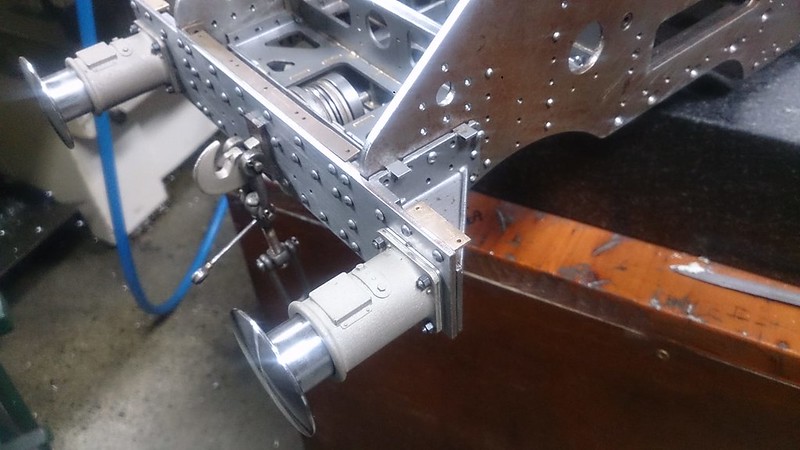  Note the pillars to space the frames, make them parallel and in the correct position. I can explain if anyone's interested. Mike
|
|
|
Post by 92220 on Jun 5, 2022 11:27:33 GMT
Those frames look superb Mike!! Brilliant job!!
Bob.
|
|
44767
Statesman

Posts: 538
|
Post by 44767 on Jun 6, 2022 13:37:29 GMT
Here's a bit more done over the last few days. The motion brackets are tricky to fixture so I set about adding to my collection of small clamps etc. so that I could machine these safely and accurately. Here are the two brackets, still with machining to do, temporarily attached to the main frames. ![]()    I'm taking this set of frames to the laser cutter tomorrow to show everyone there what I've been up to. Cheers,Mike
|
|
|
Post by David on Jun 8, 2022 1:28:43 GMT
Beautiful!
|
|
|
Post by suctionhose on Jun 10, 2022 6:29:57 GMT
In your boiler CAD above, why do you have the steam dome protruding so far into the boiler? It will suck water up like a tornado...
|
|